Manufacturing method of vehicle brake disc
A manufacturing method and technology for brake discs, which are applied in the directions of brake discs, brake components, and manufacturing tools, can solve problems such as large brake disc mass, reduce unsprung mass, improve operational stability, and reduce overall quality. Effect
- Summary
- Abstract
- Description
- Claims
- Application Information
AI Technical Summary
Problems solved by technology
Method used
Image
Examples
Embodiment Construction
[0035] It should be noted that, in the case of no conflict, the embodiments and features in the embodiments of the present invention can be combined with each other.
[0036] The present invention will be described in detail below with reference to the drawings and in combination with embodiments.
[0037] The present invention provides a method for manufacturing a brake disc of a vehicle, wherein the brake disc includes a main body disc 1 and two friction rings 2, and the friction rings 2 are annular plates attached to the main body disc 1 on both sides of the disk, the manufacturing method includes the following steps:
[0038] S1. Casting two friction rings 2 using cast iron materials;
[0039] S2. Prepare a casting mold and a core mold for the brake disc, the casting mold has a cavity corresponding to the brake disc, fix the core mold and the two friction rings 2 on the Corresponding position in the cavity;
[0040] S3. Casting molten aluminum alloy into the cavity, the...
PUM
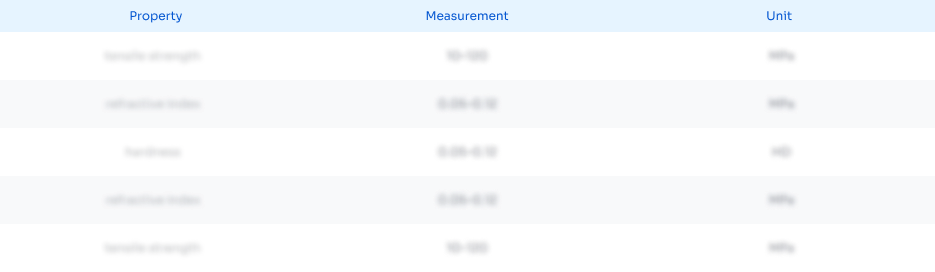
Abstract
Description
Claims
Application Information

- R&D Engineer
- R&D Manager
- IP Professional
- Industry Leading Data Capabilities
- Powerful AI technology
- Patent DNA Extraction
Browse by: Latest US Patents, China's latest patents, Technical Efficacy Thesaurus, Application Domain, Technology Topic, Popular Technical Reports.
© 2024 PatSnap. All rights reserved.Legal|Privacy policy|Modern Slavery Act Transparency Statement|Sitemap|About US| Contact US: help@patsnap.com