Preparation method of powder metallurgy friction material
A friction material and powder metallurgy technology, which is applied in the field of powder metallurgy friction material preparation, can solve the problems such as the instable friction coefficient of powder metallurgy friction materials, and achieves the advantages of light weight, high tensile strength, good high temperature resistance and friction resistance. Effect
- Summary
- Abstract
- Description
- Claims
- Application Information
AI Technical Summary
Problems solved by technology
Method used
Examples
example 1
[0024] Take 80g of copper powder, 20g of iron powder, 4g of chromium powder, 5g of ferrochrome powder, 15g of graphite, 2g of silicon dioxide and 20g of engine oil and fully mix them in a mixing equipment to obtain a mixture; cold press the mixture under a pressure of 400MPa , to obtain a block, repeat the preparation to obtain three green blocks; take 10g of glass fiber interweaving and laying up as a glass fiber mesh, 15g of ceramic fiber interweaving and laying up as a ceramic fiber mesh, and 5g of boron fiber interweaving and laying up as a boron fiber mesh; take the first Block the embryo block, and lay the glass fiber mesh, ceramic fiber mesh, and boron fiber mesh on the embryo block in sequence, then place the second embryo block on the mesh surface, and then place the glass fiber mesh, ceramic fiber mesh, boron fiber Lay the net on the green block in turn, cover the third green block to obtain the green block layer; stack the green block layer with the steel core layer ...
example 2
[0026] Take 120g of copper powder, 30g of iron powder, 6g of chromium powder, 8g of ferrochrome powder, 25g of graphite, 3g of silicon dioxide and 30g of engine oil and fully mix them in a mixing equipment to obtain a mixture; cold press the mixture under a pressure of 500MPa , to obtain a block, and repeat the preparation to obtain three green blocks; take 15g glass fiber interweaving and laying up to be glass fiber mesh, 25g ceramic fiber interweaving and laying up to be ceramic fiber mesh, 8g boron fiber interweaving and laying up to be boron fiber mesh; take the first Block the embryo block, and lay the glass fiber mesh, ceramic fiber mesh, and boron fiber mesh on the embryo block in sequence, then place the second embryo block on the mesh surface, and then place the glass fiber mesh, ceramic fiber mesh, boron fiber Lay the net on the green block in turn, cover the third green block to obtain the green block layer; stack the green block layer with the steel core layer or th...
example 3
[0028] Take 160g of copper powder, 40g of iron powder, 8g of chromium powder, 10g of ferrochrome powder, 30g of graphite, 4g of silicon dioxide and 40g of engine oil and fully mix them in a mixing equipment to obtain a mixture; cold press the mixture under a pressure of 600MPa , to obtain a block, repeat the preparation to obtain three green blocks; take 20g of glass fiber interweaving and laying up to be a glass fiber net, 30g of ceramic fiber interweaving and laying up to be a ceramic fiber net, and 10g of boron fiber to be interwoven and laying up to be a boron fiber net; take the first Block the embryo block, and lay the glass fiber mesh, ceramic fiber mesh, and boron fiber mesh on the embryo block in sequence, then place the second embryo block on the mesh surface, and then place the glass fiber mesh, ceramic fiber mesh, boron fiber Lay the net on the green block in turn, cover the third green block to obtain the green block layer; stack the green block layer and the steel...
PUM
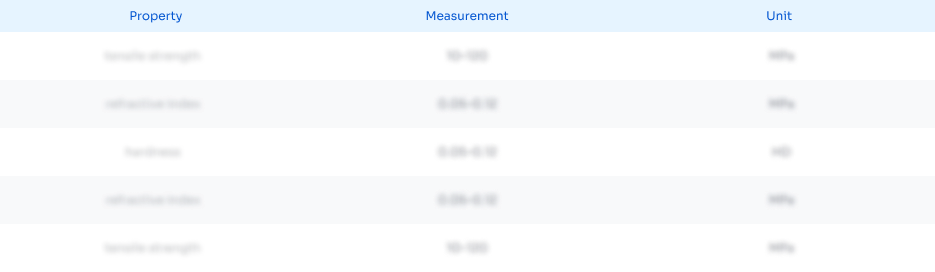
Abstract
Description
Claims
Application Information

- Generate Ideas
- Intellectual Property
- Life Sciences
- Materials
- Tech Scout
- Unparalleled Data Quality
- Higher Quality Content
- 60% Fewer Hallucinations
Browse by: Latest US Patents, China's latest patents, Technical Efficacy Thesaurus, Application Domain, Technology Topic, Popular Technical Reports.
© 2025 PatSnap. All rights reserved.Legal|Privacy policy|Modern Slavery Act Transparency Statement|Sitemap|About US| Contact US: help@patsnap.com