H13 round steel continuous casting and continuous rolling manufacturing process
A manufacturing process, continuous casting and rolling technology, applied in the direction of manufacturing tools, metal rolling, metal rolling, etc., can solve the problems of internal looseness and difficult welding, surface rolling defects, affecting the quality of rolling materials and final products, etc. Achieve the effect of improving the qualified rate of ultrasonic flaw detection
- Summary
- Abstract
- Description
- Claims
- Application Information
AI Technical Summary
Problems solved by technology
Method used
Examples
Embodiment 1
[0018] This embodiment is a H13 round steel continuous casting and rolling manufacturing process, including:
[0019] ⑴Continuous casting: It is produced by an arc-shaped billet continuous casting machine with a section of 320mm×400mm or more, using ultra-weak cold cooling, with a specific water volume of 0.21L / Kg, the electromagnetic stirring parameter of the mold: 570A*2Hz, the light reduction mode is the former The three pressing rollers respectively press down 2mm-2mm-2mm, the last four pressing rollers have a reduction of 0mm, the pulling speed: 0.51m / min, and the superheat is 10℃;
[0020] ⑵After continuous casting, hot charging and sending to the heating furnace: the casting billet is sent to the heating furnace by a fully enclosed holding car, and the heating temperature is controlled at 300℃;
[0021] ⑶ High-temperature diffusion heating: high-temperature diffusion heating is carried out in a stepped heating furnace, the temperature of the non-heating section is 300℃, the te...
Embodiment 2
[0026] This embodiment is a H13 round steel continuous casting and rolling manufacturing process, including:
[0027] ⑴Continuous casting: It is produced by an arc-shaped billet continuous casting machine with a cross-section of 320mm×400mm or more, using ultra-weak cold cooling, specific water volume of 0.25L / Kg, mold electromagnetic stirring parameter: 570A*2Hz, light reduction mode is the former The three pressing rollers respectively press down 2mm-2mm-2mm, and the last four pressing rollers have a reduction of 0mm, the pulling speed: 0.6m / min, and the degree of overheating is 35℃;
[0028] ⑵After continuous casting, hot charging and sending to the heating furnace: the casting billet is sent to the heating furnace by a fully enclosed holding car, and the heating temperature is controlled at 700℃;
[0029] ⑶ High-temperature diffusion heating: high-temperature diffusion heating in a step-by-step heating furnace, the temperature of the non-heating section is 800℃, the temperature o...
Embodiment 3
[0034] This embodiment is a H13 round steel continuous casting and rolling manufacturing process, including:
[0035] ⑴Continuous casting: It is produced by an arc-shaped billet continuous casting machine with a cross-section of 320mm×400mm and above, using ultra-weak cold cooling, specific water volume is 0.23L / Kg, mold electromagnetic stirring parameters: 570A*2Hz, light reduction mode is the front The three pressing rolls respectively press down 2mm-2mm-2mm, the last four pressing rolls have a reduction of 0mm, the pulling speed: 0.55m / min, and the degree of overheating is 25℃;
[0036] ⑵After continuous casting, hot charging and sending to the heating furnace: the casting billet is sent to the heating furnace by a fully enclosed holding car, and the heating temperature is controlled at 500℃;
[0037] ⑶ High-temperature diffusion heating: high-temperature diffusion heating is carried out in a stepped heating furnace, the temperature of the non-heating section is 600℃, the temperat...
PUM
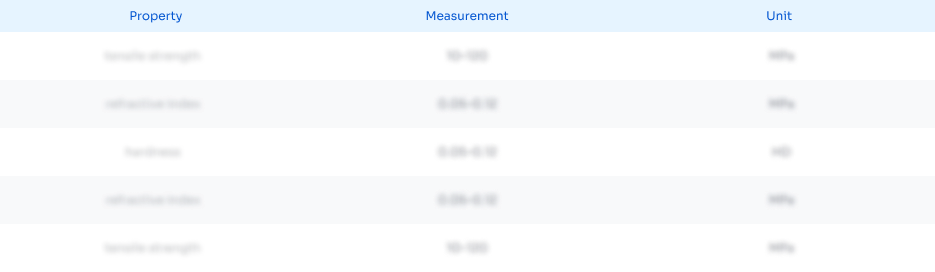
Abstract
Description
Claims
Application Information

- Generate Ideas
- Intellectual Property
- Life Sciences
- Materials
- Tech Scout
- Unparalleled Data Quality
- Higher Quality Content
- 60% Fewer Hallucinations
Browse by: Latest US Patents, China's latest patents, Technical Efficacy Thesaurus, Application Domain, Technology Topic, Popular Technical Reports.
© 2025 PatSnap. All rights reserved.Legal|Privacy policy|Modern Slavery Act Transparency Statement|Sitemap|About US| Contact US: help@patsnap.com