Silver tungsten carbide graphene electrical contact material and preparation method thereof
An electrical contact material, tungsten carbide graphite technology, which is applied in the field of silver tungsten carbide graphene electrical contact material and its preparation, can solve the problems of no significant characteristics of anti-fusion welding performance, large difference in the proportion of graphite, increase in product cost, etc. Make up for the effects of large and unstable contact resistance, high density, and improved reliability
- Summary
- Abstract
- Description
- Claims
- Application Information
AI Technical Summary
Problems solved by technology
Method used
Image
Examples
preparation example Construction
[0051] Such as figure 1 As shown, this figure is a flow chart of the preparation method of the silver tungsten carbide graphene electrical contact material when the tungsten carbide content of the present invention is 12wt%-25wt%, and the preparation process of the silver tungsten carbide graphene electrical contact material can be carried out sequentially according to this process , and individual steps can also be selected according to actual application requirements.
[0052] Such as figure 2 As shown, this figure is a flow chart of the preparation process of the silver tungsten carbide graphene electrical contact material when the tungsten carbide content of the present invention is greater than 25wt% and less than or equal to 85wt%. The preparation process of the silver tungsten carbide graphene electrical contact material can be according to this The process is carried out sequentially, and individual steps can also be selected according to actual application requireme...
Embodiment 1
[0055] This embodiment provides the preparation of a silver / tungsten carbide / graphene / nickel electrical contact material, the operation steps are as follows:
[0056] Ⅰ) Material composition of silver / tungsten carbide / graphene / nickel electrical contact materials
[0057] The material components of silver / tungsten carbide / graphene / nickel electrical contact materials are mainly metallic silver, tungsten carbide, graphene, and metallic nickel, wherein the content of tungsten carbide is 12wt%, the content of graphene is 0.1wt%, and the content of nickel is 0.5wt% %, the balance being silver.
[0058] Ⅱ) Basic steps for preparing silver / tungsten carbide / graphene / nickel electrical contact materials (see attached figure 1 )
[0059] 1) Prepare 0.1mol / L silver nitrate solution, 0.1mol / L nickel nitrate solution, 0.1mol / L ascorbic acid solution (or one or more of glucose, citric acid or oxalic acid).
[0060] 2) According to the composition of the material, a quantitative ascorbic ac...
Embodiment 2
[0066] The main difference from Example 1 is: the content of tungsten carbide in the product in Example 2 is 25wt%, the content of graphene is 3wt%, the content of nickel is 1.5wt%, and the balance is silver.
[0067] The basic operation steps for preparing silver / tungsten carbide / graphene / nickel electrical contact material in this embodiment 1 are as follows:
[0068] Ⅰ) Material composition of silver / tungsten carbide / graphene / nickel electrical contact materials
[0069] The material components of silver / tungsten carbide / graphene / nickel electrical contact materials are mainly metallic silver, tungsten carbide, graphene, and metallic nickel, wherein the content of tungsten carbide is 25wt%, the content of graphene is 3wt%, and the content of nickel is 1.5wt%. , and the balance is silver.
[0070] Ⅱ) Basic steps for preparing silver / tungsten carbide / graphene / nickel electrical contact materials (see attached figure 1 )
[0071] 1) Prepare 0.2mol / L silver nitrate solution, 0.2...
PUM
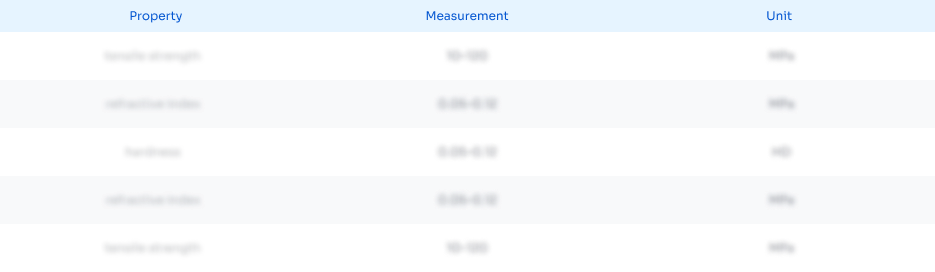
Abstract
Description
Claims
Application Information

- R&D
- Intellectual Property
- Life Sciences
- Materials
- Tech Scout
- Unparalleled Data Quality
- Higher Quality Content
- 60% Fewer Hallucinations
Browse by: Latest US Patents, China's latest patents, Technical Efficacy Thesaurus, Application Domain, Technology Topic, Popular Technical Reports.
© 2025 PatSnap. All rights reserved.Legal|Privacy policy|Modern Slavery Act Transparency Statement|Sitemap|About US| Contact US: help@patsnap.com