Metallographic sample preparation method of CrMo steel
A metallographic sample preparation and electrolyte technology, which is applied in the preparation of test samples, etc., to achieve the effects of simple and easy operation, conducive to metallographic observation, and promotion of corrosion.
- Summary
- Abstract
- Description
- Claims
- Application Information
AI Technical Summary
Problems solved by technology
Method used
Image
Examples
Embodiment 1
[0021] (1) Preparation of the working electrode of the sample: the sample used is 35CrMo steel, and a square sample with a size of 10mm×10mm is obtained by an electric spark cutting machine, and then the wire is welded on the surface of the sample and then sealed with epoxy resin. Obtain the primary sample electrode. Roughly grind the primary sample electrode on 180#, 320#, 600# sandpaper, and then finely grind it with 800#, 1000#, 1200 sandpaper (when changing the sandpaper, use the same grinding direction as the previous sandpaper). vertical direction), and then mechanically polish it on a polishing machine with a diamond polishing paste of W1.5, so that its roughness Ra reaches 0.4 μm, and then the sample working electrode (its preparation and structural schematic diagram as shown in figure 1 shown).
[0022] (2) Electrolyte configuration: Pour 8g of sodium chloride and 392g of tap water into a clean container, and stir until the sodium chloride is completely dissolved to ...
Embodiment 2
[0026] (1) Preparation of the working electrode of the sample: the sample used is 35CrMo steel, and a square sample with a size of 10mm×10mm is obtained by an electric spark cutting machine, and then the wire is welded on the surface of the sample and then sealed with epoxy resin. Obtain the primary sample electrode. Roughly grind the primary sample electrode on 180#, 320#, 600# sandpaper, and then finely grind it with 800#, 1000#, 1200 sandpaper (when changing the sandpaper, use the same grinding direction as the previous sandpaper). Vertical direction), and then use W1.5 diamond polishing paste to mechanically polish it on a polishing machine, so that the roughness Ra reaches 0.4 μm, and the working electrode of the sample is obtained.
[0027] Electrolyte configuration: Pour 14g of sodium chloride and 386g of tap water into a clean container, and stir until all the sodium chloride is dissolved to make a NaCl solution with a concentration of 3.5%, and heat the solution to 30...
Embodiment 3
[0031] (1) Preparation of the working electrode of the sample: the sample used is 35CrMo steel, and a square sample with a size of 15mm×15mm is obtained by an electric spark cutting machine, and then the wire is welded on the surface of the sample and then sealed with epoxy resin. Obtain the primary sample electrode. Roughly grind the primary sample electrode on 180#, 320#, 600# sandpaper, and then finely grind it with 800#, 1000#, 1200 sandpaper (when changing the sandpaper, use the same grinding direction as the previous sandpaper). vertical direction), and then mechanically polish it on a polishing machine with W1.5 diamond polishing paste to make the roughness Ra reach 0.2 μm, that is, the working electrode of the sample is obtained.
[0032] Electrolyte configuration: Pour 16g of sodium chloride and 384g of tap water into a clean container, and stir until all the sodium chloride is dissolved to make a NaCl solution with a concentration of 4.0%, and heat the solution to 25...
PUM
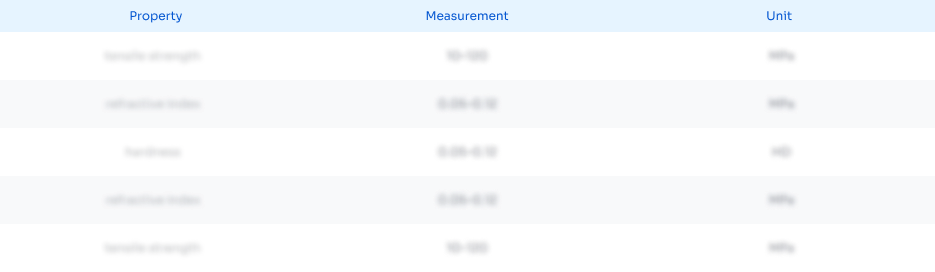
Abstract
Description
Claims
Application Information

- R&D Engineer
- R&D Manager
- IP Professional
- Industry Leading Data Capabilities
- Powerful AI technology
- Patent DNA Extraction
Browse by: Latest US Patents, China's latest patents, Technical Efficacy Thesaurus, Application Domain, Technology Topic, Popular Technical Reports.
© 2024 PatSnap. All rights reserved.Legal|Privacy policy|Modern Slavery Act Transparency Statement|Sitemap|About US| Contact US: help@patsnap.com