Controlled cooling and controlled rolling method for control over bearing steel wire network carbide
A technology of controlled cooling and controlled rolling and carbide, applied in the field of steel manufacturing, can solve the problems of high temperature difference, increase the cost of steelmaking, increase the difficulty of steelmaking, etc., and achieve the effects of uniform temperature, fast cooling speed and short cooling time.
- Summary
- Abstract
- Description
- Claims
- Application Information
AI Technical Summary
Problems solved by technology
Method used
Image
Examples
Embodiment 1
[0032] The production specification is Φ18mm high-carbon chromium bearing steel wire rod. The wire rod is rolled into the specified specification by high-speed wire rod and then spun into loose coils. The carbide network control is carried out according to the following process parameters: the temperature of the entering and reducing sizing machine (ie, the final rolling temperature) is 830°C-870°C, and the spinning temperature of the wire rod is 810°C-850°C; the wire rod passes through the water bath online after spinning Controlled cooling by isothermal quenching, the temperature of the water bath is 90°C-97°C, and the cooling time of the water bath is 20s-80s; the temperature of the outlet water after the wire rod is cooled by the EDC water bath is 620°C-630°C. After the wire rod comes out of the water, add a cover to cool slowly. The holding time is 30min-60min, and slowly cool to 430°C-470°C. After taking out the cover, the collection rolls were air-cooled to room tempera...
Embodiment 2
[0036] The production specification is Φ13.5mm high-carbon chromium bearing steel wire rod, and the wire rod is rolled into the specified specification by high-speed wire rod before spinning. The carbide network control is carried out according to the following process parameters: the temperature of the entering and reducing sizing machine is 800°C-850°C, and the spinning temperature of the wire rod is 800°C-840°C; The temperature is 90°C-97°C, and the cooling time in the water bath is 20s-60s; the temperature of the outlet water after the wire rod is cooled by the EDC water bath is 620°C-630°C. After the wire rod comes out of the water, add a cover to cool slowly. The holding time is 40min-60min, and slowly cool to 420°C-450°C. After taking out the cover, the collection rolls were air-cooled to room temperature.
[0037] The chemical composition of the product: C 0.98%, Si 0.29%, Mn 0.31%, Cr 1.45%, Mo 0.01%, Ni0.02%, Al 0.025%, P 0.012%, S 0.001%, Cu 0.09%, Ca 0.0001%, O 0...
PUM
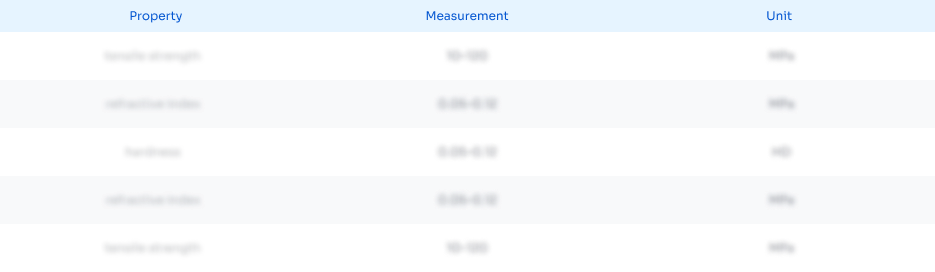
Abstract
Description
Claims
Application Information

- R&D
- Intellectual Property
- Life Sciences
- Materials
- Tech Scout
- Unparalleled Data Quality
- Higher Quality Content
- 60% Fewer Hallucinations
Browse by: Latest US Patents, China's latest patents, Technical Efficacy Thesaurus, Application Domain, Technology Topic, Popular Technical Reports.
© 2025 PatSnap. All rights reserved.Legal|Privacy policy|Modern Slavery Act Transparency Statement|Sitemap|About US| Contact US: help@patsnap.com