Preparation method of full-synthetic type cutting fluid
A cutting fluid, fully synthetic technology, used in lubricating compositions, petroleum industry, etc., can solve the problems of high post-treatment cost, poor extreme pressure lubrication performance and anti-rust performance, poor cooling performance, etc., and achieve excellent extreme pressure lubrication performance. and anti-rust performance, avoid discoloration, improve the effect of stability
- Summary
- Abstract
- Description
- Claims
- Application Information
AI Technical Summary
Problems solved by technology
Method used
Image
Examples
Embodiment 1
[0015] A preparation method of fully synthetic cutting fluid, comprising the following steps:
[0016] (1) In parts by weight, after mixing 17 parts of boric acid and 12 parts of triethanolamine, heating to 140°C, and heat preservation treatment for 4 hours, triethanolamine borate was obtained;
[0017] (2) In parts by weight, add 23 parts of samarium chloride and 30 parts of lanthanum chloride to 110 parts of water, then add 55 parts of naphthenic acid to it, mix and stir evenly, and raise the temperature of the mixture to 88°C , thermal insulation treatment for 3 hours, prepared naphthenic acid rare earth mixture;
[0018] (3) In parts by weight, 44 parts of triethanolamine borate, 11 parts of rare earth naphthenic acid mixture, 2 parts of sodium hyposulfite, 7 parts of polyglycerol monostearate, 1 part of polyoxyethylene sorbitan monolaurate , 5 parts of calcium stearoyl lactylate, and 150 parts of deionized water were evenly mixed, and ultrasonically treated for 20 minute...
Embodiment 2
[0022] A preparation method of fully synthetic cutting fluid, comprising the following steps:
[0023] (1) In parts by weight, after mixing 21 parts of boric acid and 14 parts of triethanolamine, heating to 145°C, and heat preservation treatment for 4.5 hours, boric acid triethanolamine was obtained;
[0024] (2) In parts by weight, add 25 parts of samarium chloride and 33 parts of lanthanum chloride to 130 parts of water, then add 58 parts of naphthenic acid to it, mix and stir evenly, and raise the temperature of the mixture to 90°C , thermal insulation treatment for 3.5 hours, prepared naphthenic acid rare earth mixture;
[0025] (3) In parts by weight, 46 parts of triethanolamine borate, 13 parts of rare earth naphthenic acid mixture, 3 parts of sodium hyposulfite, 9 parts of polyglycerol monostearate, 3 parts of polyoxyethylene sorbitan monolaurate , 6 parts of calcium stearoyl lactylate, and 180 parts of deionized water were evenly mixed, and ultrasonically treated for ...
Embodiment 3
[0029] A preparation method of fully synthetic cutting fluid, comprising the following steps:
[0030] (1) In parts by weight, after mixing 25 parts of boric acid and 16 parts of triethanolamine, heating to 150°C, and heat preservation treatment for 5 hours, triethanolamine borate was obtained;
[0031] (2) In parts by weight, add 26 parts of samarium chloride and 35 parts of lanthanum chloride to 150 parts of water, then add 60 parts of naphthenic acid to it, mix and stir evenly, and raise the temperature of the mixture to 92°C , thermal insulation treatment for 3-4 hours, prepared naphthenic acid rare earth mixture;
[0032] (3) In parts by weight, 50 parts of triethanolamine borate, 13 parts of rare earth naphthenic acid mixture, 4 parts of sodium hyposulfite, 10 parts of polyglycerol monostearate, 4 parts of polyoxyethylene sorbitan monolaurate , 7 parts of calcium stearoyl lactylate, and 200 parts of deionized water were evenly mixed, and ultrasonically treated for 30 mi...
PUM
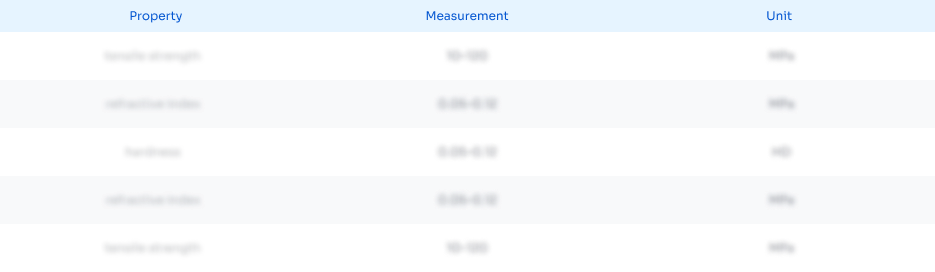
Abstract
Description
Claims
Application Information

- Generate Ideas
- Intellectual Property
- Life Sciences
- Materials
- Tech Scout
- Unparalleled Data Quality
- Higher Quality Content
- 60% Fewer Hallucinations
Browse by: Latest US Patents, China's latest patents, Technical Efficacy Thesaurus, Application Domain, Technology Topic, Popular Technical Reports.
© 2025 PatSnap. All rights reserved.Legal|Privacy policy|Modern Slavery Act Transparency Statement|Sitemap|About US| Contact US: help@patsnap.com