High-heat conduction wear-resistant high-temperature resistant composite material and preparation method thereof
A composite material and high temperature resistant technology, applied in heat exchange materials, chemical instruments and methods, etc., can solve the problems of low thermal conductivity and reduce other properties of polymer materials, achieve low thermal conductivity, improve thermal conductivity and mechanical properties. , Excellent waterproof and impermeability
- Summary
- Abstract
- Description
- Claims
- Application Information
AI Technical Summary
Problems solved by technology
Method used
Image
Examples
Embodiment 1
[0031] The preparation method of modified graphene comprises the following steps:
[0032] 1) graphene is added in the ethanol solution of pimelic acid and carried out ultrasonic dispersion, obtains the alcohol dispersion liquid of carboxylated graphene;
[0033] 2) Add sodium metaaluminate to the alcohol dispersion of carboxylated graphene, then carry out stirring reaction, centrifuge after the reaction finishes, obtain filtrate;
[0034] 3) Heat the filtrate to 400°C at a heating rate of 1°C / min under a nitrogen atmosphere, and keep it warm for 3 hours. The mass ratio of graphene to pimelic acid is 1:6, and the mass ratio of graphene to sodium metaaluminate is 1:3.
[0035] The preparation method of modified calcium sulfate whisker comprises the following steps:
[0036] Add calcium sulfate whiskers and zinc sulfate to acetone, carry out ultrasonic dispersion to obtain a dispersion liquid, raise the temperature of the dispersion liquid to 70°C, then add aluminate coupling ...
Embodiment 2
[0038] The preparation method of modified graphene comprises the following steps:
[0039] 1) graphene is added in the propanol solution of pimelic acid and carries out ultrasonic dispersion, obtains the alcohol dispersion liquid of carboxylated graphene;
[0040] 2) Add sodium metaaluminate to the alcohol dispersion of carboxylated graphene, then carry out stirring reaction, centrifuge after the reaction finishes, obtain filtrate;
[0041] 3) Heat the filtrate to 600°C at a heating rate of 5°C / min under nitrogen atmosphere, and keep it warm for 1h. The mass ratio of graphene to pimelic acid is 1:2, and the mass ratio of graphene to sodium metaaluminate is 1:7.
[0042] The preparation method of modified calcium sulfate whisker comprises the following steps:
[0043] Add calcium sulfate whiskers and zinc sulfate to acetone, carry out ultrasonic dispersion to obtain a dispersion liquid, heat the dispersion liquid to 80°C, then add aluminate coupling agent for ultrasonic vibra...
Embodiment 3
[0045] A high thermal conductivity, wear-resistant and high-temperature resistant composite material, calculated in parts by weight, includes the following raw materials:
[0046] 70 parts of nylon, 14 parts of silicone modified polyester acrylate, 2 parts of modified calcium sulfate whiskers of Example 1, 7 parts of magnesium oxide, 24 parts of modified graphene of Example 1, maleic anhydride grafted ethylene - 6 parts of octene copolymer, 1.2 parts of styrene-maleic anhydride copolymer, 0.4 part of polyethylene wax and 0.4 part of hindered phenolic antioxidant.
[0047] Preparation method of high thermal conductivity, wear-resistant and high-temperature resistant composite material:
[0048] 1) Nylon, maleic anhydride grafted ethylene-octene copolymer, magnesium oxide and the modified graphene in Example 1 were mixed and stirred evenly, then added to a twin-screw extruder, and extruded at 260°C Granulating to obtain thermally conductive nylon masterbatch;
[0049] 2) The h...
PUM
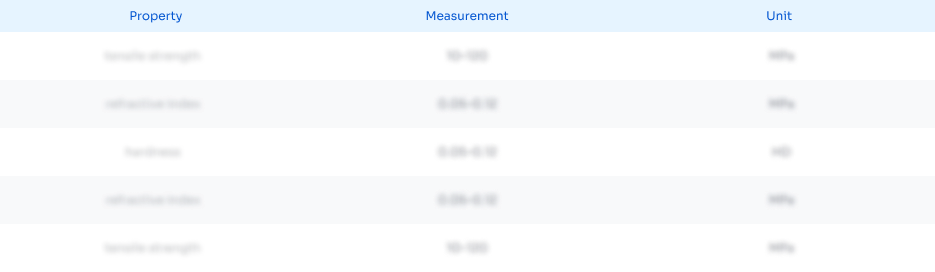
Abstract
Description
Claims
Application Information

- R&D Engineer
- R&D Manager
- IP Professional
- Industry Leading Data Capabilities
- Powerful AI technology
- Patent DNA Extraction
Browse by: Latest US Patents, China's latest patents, Technical Efficacy Thesaurus, Application Domain, Technology Topic, Popular Technical Reports.
© 2024 PatSnap. All rights reserved.Legal|Privacy policy|Modern Slavery Act Transparency Statement|Sitemap|About US| Contact US: help@patsnap.com