A kind of heat treatment method of 55nicrmov7 roller table roller
A heat treatment method and roller table technology, applied in the field of heat treatment of rolls, can solve problems such as unsuitable processing of thread holes on the end face of roll necks, high labor intensity of operators, hidden dangers of quenching oil fires, etc., and achieve good comprehensive performance, ensure hardness uniformity, The effect of cost reduction
- Summary
- Abstract
- Description
- Claims
- Application Information
AI Technical Summary
Problems solved by technology
Method used
Examples
Embodiment 1
[0038] The 55NiCrMoV7 roller bed has a diameter of 273mm and a length of 500mm. The following are the process steps of quenching:
[0039] 1) Induction preheating: Inductively heat the roll on an intermediate frequency quenching machine tool. During the induction heating process, the operating speed is 75mm / min, and the reciprocating linear motion is made along the roll body to perform cyclic induction preheating on the roll body of the roll. The induction frequency 750Hz. Induction preheating is heated to 500°C to complete the preheating of the entire roll body.
[0040] 2) Induction heating: Continue to use the intermediate frequency quenching machine tool for induction heating. During the induction heating process, the operating speed is 75mm / min, and the reciprocating linear motion is made along the roll body to perform cyclic induction heating on the roll body of the roll. The induction frequency is 830Hz. Heat the roll to 850°C for full austenitization and keep it warm...
Embodiment 2
[0046] The 55NiCrMoV7 roller bed has a diameter of 205mm and a length of 600mm. The following are the process steps of quenching:
[0047] 1) Induction preheating: Inductively heat the roll on an intermediate frequency quenching machine tool. During the induction heating process, the operating speed is 55mm / min, and the reciprocating linear motion is made along the roll body to perform cyclic induction preheating on the roll body of the roll. The induction frequency 530Hz. Induction preheating is heated to 580°C to complete the preheating of the entire roll body.
[0048]2) Induction heating: Continue to use the intermediate frequency quenching machine tool for induction heating. During the induction heating process, the operating speed is 52mm / min, and the reciprocating linear motion is made along the roll body to perform cyclic induction preheating on the roll body of the roll. The induction frequency is 560Hz. Heat the roll to 880°C for full austenitization and keep it wa...
Embodiment 3
[0054] The 55NiCrMoV7 roller bed has a diameter of 255mm and a length of 1000mm. The following are the process steps of quenching:
[0055] 1) Induction preheating: The roll is heated by induction on a medium frequency quenching machine tool. During the induction heating process, the operating speed is 30mm / min, and the reciprocating linear motion is made along the roll body to perform cyclic induction preheating on the roll body of the roll. The induction frequency 200Hz. Induction preheating is heated to 700°C to complete the preheating of the entire roll body.
[0056] 2) Induction heating: Continue to use the intermediate frequency quenching machine tool for induction heating. During the induction heating process, the operating speed is 30mm / min, and the reciprocating linear motion is made along the roll body to perform cyclic induction preheating on the roll body of the roll. The induction frequency is 200Hz. Heat the roll to 940°C for full austenitization and keep it w...
PUM
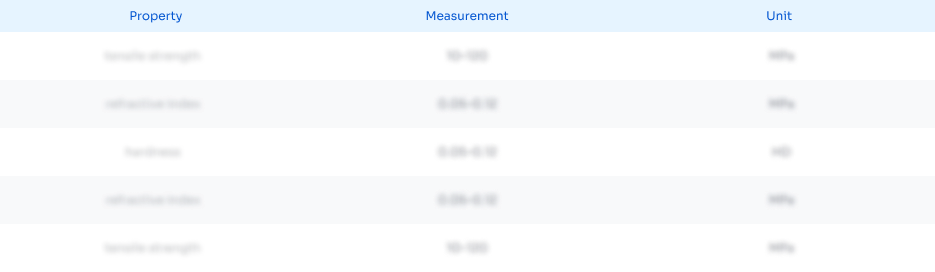
Abstract
Description
Claims
Application Information

- Generate Ideas
- Intellectual Property
- Life Sciences
- Materials
- Tech Scout
- Unparalleled Data Quality
- Higher Quality Content
- 60% Fewer Hallucinations
Browse by: Latest US Patents, China's latest patents, Technical Efficacy Thesaurus, Application Domain, Technology Topic, Popular Technical Reports.
© 2025 PatSnap. All rights reserved.Legal|Privacy policy|Modern Slavery Act Transparency Statement|Sitemap|About US| Contact US: help@patsnap.com