Castable and forgeable solid solution tungsten alloy and preparation method
A solid solution and tungsten alloy technology, applied in the field of refractory alloys, can solve problems such as low density, inability to guarantee toughness, and easy forging cracks, etc., and achieve excellent comprehensive performance, excellent thermal processing performance, and good thermal processing performance.
- Summary
- Abstract
- Description
- Claims
- Application Information
AI Technical Summary
Problems solved by technology
Method used
Image
Examples
Embodiment Construction
[0046] According to the chemical composition scope of castable wrought solid solution tungsten alloy of the present invention, adopt 25 kilograms of vacuum induction furnaces to prepare 20 kilograms of alloy ingots 31 furnaces, its specific chemical composition sees table 1.
[0047] The melting temperature of the alloy is above 1500°C. After the test steel is smelted and cast into steel ingots, the billet is opened at 1180°C, the forging heating temperature is 1150°C, and the final forging temperature is 1000°C.
[0048] The size of the forging test rod is: φ15×2000mm, 15×15×2000mm.
[0049] After forging, the test bar is first stretched and impacted on the sample blank. Finally, aging treatment: aging treatment at 550-850°C, holding time for 10 hours, air cooling. The mechanical properties tested after grinding of the sample blank are shown in Table 2.
[0050] For comparison, the chemical composition and mechanical properties of Comparative Example 93W-7 (Ni, Fe) etc. are...
PUM
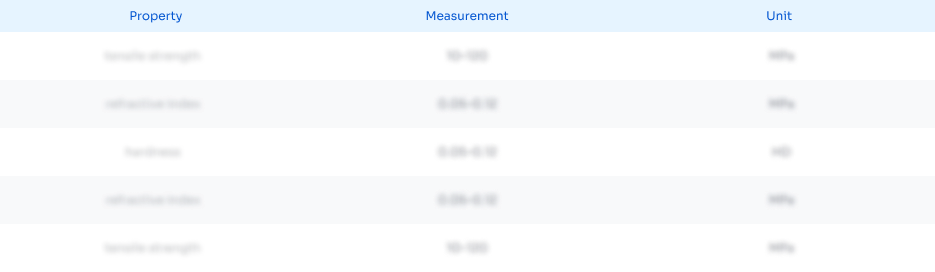
Abstract
Description
Claims
Application Information

- R&D
- Intellectual Property
- Life Sciences
- Materials
- Tech Scout
- Unparalleled Data Quality
- Higher Quality Content
- 60% Fewer Hallucinations
Browse by: Latest US Patents, China's latest patents, Technical Efficacy Thesaurus, Application Domain, Technology Topic, Popular Technical Reports.
© 2025 PatSnap. All rights reserved.Legal|Privacy policy|Modern Slavery Act Transparency Statement|Sitemap|About US| Contact US: help@patsnap.com