Heat exchange structure and preparation method thereof
A technology of heat exchange structure and rib plate, applied in the direction of electrical components, electric solid devices, circuits, etc., can solve the problems of difficult to solve thermal control of high power density electronic products, large temperature difference between heat source and internal steam, immersion, etc., and achieves the preparation method. Simple and efficient, shortened motion path, reliable principle effect
- Summary
- Abstract
- Description
- Claims
- Application Information
AI Technical Summary
Problems solved by technology
Method used
Image
Examples
Embodiment 1
[0032] Such as figure 1 As shown, a rib-composite internal groove enhanced boiling heat transfer structure includes a metal base plate 1, a rib array group 2 arranged in parallel on the metal base plate, and a number of vertical inner grooves 3 evenly arranged on the side of the rib plate . The thickness of the ribs in the rib array group is 1.2mm, the height of the ribs is 5mm, and the spacing between the ribs is 0.8mm. The rib plate is a metal solid structure, and the material of the base plate and the rib plate is aluminum metal. The cross-sectional shape of the inner groove is "Ω" shape, the equivalent diameter is 0.35mm, and the center-to-center distance between two adjacent inner grooves is 1mm.
[0033] The preparation method of the above-mentioned rib-plate composite inner groove enhanced boiling heat transfer structure includes the following steps:
[0034] S1. Select a metal base plate with a thickness of 7 mm, and process a rib array group arranged in parallel on...
Embodiment 2
[0038] Such as figure 2 As shown, a rib-plate composite inner-groove channel enhanced boiling heat transfer structure includes a metal base plate, rib plate arrays arranged in parallel on the metal base plate, and several vertical inner grooves evenly arranged on the side of the rib plate. The thickness of the ribs in the rib array group is 1mm, the height of the ribs is 4mm, and the spacing between the ribs is 1mm. The base plate and ribs are made of red copper, the ribs are sintered metal powder, and the metal powder 5 is spherical. The cross-sectional shape of the inner groove is "Ω" shape, the equivalent diameter is 0.3mm, and the center-to-center distance between two adjacent inner grooves is 0.8mm.
[0039] The preparation method of the above-mentioned rib-plate composite inner groove enhanced boiling heat transfer structure includes the following steps:
[0040] S1. Choose a metal substrate with a thickness of 2mm and metal powder with an equivalent diameter between ...
PUM
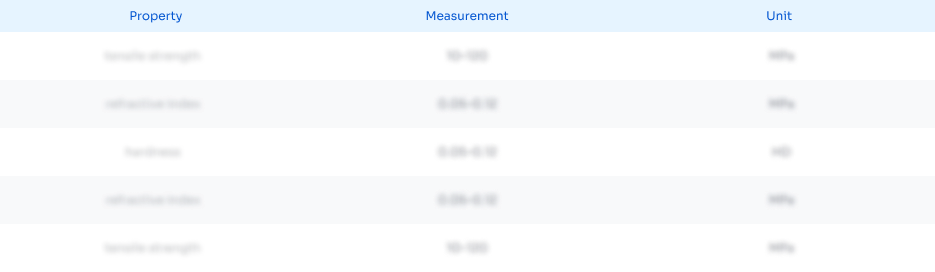
Abstract
Description
Claims
Application Information

- R&D Engineer
- R&D Manager
- IP Professional
- Industry Leading Data Capabilities
- Powerful AI technology
- Patent DNA Extraction
Browse by: Latest US Patents, China's latest patents, Technical Efficacy Thesaurus, Application Domain, Technology Topic, Popular Technical Reports.
© 2024 PatSnap. All rights reserved.Legal|Privacy policy|Modern Slavery Act Transparency Statement|Sitemap|About US| Contact US: help@patsnap.com