Method for efficiently separating copper and arsenic in copper smelting smoke dust
A technology of copper smelting and dust, which is applied in the field of separation of copper and arsenic from copper smelting dust, can solve the problems of long process, low leaching rate, unfavorable extraction process, etc., achieve high-efficiency separation, facilitate production operation, and simplify the process.
- Summary
- Abstract
- Description
- Claims
- Application Information
AI Technical Summary
Problems solved by technology
Method used
Image
Examples
Embodiment 1
[0022] Take 100g of copper smelting dust, the main components are 12.57% of copper, 3.46% of arsenic, 15.52% of lead, 2.9% of bismuth, 14.97% of zinc, and 11.73% of sulfur, add 500ml of water for slurry, add 25g of concentrated sulfuric acid after slurry In a water bath at 85°C, start a period of normal pressure leaching and react for 2 hours. After the reaction is over, the arsenic leaching rate is greater than 60%, and the leaching residue continues to be subjected to the second-stage oxygen-enriched pressure leaching. The controlled pressure leaching conditions are: liquid-solid ratio 5:1, initial acidity 100g / L, reaction temperature 150°C, oxygen partial pressure 5atm, reaction time 2h. After two stages of leaching, the leaching rate of copper and arsenic is greater than 90%, lead and bismuth are enriched in the leaching residue, and the leaching solution is reduced and crystallized to produce white arsenic.
Embodiment 2
[0024] Take 500g of copper smelting dust, the main components are 11.52% copper, 13.71% arsenic, 20.78% lead, 1.91% zinc, 1.45% iron, 3.13% bismuth, and 5.45% sulfur. The concentration of sulfuric acid is 5%, and the reaction time is 2 hours for a period of normal pressure leaching, and the leaching rate of copper and arsenic can reach more than 90%. After liquid-solid separation, the first-stage leaching residue is subjected to second-stage pressure leaching. The controlled pressure leaching conditions are: liquid-solid ratio 4:1, initial acidity 120g / L, reaction temperature 140°C, oxygen partial pressure 3atm, reaction time 2h. After two stages of leaching, the leaching rate of copper and arsenic is greater than 95%, realizing the efficient removal of arsenic.
PUM
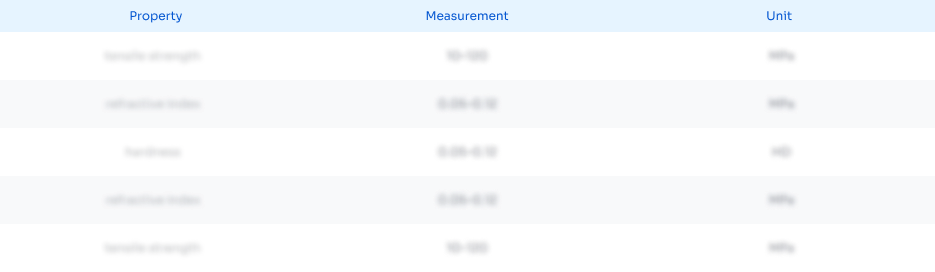
Abstract
Description
Claims
Application Information

- Generate Ideas
- Intellectual Property
- Life Sciences
- Materials
- Tech Scout
- Unparalleled Data Quality
- Higher Quality Content
- 60% Fewer Hallucinations
Browse by: Latest US Patents, China's latest patents, Technical Efficacy Thesaurus, Application Domain, Technology Topic, Popular Technical Reports.
© 2025 PatSnap. All rights reserved.Legal|Privacy policy|Modern Slavery Act Transparency Statement|Sitemap|About US| Contact US: help@patsnap.com