Method for synthesizing molybdenum disulfide-carbon nitride composite photocatalytic material
A technology of molybdenum disulfide and composite materials, applied in chemical instruments and methods, physical/chemical process catalysts, chemical/physical processes, etc., to achieve the effect of improving the catalytic effect of visible light
- Summary
- Abstract
- Description
- Claims
- Application Information
AI Technical Summary
Problems solved by technology
Method used
Image
Examples
Embodiment 1
[0026] Put 10 grams of urea in a crucible and calcined at 500°C for 2 hours to obtain light yellow carbon nitride powder.
[0027] Dissolve 0.2 g of carbon nitride and 0.346 g of PEI (50% aqueous solution) in 30 ml of deionized water, stir ultrasonically for 30 minutes, then add 0.348 g of sodium molybdate dihydrate and 0.454 g of cysteine, and then add Deionized water up to 60 ml, stirred for 2 hours. Then the solution was transferred to a 100ml polytetrafluoroethylene reactor and reacted at 220°C for 20 hours. After the reactor was naturally cooled to room temperature, the black solid product was separated by centrifugation, washed with deionized water and absolute ethanol three times each, and dried in a vacuum oven at 70°C for 12 hours. The final product was heat-treated at 450 °C for 5 minutes in a nitrogen atmosphere in a tube furnace to obtain a molybdenum sulfide-carbon nitride composite material, in which the mass ratio of molybdenum disulfide to carbon nitride was 1...
Embodiment 2
[0030] Put 10 grams of urea in a crucible and calcined at 520° C. for 2 hours to obtain light yellow carbon nitride powder.
[0031] Dissolve 0.15 g of carbon nitride and 0.246 g of PEI (50% aqueous solution) in 30 ml of deionized water, stir ultrasonically for 30 minutes, then add 0.348 g of sodium molybdate dihydrate and 0.696 g of cysteine, and then add Deionized water up to 60 ml, stirred for 2 hours. Then the solution was transferred to a 100ml polytetrafluoroethylene reactor and reacted at 200°C for 24 hours. After the reaction kettle was naturally cooled to room temperature, the black solid product was separated by centrifugal washing, washed with deionized water and absolute ethanol three times each, and dried in a vacuum oven at 70°C for 12 hours. The final product was heat-treated at 430 °C for 5 minutes in a nitrogen atmosphere in a tube furnace to obtain a molybdenum sulfide-carbon nitride composite material, in which the mass ratio of molybdenum disulfide to carb...
Embodiment 3
[0033] Put 10 grams of urea in a crucible, and calcined at 550° C. for 2 hours to obtain light yellow carbon nitride powder.
[0034] Dissolve 0.1 g of carbon nitride and 0.162 g of PEI (50% aqueous solution) in 30 ml of deionized water, stir ultrasonically for 30 minutes, then add 0.348 g of sodium molybdate dihydrate and 0.454 g of cysteine, and then add Deionized water up to 60 ml, stirred for 2 hours. Then the solution was transferred to a 100ml polytetrafluoroethylene reactor and reacted at 180°C for 24 hours. After the reaction kettle was naturally cooled to room temperature, the black solid product was separated by centrifugal washing, washed with deionized water and absolute ethanol three times each, and dried in a vacuum oven at 70°C for 12 hours. The final product was heat-treated at 400° C. for 5 minutes in a nitrogen atmosphere in a tube furnace to obtain a molybdenum sulfide-carbon nitride composite material, wherein the mass ratio of molybdenum disulfide to carb...
PUM
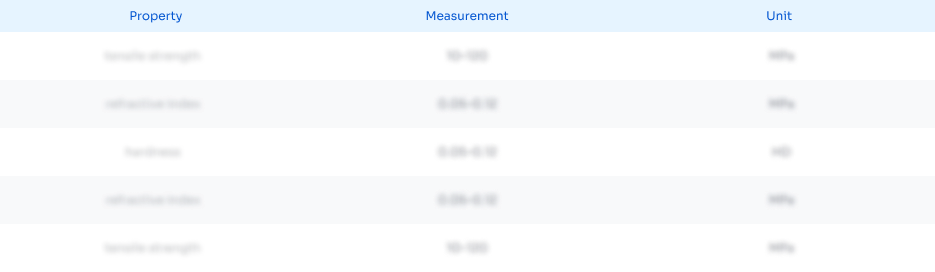
Abstract
Description
Claims
Application Information

- R&D
- Intellectual Property
- Life Sciences
- Materials
- Tech Scout
- Unparalleled Data Quality
- Higher Quality Content
- 60% Fewer Hallucinations
Browse by: Latest US Patents, China's latest patents, Technical Efficacy Thesaurus, Application Domain, Technology Topic, Popular Technical Reports.
© 2025 PatSnap. All rights reserved.Legal|Privacy policy|Modern Slavery Act Transparency Statement|Sitemap|About US| Contact US: help@patsnap.com