Insulating heat-conducting cable material and preparation method thereof
A technology of insulation and heat conduction, cable material, applied in the field of cable material, can solve the problems of the overall performance level decline and poor compatibility of the cable material, and achieve the effect of excellent overall performance, good aging resistance and high thermal conductivity
- Summary
- Abstract
- Description
- Claims
- Application Information
AI Technical Summary
Problems solved by technology
Method used
Examples
Embodiment 1
[0027] This embodiment relates to an insulating and heat-conducting cable material, including the following raw materials in parts by weight: 20 parts of polyvinyl chloride resin, 15 parts of ethylene-vinyl acetate copolymer, and 18 parts of styrene-ethylene-butylene-styrene block copolymer , 3 parts of graphene oxide, 6 parts of butyl rubber, 3 parts of trioctyl trimellitate, 3 parts of modified talcum powder, 2 parts of flame retardant, 1 part of lubricant, and 2 parts of antioxidant.
[0028] Wherein, the preparation method of described modified talcum powder is as follows:
[0029] Soak the talc powder in the mixed solution of sodium carbonate and potassium permanganate for 3 hours, take it out and dry it, add silane coupling agent KH550 equivalent to 3% of the weight of the talc powder, and sodium lauryl sulfate equivalent to 2% of the weight of the talc powder Stir with alumina equivalent to 2% of the weight of talcum powder at 1000r / min for 20 minutes, then grind, and p...
Embodiment 2
[0041] This embodiment relates to an insulating and heat-conducting cable material, including the following raw materials in parts by weight: 30 parts of polyvinyl chloride resin, 25 parts of ethylene-vinyl acetate copolymer, and 27 parts of styrene-ethylene-butylene-styrene block copolymer , 6 parts of graphene oxide, 9 parts of butyl rubber, 4 parts of trioctyl trimellitate, 6 parts of modified talcum powder, 4 parts of flame retardant, 2 parts of lubricant, and 3 parts of antioxidant.
[0042] Wherein, the preparation method of described modified talcum powder is as follows:
[0043] Soak the talc powder in the mixed solution of sodium carbonate and potassium permanganate for 3 hours, take it out and dry it, add silane coupling agent KH550 equivalent to 3% of the weight of the talc powder, and sodium lauryl sulfate equivalent to 2% of the weight of the talc powder Stir with alumina equivalent to 2% of the weight of talcum powder at 1000r / min for 20 minutes, then grind, and ...
Embodiment 3
[0055] This embodiment relates to an insulating and heat-conducting cable material, including the following raw materials in parts by weight: 23 parts of polyvinyl chloride resin, 17 parts of ethylene-vinyl acetate copolymer, and 20 parts of styrene-ethylene-butylene-styrene block copolymer , 4 parts of graphene oxide, 7 parts of butyl rubber, 3.2 parts of trioctyl trimellitate, 3.3 parts of modified talcum powder, 2.8 parts of flame retardant, 1.2 parts of lubricant, and 2.1 parts of antioxidant.
[0056] Wherein, the preparation method of described modified talcum powder is as follows:
[0057] Soak the talc powder in the mixed solution of sodium carbonate and potassium permanganate for 3 hours, take it out and dry it, add silane coupling agent KH550 equivalent to 3% of the weight of the talc powder, and sodium lauryl sulfate equivalent to 2% of the weight of the talc powder Stir with alumina equivalent to 2% of the weight of talcum powder at 1000r / min for 20 minutes, then g...
PUM
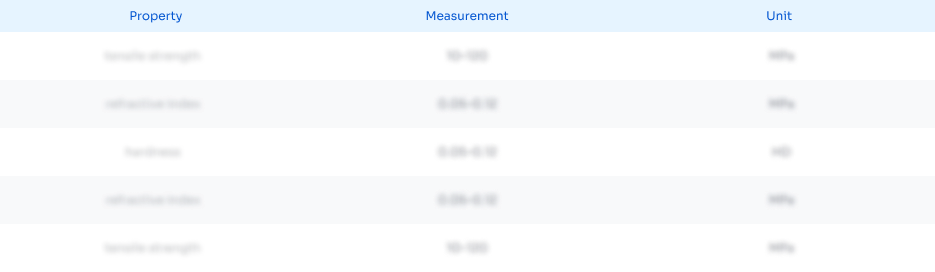
Abstract
Description
Claims
Application Information

- Generate Ideas
- Intellectual Property
- Life Sciences
- Materials
- Tech Scout
- Unparalleled Data Quality
- Higher Quality Content
- 60% Fewer Hallucinations
Browse by: Latest US Patents, China's latest patents, Technical Efficacy Thesaurus, Application Domain, Technology Topic, Popular Technical Reports.
© 2025 PatSnap. All rights reserved.Legal|Privacy policy|Modern Slavery Act Transparency Statement|Sitemap|About US| Contact US: help@patsnap.com