Biomass boiler system with self biomass upgrading function
A biomass boiler and biomass technology, applied in the direction of biofuel, coke oven, waste fuel, etc., can solve the problems of wasting resources, incomplete combustion, and high energy consumption in production, so as to reduce energy consumption and pollution, and improve combustion efficiency , Improve the effect of fuel quality
- Summary
- Abstract
- Description
- Claims
- Application Information
AI Technical Summary
Problems solved by technology
Method used
Image
Examples
Embodiment Construction
[0030] The present invention will be further described in detail below in conjunction with specific embodiments, which are explanations of the present invention rather than limitations.
[0031] Such as figure 1 As shown, the present invention has a biomass boiler system with biomass quality improvement function, comprising a raw material bin 1, a crusher 2 connected to the raw material bin 1, a granulator 3 connected to the crusher 2, and an upper part connected to the granulator The first carbonization furnace 4 and the second carbonization furnace 5 connected by machine 3. The carbonization furnace here has at least one stage, and can also be cascaded in parallel with multiple stages. This embodiment takes two stages as an example for illustration. The combustible flue gas discharged from the upper part of the first carbonization furnace 4 and the second carbonization furnace 5 passes into the boiler 6 for combustion through the tuyeres on the upper part of the throat, and...
PUM
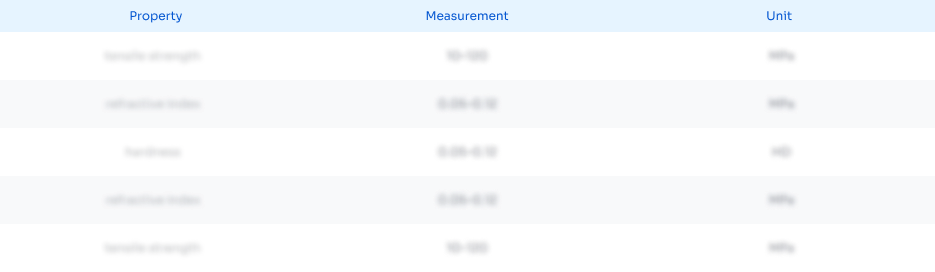
Abstract
Description
Claims
Application Information

- R&D
- Intellectual Property
- Life Sciences
- Materials
- Tech Scout
- Unparalleled Data Quality
- Higher Quality Content
- 60% Fewer Hallucinations
Browse by: Latest US Patents, China's latest patents, Technical Efficacy Thesaurus, Application Domain, Technology Topic, Popular Technical Reports.
© 2025 PatSnap. All rights reserved.Legal|Privacy policy|Modern Slavery Act Transparency Statement|Sitemap|About US| Contact US: help@patsnap.com