Preparation method and application of high-abrasion-resistant exterior wall coating
An exterior wall coating, high wear resistance technology, used in epoxy resin coatings, coatings and other directions, can solve the problems of easy cracking, coating failure, peeling, etc., to achieve good application prospects, improve performance, adhere to Strong effect
- Summary
- Abstract
- Description
- Claims
- Application Information
AI Technical Summary
Problems solved by technology
Method used
Image
Examples
Embodiment 1
[0022] (1) After mixing 7 parts of ferric oxide and 6 parts of titanium dioxide, the mixture powder is obtained by preliminary crushing, then 12 parts of sodium tetraborate is added to the mixture powder and stirred evenly, transferred to a ball mill for full ball milling, and the ball material processed by ball milling The ratio is 12:1, the rotating speed of the ball mill is 2000 rpm, and the ball milling time is 90 minutes to obtain a preliminary mixture;
[0023] (2) Put the preliminary mixture obtained in step (1) into a drying oven, adjust the temperature in the drying oven to 75° C., and continue drying at this temperature for 8 hours to obtain a dry mixture;
[0024] (3) 55 parts of bisphenol A epoxy resin, 50 parts of melamine formaldehyde resin, 25 parts of lauryl dimethyl amine oxide, and 10 parts of methyl ethyl ketone peroxide are placed in the reactor, and then the dry mixture obtained in step (2) Put it into the reaction kettle, adjust the temperature of the rea...
Embodiment 2
[0029] (1) After mixing 8 parts of ferric oxide and 7 parts of titanium dioxide, the mixture powder is obtained by preliminary crushing, and then 14 parts of sodium tetraborate are added to the mixture powder and stirred evenly, transferred to a ball mill for full ball milling, and the ball material processed by ball milling The ratio is 12:1, the rotating speed of the ball mill is 2500 rpm, and the ball milling time is 105 minutes to obtain a preliminary mixture;
[0030] (2) Put the preliminary mixture obtained in step (1) into a drying oven, adjust the temperature in the drying oven to 80° C., and continue drying at this temperature for 10 hours to obtain a dry mixture;
[0031] (3) 60 parts of bisphenol A epoxy resin, 55 parts of melamine formaldehyde resin, 30 parts of lauryl dimethyl amine oxide, and 11 parts of methyl ethyl ketone peroxide are placed in the reactor, and then the dry mixture obtained in step (2) Put it into the reaction kettle, adjust the temperature of ...
Embodiment 3
[0036](1) After mixing 9 parts of ferric oxide and 8 parts of titanium dioxide, the mixture powder is obtained by preliminary crushing, then 16 parts of sodium tetraborate is added to the mixture powder and stirred evenly, transferred to a ball mill for full ball milling, and the ball material processed by ball milling The ratio is 12:1, the rotating speed of the ball mill is 3000 rpm, and the ball milling time is 120 minutes to obtain a preliminary mixture;
[0037] (2) Put the preliminary mixture obtained in step (1) into a drying oven, adjust the temperature in the drying oven to 85° C., and continue drying at this temperature for 12 hours to obtain a dry mixture;
[0038] (3) 65 parts of bisphenol A epoxy resin, 60 parts of melamine formaldehyde resin, 35 parts of lauryl dimethyl amine oxide, and 12 parts of methyl ethyl ketone peroxide are placed in the reactor, and then the dry mixture obtained in step (2) Put it into the reaction kettle, adjust the temperature of the re...
PUM
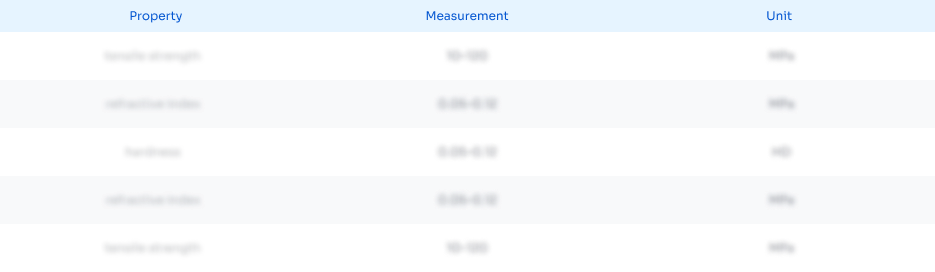
Abstract
Description
Claims
Application Information

- R&D Engineer
- R&D Manager
- IP Professional
- Industry Leading Data Capabilities
- Powerful AI technology
- Patent DNA Extraction
Browse by: Latest US Patents, China's latest patents, Technical Efficacy Thesaurus, Application Domain, Technology Topic, Popular Technical Reports.
© 2024 PatSnap. All rights reserved.Legal|Privacy policy|Modern Slavery Act Transparency Statement|Sitemap|About US| Contact US: help@patsnap.com