Production method for preventing straightening and hot delivering cracks of microalloy continuous casting slab
A production method and technology of micro-alloyed steel, applied in the field of steelmaking, to achieve the effects of avoiding straightening crack defects, improving surface structure, and improving high-temperature plasticity
- Summary
- Abstract
- Description
- Claims
- Application Information
AI Technical Summary
Problems solved by technology
Method used
Image
Examples
Embodiment 1
[0022] When producing aluminum-killed steel blooms with a cross-section of 300mm×390mm and the brand SCM435 (mass percentage of chemical composition: C: 0.35%, Al: 0.033%), the ordinary continuous casting cooling process is adopted to hot charge and heat the billet, and the billet is put into the furnace When the surface temperature was 738°C, after the bloom was opened into a billet, the occurrence rate of surface cracks was as high as 10.6%, such as figure 1 and image 3 shown. When the present invention is adopted, the surface temperature of the billet before rapid cooling is 920°C, the four-sided spray mode of full water spray is adopted, the cooling water volume is 280L / min, the spray pressure reaches 8.2MPa, the surface cooling rate is 5.8°C / s, and the rapid cooling Finally, the surface temperature of the billet is 420°C. After tempering, the surface temperature of the billet at the straightening position is 568°C. The highest surface temperature after tempering is 650°...
Embodiment 2
[0024] When producing aluminum-killed steel billets with a cross-section of 140mm×140mm and a grade of 10B21 (mass percentage of chemical composition: C: 0.22%, Al: 0.030%), the ordinary continuous casting cooling process is adopted to hot charge and heat the billets for straightening The corner temperature of the billet was 848°C. After the billet surface was pickled, many transverse crack defects were found at the corners, and the crack incidence rate reached 33.3%. After the billet was rolled, the wire rod returned to scrap aluminum as high as 3.8%. When the present invention is adopted, the full water spray mode is adopted, the cooling water volume is 260L / min, the spray pressure reaches 7.5MPa, and the surface cooling rate is 6.5°C / s. After rapid cooling, the billet surface temperature is 415°C. , The surface temperature of the billet at the straightening position is 566°C, no transverse crack defects at the corners were found in the pickling of the billet sample surface, ...
Embodiment 3
[0026] When producing 220mm×1260mm grade X70 (chemical composition mass percentage C: 0.06%, Nb: 0.07%) continuous casting slabs of pipeline steel containing Nb, the ordinary continuous casting cooling process is adopted, and the surface temperature of the slab at the straightening position is 906 ℃, the continuous casting slab blank inspection found that there are many surface transverse cracks at the corners, and the crack occurrence rate is as high as 15.2%. When the present invention is adopted, the steam-water four-sided spray mode is adopted, the cooling water volume is 350L / min, the spray pressure reaches 8.0MPa, and the surface cooling rate is 6.2°C / s. After rapid cooling, the billet surface temperature is 440°C. , The surface temperature of the blank at the straightening position is 587°C. After checking the continuous casting slab blank, no transverse crack defect at the corner was found.
PUM
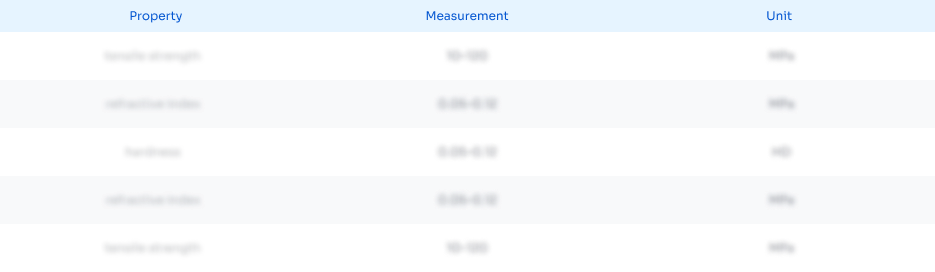
Abstract
Description
Claims
Application Information

- Generate Ideas
- Intellectual Property
- Life Sciences
- Materials
- Tech Scout
- Unparalleled Data Quality
- Higher Quality Content
- 60% Fewer Hallucinations
Browse by: Latest US Patents, China's latest patents, Technical Efficacy Thesaurus, Application Domain, Technology Topic, Popular Technical Reports.
© 2025 PatSnap. All rights reserved.Legal|Privacy policy|Modern Slavery Act Transparency Statement|Sitemap|About US| Contact US: help@patsnap.com