Method for producing ferric phosphate by dephosphorized converter slag
An iron phosphate and slag technology, applied in chemical instruments and methods, phosphorus compounds, inorganic chemistry, etc., can solve the problems of insoluble, incomplete, undisclosed alloys, and P, Fe oxide impurity content, etc., to reduce the harmfulness , the effect of high added value
- Summary
- Abstract
- Description
- Claims
- Application Information
AI Technical Summary
Problems solved by technology
Method used
Image
Examples
Embodiment 1
[0009] Embodiment 1: containing P 2 o 5 Dephosphorization slag treatment process with a mass fraction of 5.2%
[0010] The specific composition of dephosphorization slag is as follows:
[0011] Element
[0012] Treat 10 tons of dephosphorized slag with the above components in an electric arc furnace, and add 1200kg of silica (containing SiO 2 =95%, CaO=5%), the slag obtained at this time has a basicity of 1.20, and then adds coal powder (containing 80% of fixed carbon, 10% of volatile matter, and 10% of ash) to it, and the excess coefficient is 1.2. The added amount is 1350kg, and the melting reduction is carried out under the condition of 1350°C.
[0013] The composition of the obtained slag is similar to that of blast furnace slag, and it can be used as cement raw material after water quenching. The specific composition is as follows:
[0014] Element
[0015] Obtain a total of 2435.0kg containing P=3.28% high-phosphorus molten iron, and the compositi...
Embodiment 2
[0020] Embodiment 2: containing P 2 o 5 Dephosphorization slag treatment process with mass fraction of 7.5%
[0021] The specific composition of dephosphorization slag is as follows:
[0022] Element
[0023] Treat 10 tons of dephosphorized slag of the above composition in an electric arc furnace, and add 1400kg of iron tailings (containing SiO 2 = 60%, Fe 2 o 3 =30%, Al 2 o 3 =10%), the slag system alkalinity obtained at this moment is 1.20, and then is mixed into coal powder (containing fixed carbon 80%, volatile matter 10%, ash content 10%) wherein, excess coefficient gets 1.2, and add-on is 1400kg, Smelting reduction is carried out at 1350°C.
[0024] The composition of the obtained slag is similar to that of blast furnace slag, and it can be used as cement raw material after water quenching. The specific composition is as follows:
[0025] Element
[0026] Obtain simultaneously the total 2288.6kg of high-phosphorus molten iron that contains P=4...
PUM
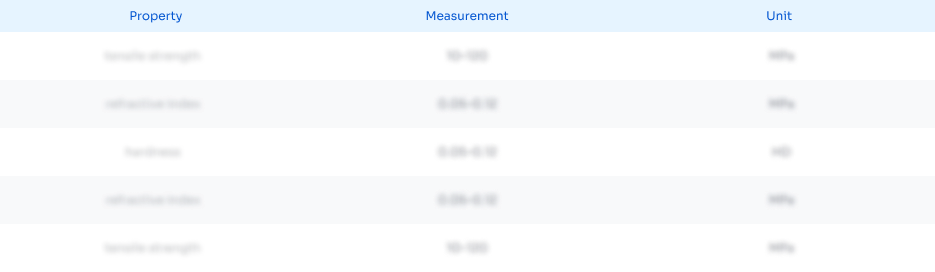
Abstract
Description
Claims
Application Information

- R&D Engineer
- R&D Manager
- IP Professional
- Industry Leading Data Capabilities
- Powerful AI technology
- Patent DNA Extraction
Browse by: Latest US Patents, China's latest patents, Technical Efficacy Thesaurus, Application Domain, Technology Topic, Popular Technical Reports.
© 2024 PatSnap. All rights reserved.Legal|Privacy policy|Modern Slavery Act Transparency Statement|Sitemap|About US| Contact US: help@patsnap.com