A method of using high-iron sphalerite to strengthen bornite leaching
A technology for sphalerite and bornite, which is applied in the direction of improving process efficiency, can solve the problems of long leaching period, slow growth of microorganisms, slow leaching rate, etc., so as to shorten the leaching period, reduce the technological process and shorten the lag period. Effect
- Summary
- Abstract
- Description
- Claims
- Application Information
AI Technical Summary
Problems solved by technology
Method used
Examples
Embodiment 1
[0028] The high-iron sphalerite and bornite are respectively ground to -0.074mm, and the ore powder content of this particle size is more than 85%. The high-iron sphalerite powder and bornite powder are intermittently sterilized, the sterilized high-iron sphalerite powder and bornite powder are mixed, and the mixing ratio is 3:1, and then the sterilized powder is added. The 9K basal medium of the bacteria is obtained by ore pulp, and by regulating the chemical conditions of the leaching solution, 0.1-0.5mol / L H is used. 2 SO 4 Adjust the pH of the pulp to 1.5-2.0, and then the mixed pulp is leached by stirring. The leaching temperature is 30°C, the stirring speed is 100-300rpm, the leaching potential is 180-610mV, and the leaching is carried out for 15 days, and the leaching of copper is measured and calculated. Compared with leaching bornite alone in the prior art, the leaching rate is increased by 3.9%.
Embodiment 2
[0030] The high-iron sphalerite and bornite are respectively ground to -0.074mm, and the ore powder content of this particle size is more than 85%. The high-iron sphalerite powder and bornite powder are intermittently sterilized, the sterilized high-iron sphalerite powder and bornite powder are mixed, and the mixing ratio is 1:1, and then the sterilized powder is added. The 9K basal medium of the bacteria is obtained by ore pulp, and by regulating the chemical conditions of the leaching solution, 0.1-0.5mol / L H is used. 2 SO 4 Adjust the pH of the pulp to 1.5-2.0, and then the mixed pulp is leached by stirring. The leaching temperature is 30°C, the stirring speed is 100-300rpm, the leaching potential is 180-610mV, and the leaching is performed for 15 days. The leaching of copper is measured and calculated. Compared with leaching bornite alone in the prior art, the leaching rate is increased by 2.5%.
Embodiment 3
[0032] The high-iron sphalerite and bornite are respectively ground to -0.074mm, and the content of ore powder of this particle size is over 85%. The high-iron sphalerite powder and bornite powder are intermittently sterilized, the sterilized high-iron sphalerite powder and bornite powder are mixed, and the mixing ratio is 1:3, and then the sterilized powder is added. The 9K basal medium of the bacteria is obtained by ore pulp, and by regulating the chemical conditions of the leaching solution, 0.1-0.5mol / L H is used. 2 SO 4 Adjust the pH of the pulp to 1.5-2.0, and then the mixed pulp is leached by stirring. The leaching temperature is 30°C, the stirring speed is 100-300rpm, the leaching potential is 180-610mV, and the leaching is carried out for 15 days, and the leaching of copper is measured and calculated. Compared with leaching bornite alone in the prior art, the leaching rate is increased by 1.8%.
PUM
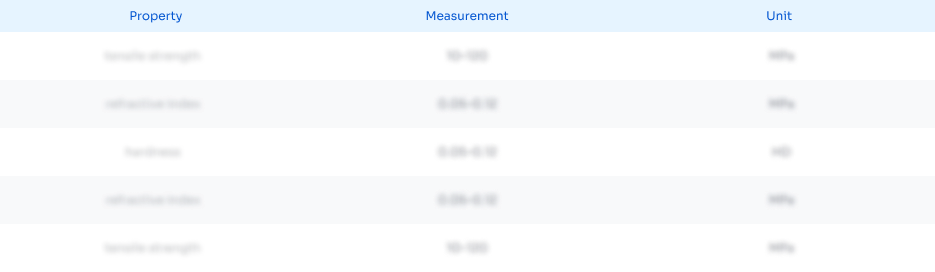
Abstract
Description
Claims
Application Information

- R&D
- Intellectual Property
- Life Sciences
- Materials
- Tech Scout
- Unparalleled Data Quality
- Higher Quality Content
- 60% Fewer Hallucinations
Browse by: Latest US Patents, China's latest patents, Technical Efficacy Thesaurus, Application Domain, Technology Topic, Popular Technical Reports.
© 2025 PatSnap. All rights reserved.Legal|Privacy policy|Modern Slavery Act Transparency Statement|Sitemap|About US| Contact US: help@patsnap.com