Process for recovering nickel cobalt lithium manganate positive electrode material by taking waste lithium ion battery as raw material
A technology of lithium ion battery and lithium nickel cobalt manganate, applied in the field of waste lithium ion battery recycling, can solve the problems of high price of organic acid and hydrogen peroxide, increase industrial cost and environmental pressure, increase industrial recycling cost, etc. Controlled, pH stable, simple steps to effect
- Summary
- Abstract
- Description
- Claims
- Application Information
AI Technical Summary
Problems solved by technology
Method used
Image
Examples
Embodiment 1
[0033] A kind of technology that reclaims and prepares nickel cobalt lithium manganese oxide cathode material with waste lithium ion battery as raw material comprises the following steps:
[0034] (1) Pulverize the positive electrode sheet of the battery cell, pyrolyze it in air at 400° C., and sieve it with a 200-mesh standard sieve under vibration to obtain 10 g of positive electrode powder.
[0035] (2) Add 28 g of ammonium sulfate to the positive electrode powder and mix well, and then bake in a muffle furnace under the condition of air ventilation, the roasting temperature is 470° C., and the roasting time is 2 hours. Then add 100 mL of deionized water to the roasted product, perform leaching at 60° C., and filter to obtain the leaching solution.
[0036] (3) Remove impurity iron by yellow sodium iron vanadium method in leaching solution, after hydrolysis method removes impurity aluminum at the same time, measure and analyze the nickel ion concentration in the leaching so...
Embodiment 2
[0043] A kind of technology that reclaims and prepares nickel cobalt lithium manganese oxide cathode material with waste lithium ion battery as raw material comprises the following steps:
[0044] (1) The positive electrode sheet of the battery cell was crushed, pyrolyzed in air at 400° C., and sieved with a 200-mesh standard sieve under vibration to obtain 9.8 g of positive electrode powder.
[0045] (2) Add 29g of ammonium sulfate + 3g of urea to the positive electrode powder and mix well, and then roast in a muffle furnace under an ammonia gas atmosphere, the roasting temperature is 450°C, and the roasting time is 1.5h. Then add 100 mL of deionized water to the roasted product, perform leaching at 60° C., and filter to obtain the leaching solution.
[0046] (3) Remove impurity iron by yellow sodium iron vanadium method in leaching liquid, after hydrolysis method removes impurity aluminum, record the nickel ion concentration in leaching liquid to be 0.94mol L -1 , the cobal...
Embodiment 3
[0051] A kind of technology that reclaims and prepares nickel cobalt lithium manganese oxide cathode material with waste lithium ion battery as raw material comprises the following steps:
[0052] (1) Disassemble the battery cell, take out the positive electrode sheet; crush the positive electrode sheet, pyrolyze it at 400°C in an atmosphere of ammonia + nitrogen (1:1), and sieve it with a 200-mesh standard sieve under vibration to obtain Positive electrode powder 11g.
[0053] (2) Add 31 g of ammonium sulfate + 5 g of ammonium bicarbonate to the positive electrode powder and mix well, and then roast in a muffle furnace under an ammonia gas atmosphere, the roasting temperature is 470 ° C, and the roasting time is 1.5 h. Then add 100 mL of deionized water to the roasted product, perform leaching at 60° C., and filter to obtain the leaching solution.
[0054] (3) After removing the impurity iron and the hydrolysis method to remove the impurity aluminum in the leaching solution,...
PUM
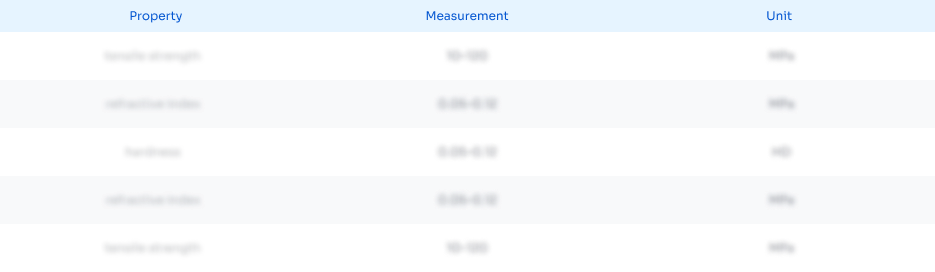
Abstract
Description
Claims
Application Information

- R&D
- Intellectual Property
- Life Sciences
- Materials
- Tech Scout
- Unparalleled Data Quality
- Higher Quality Content
- 60% Fewer Hallucinations
Browse by: Latest US Patents, China's latest patents, Technical Efficacy Thesaurus, Application Domain, Technology Topic, Popular Technical Reports.
© 2025 PatSnap. All rights reserved.Legal|Privacy policy|Modern Slavery Act Transparency Statement|Sitemap|About US| Contact US: help@patsnap.com