A welding method for thin steel plate fillet joints
A fillet joint and welding method technology, which is applied in the welding field of thin steel plate fillet joints, can solve the problems of complex adjustment of double laser beam welding process, difficulty in mass production, and large heat input, etc., to achieve non-deformation connection, Beautiful shape and good consistency
- Summary
- Abstract
- Description
- Claims
- Application Information
AI Technical Summary
Problems solved by technology
Method used
Image
Examples
Embodiment Construction
[0039] The technical solution of the present invention will be described in detail below in conjunction with the accompanying drawings and specific embodiments.
[0040] Such as Figure 1-3 As shown, the invention provides a welding method of thin steel fillet joints, comprising the steps of:
[0041] Step 1: Accurately corner-join and clamp the first workpiece 2 and the second workpiece 3 .
[0042] Optionally, the thickness of the first workpiece 2 and the second workpiece 3 are both 0.5-2.5 mm.
[0043] Optionally, the first workpiece 2 and the second workpiece 3 may be ordinary carbon steel plates, coated carbon steel plates and stainless steel plates.
[0044] Step 2: Provide a third workpiece 5 of the same material as the first workpiece 2 and the second workpiece 3, the third workpiece 5 is located directly above the corner joint.
[0045] Optionally, the thickness of the third workpiece 5 is 1.0-5.0 mm.
[0046] Optionally, the third workpiece 5 is made of the same...
PUM
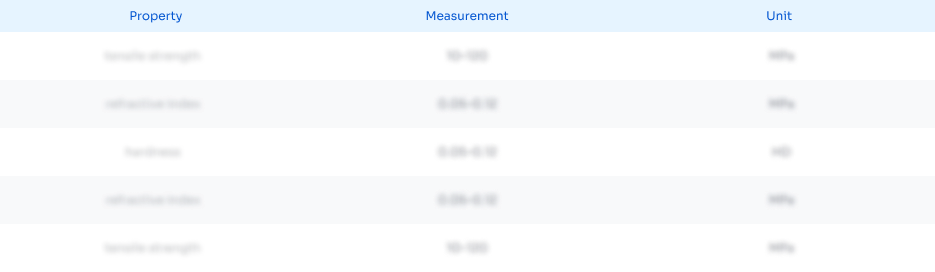
Abstract
Description
Claims
Application Information

- R&D Engineer
- R&D Manager
- IP Professional
- Industry Leading Data Capabilities
- Powerful AI technology
- Patent DNA Extraction
Browse by: Latest US Patents, China's latest patents, Technical Efficacy Thesaurus, Application Domain, Technology Topic, Popular Technical Reports.
© 2024 PatSnap. All rights reserved.Legal|Privacy policy|Modern Slavery Act Transparency Statement|Sitemap|About US| Contact US: help@patsnap.com