Phenolic resin binder with less resin content
A technology of phenolic resin and resin content, which is applied in the direction of casting molding equipment, molds, cores, etc., can solve the problems of low strength, increased dosage, and increased core cost, and achieve strong bonding strength, high compressive strength, The effect of reduced dosage
- Summary
- Abstract
- Description
- Claims
- Application Information
AI Technical Summary
Problems solved by technology
Method used
Image
Examples
preparation example Construction
[0020] The preparation method of the modifier is to heat the xylene solution with a mass concentration of 28-36% to 125-135°C in an argon atmosphere, and then add 2.6-3.2% polyacrylic acid equivalent to the weight of the xylene solution Butyl ester, 1.2-1.8% α-cyanoacrylate, 2.2-2.8% vinyl tertiary carbonate, stirred for 40-60 minutes, then cooled to 95-105°C, then added 1.5-2 % isooctyl acrylate, 0.8-1.2% dodecyl mercaptan, 0.2-0.7% furfural, stir for 10-12 hours, cool to room temperature after completion, add ethanol and let stand for 4-6 hours, filter after completion, Obtained by washing and drying;
[0021] The preparation method includes the following contents: mixing thermosetting resole phenolic resin, thermosetting b-stage phenolic resin, alkali aqueous solution with a mass concentration of 50%, and a modifier, stirring and mixing for 30-40 minutes at a temperature of 85-95°C , lower the temperature to 45°C, add potassium pyrophosphate, boric acid, alkaline regulator...
Embodiment 1
[0033] A phenolic resin binder with reduced resin content, comprising the following raw materials in parts by weight: 40 parts of thermosetting resole phenolic resin, 24 parts of thermosetting B-stage phenolic resin, 80 parts of alkali aqueous solution with a mass concentration of 50%, and 8 parts of modifier 2 parts of potassium pyrophosphate, 5 parts of boric acid, 4 parts of alkaline regulator, 8 parts of ammonium sulfate, 3.2 parts of lauryl glucoside, 3.5 parts of polycarbonate diol, 2.2 parts of organometallic carboxylic acid compound, wood 1.6 parts of sodium sulfonate, 5 parts of silane coupling agent;
[0034]The preparation method of the modifier is as follows: in an argon atmosphere, heat a xylene solution with a mass concentration of 32% to 130°C, and then add 2.9% polybutylacrylate, 1.5% α -Cyanoacrylate, 2.5% vinyl tertiary carbonate, stirred for 50 minutes, then cooled to 100°C, then added 1.8% isooctyl acrylate, 1% dodecyl mercaptan, 0.5 % furfural, stirred an...
Embodiment 2
[0038] A phenolic resin binder with reduced resin content, comprising the following raw materials in parts by weight: 35 parts of thermosetting resole phenolic resin, 20 parts of thermosetting B-stage phenolic resin, 75 parts of alkali aqueous solution with a mass concentration of 50%, and 10 parts of modifier 3 parts, potassium pyrophosphate 3 parts, boric acid 4 parts, alkaline regulator 5 parts, ammonium sulfate 10 parts, lauryl glucoside 3.6 parts, polycarbonate diol 3.3 parts, organometallic carboxylic acid compound 2.6 parts, wood 1.4 parts of sodium sulfonate, 6 parts of silane coupling agent;
[0039] The preparation method of the modifier is as follows: in an argon atmosphere, heat a xylene solution with a mass concentration of 28% to 125°C, and then add 3.2% polybutylacrylate, 1.2% α -Cyanoacrylate, 2.8% vinyl tertiary carbonate, stirred for 60 minutes, then cooled to 105°C, then added 2% isooctyl acrylate, 1.2% dodecyl mercaptan, 0.2 % furfural, stirred and reacted...
PUM
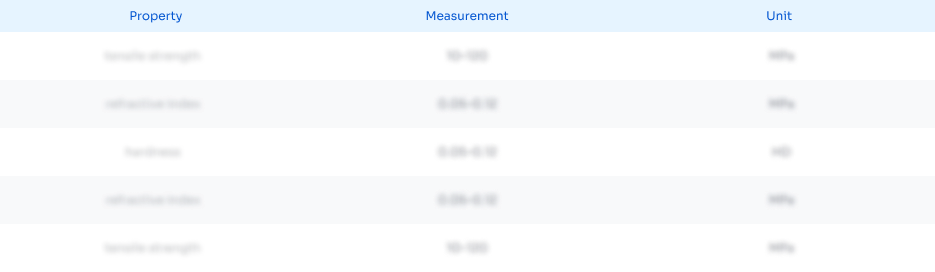
Abstract
Description
Claims
Application Information

- R&D Engineer
- R&D Manager
- IP Professional
- Industry Leading Data Capabilities
- Powerful AI technology
- Patent DNA Extraction
Browse by: Latest US Patents, China's latest patents, Technical Efficacy Thesaurus, Application Domain, Technology Topic, Popular Technical Reports.
© 2024 PatSnap. All rights reserved.Legal|Privacy policy|Modern Slavery Act Transparency Statement|Sitemap|About US| Contact US: help@patsnap.com