Preparation method of cross-linked polyimide fiber membrane
A technology of polyimide fiber and fiber film, which is applied in fiber treatment, fiber type, textile and papermaking, etc., can solve the problems of limited types of polyimide, negative impact on mechanical properties, and limited use range, etc., and achieve cross-linking Adjustable and controllable, easy to meet conditions, low cost effect
- Summary
- Abstract
- Description
- Claims
- Application Information
AI Technical Summary
Problems solved by technology
Method used
Image
Examples
Embodiment 1
[0025] Preparation of PMDA / ODA system cross-linked polyimide fiber membrane: (1) Weigh 2.0 g of pyromellitic dianhydride (PMDA), 4,4'-diaminodiphenyl ether (ODA) with a molar ratio of 1:1 ) 1.8g, all ODA was dissolved in 30ml of N,N-dimethylformamide (DMF) solvent, mechanically stirred, after all ODA was dissolved in DMF, under the condition of ice-water bath, PMDA was added step by step to obtain the viscosity After adding a moderate amount of polyamic acid solution, after mechanical stirring for 2 hours, put the polyamic acid solution into a 20ml syringe, and use electrospinning technology to prepare polyamic acid fiber membranes. The specific parameters of the electrospinning machine are spinning voltage: 20kV ; Spinning temperature: room temperature; Spinning humidity: 20%; Syringe needle diameter: No. 12; Receiving roll speed: 80.0m / min; Receiving distance: 20cm. The prepared polyamic acid fiber membrane was placed in a clean bench for 12 hours; (2) the polyamic acid fibe...
Embodiment 2
[0027] Preparation of PMDA / ODA system cross-linked polyimide fiber membrane: (1) Weigh 2.0 g of pyromellitic dianhydride (PMDA), 4,4'-diaminodiphenyl ether (ODA) with a molar ratio of 1:1 ) 1.8g, all ODA was dissolved in 30ml of N,N-dimethylformamide (DMF) solvent, mechanically stirred, after all ODA was dissolved in DMF, under the condition of ice-water bath, PMDA was added step by step to obtain the viscosity After adding a moderate amount of polyamic acid solution, after mechanical stirring for 2 hours, put the polyamic acid solution into a 20ml syringe, and use electrospinning technology to prepare polyamic acid fiber membranes. The specific parameters of the electrospinning machine are spinning voltage: 20kV ; Spinning temperature: room temperature; Spinning humidity: 20%; Syringe needle diameter: No. 12; Receiving roll speed: 80.0m / min; Receiving distance: 20cm. The prepared polyamic acid fiber membrane was placed in a clean bench for 12 hours; (2) the polyamic acid fibe...
Embodiment 3
[0029]Preparation of PMDA / ODA system cross-linked polyimide fiber membrane: (1) Weigh 2.0 g of pyromellitic dianhydride (PMDA), 4,4'-diaminodiphenyl ether (ODA) with a molar ratio of 1:1 ) 1.8g, all ODA was dissolved in 30ml of N,N-dimethylformamide (DMF) solvent, mechanically stirred, after all ODA was dissolved in DMF, under the condition of ice-water bath, PMDA was added step by step to obtain the viscosity After adding a moderate amount of polyamic acid solution, after mechanical stirring for 2 hours, put the polyamic acid solution into a 20ml syringe, and use electrospinning technology to prepare polyamic acid fiber membranes. The specific parameters of the electrospinning machine are spinning voltage: 20kV ; Spinning temperature: room temperature; Spinning humidity: 20%; Syringe needle diameter: No. 12; Receiving roll speed: 80.0m / min; Receiving distance: 20cm. The prepared polyamic acid fiber membrane was placed in a clean bench for 12 hours; (2) the polyamic acid fiber...
PUM
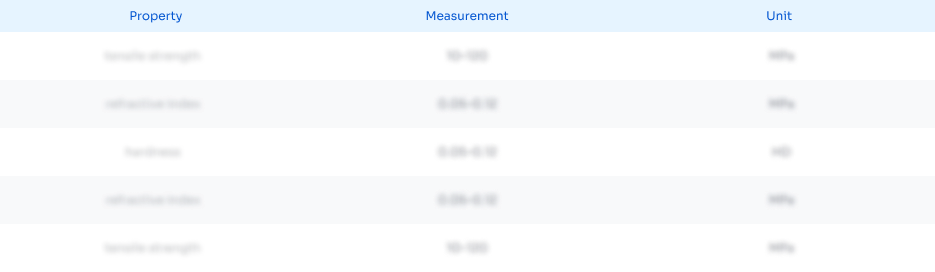
Abstract
Description
Claims
Application Information

- R&D Engineer
- R&D Manager
- IP Professional
- Industry Leading Data Capabilities
- Powerful AI technology
- Patent DNA Extraction
Browse by: Latest US Patents, China's latest patents, Technical Efficacy Thesaurus, Application Domain, Technology Topic, Popular Technical Reports.
© 2024 PatSnap. All rights reserved.Legal|Privacy policy|Modern Slavery Act Transparency Statement|Sitemap|About US| Contact US: help@patsnap.com