A kind of preparation method of lamellar porous carbon nitride
A porous carbon nitride and lamellar technology, which is applied in the field of photocatalytic material preparation, can solve the problems of complex preparation process and high cost of lamellar porous carbon nitride, achieve good photocatalytic performance, low cost, and increase specific surface area Effect
- Summary
- Abstract
- Description
- Claims
- Application Information
AI Technical Summary
Problems solved by technology
Method used
Image
Examples
preparation example Construction
[0023] The invention relates to a preparation method of lamellar porous carbon nitride, which uses carbon and nitrogen precursors, dyes and water as raw materials, first adopts dye-assisted hydrothermal treatment of conventional carbon and nitrogen precursors to prepare modified precursors; then the above modified The lamellar porous carbon nitride can be obtained by calcining the precursor at high temperature.
[0024] Specifically follow the steps below:
[0025] Step 1, preparation of modified precursor:
[0026] Weigh the carbon-nitrogen precursor, put it into a clean polytetrafluoroethylene lining, and then add dye and deionized water; the mass ratio of carbon-nitrogen precursor to deionized water is 1:2 to 1:50, and the dye The mass ratio to deionized water is 1:100~1:500000. After stirring evenly, cover the lid and move it into the corresponding stainless steel reactor jacket, and keep it in an oven at 110~210°C for 10~100h. After cooling in the furnace, the obtained ...
Embodiment 1
[0033] Step 1, according to the mass ratio of melamine and deionized water is 1:10, and the mass ratio of rhodamine B and deionized water is 1:6000, add melamine, rhodamine B, and deionized water into clean polytetrafluoroethylene Mix in the lining and stir evenly; cover the above-mentioned polytetrafluoroethylene lining with a lid, put it into the corresponding stainless steel jacket, tighten it, put it in an oven, and keep it warm at 200 ° C for 12 hours; after cooling with the furnace, the obtained solid-liquid mixture , with deionized water and absolute ethanol, respectively, centrifuged and washed 5 times; then dried in an oven at 70 ° C for 20 h, and the light pink modified melamine precursor can be obtained.
[0034] Step 2. Put the precursor obtained in step 1 into an alumina crucible and cover it; heat preservation at 550°C for 4 hours, and calcining at a heating rate of 0.5°C / min to obtain light yellow lamellar porous nitrogen carbonized.
[0035] The g-C that embod...
Embodiment 2
[0037] Step 1, according to the mass ratio of melamine and deionized water is 1:10, and the mass ratio of methyl orange and deionized water is 1:2000, add melamine, methyl orange and deionized water into clean polytetrafluoroethylene Mix in the lining and stir evenly; cover the above-mentioned polytetrafluoroethylene lining with a lid, put it into the corresponding stainless steel jacket, tighten it, put it in an oven, and keep it warm at 200 ° C for 12 hours; after cooling with the furnace, the obtained solid-liquid mixture , respectively centrifuged and washed 6 times with deionized water and absolute ethanol; then dried in an oven at 60° C. for 24 hours to obtain a brown modified melamine precursor.
[0038] Step 2, put the precursor obtained in step 1 into an alumina crucible, and cover it; heat preservation at 550°C for 4 hours, and calcining at a heating rate of 0.5°C / min to obtain brown lamellar porous nitriding carbon.
[0039] The g-C that embodiment 2 obtains 3 N ...
PUM
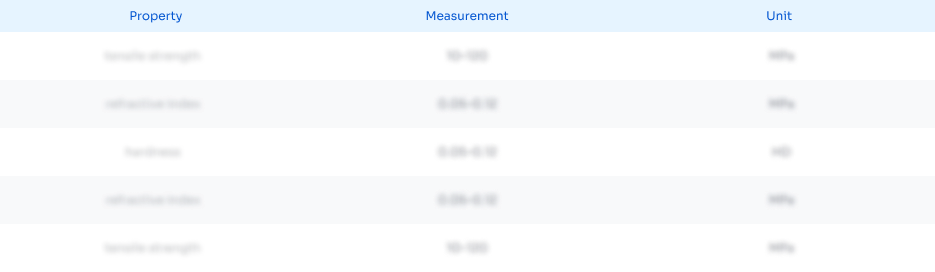
Abstract
Description
Claims
Application Information

- R&D
- Intellectual Property
- Life Sciences
- Materials
- Tech Scout
- Unparalleled Data Quality
- Higher Quality Content
- 60% Fewer Hallucinations
Browse by: Latest US Patents, China's latest patents, Technical Efficacy Thesaurus, Application Domain, Technology Topic, Popular Technical Reports.
© 2025 PatSnap. All rights reserved.Legal|Privacy policy|Modern Slavery Act Transparency Statement|Sitemap|About US| Contact US: help@patsnap.com