Molybdenum sulfide-based catalyst for preparing low-carbon alcohol from synthesis gas and preparation method thereof
A technology of alcohol molybdenum sulfide and catalyst, which is applied in the direction of catalyst activation/preparation, preparation of organic compounds, physical/chemical process catalysts, etc. It can solve the problems of few catalytic active sites and low activity, and achieve high selectivity and preparation of C2+ alcohols The effect of simple process and high selectivity of total alcohol
- Summary
- Abstract
- Description
- Claims
- Application Information
AI Technical Summary
Problems solved by technology
Method used
Image
Examples
Embodiment 1
[0017] Weigh 1.2359g ammonium heptamolybdate tetrahydrate and 1.0657g thiourea (Mo:S ratio 1:2) and dissolve in 75ml water, put the solution into a 100ml polytetrafluoroethylene reactor and seal it in a stainless steel shell. The reaction kettle was reacted in an oven at 220°C for 24h. After cooling to room temperature, the solid product was washed three times with water and once with ethanol, and dried at 60°C for 12h. Mix 0.7g of the product with 0.3g of potassium carbonate (Mo:K=1:1), mechanically grind for 1h, press into tablets and sieve to collect the 40-60 mesh catalyst. The K-MoS prepared by the above method 2 Catalysts were evaluated for catalytic performance in a stainless steel fixed-bed reactor. The inner diameter of the reactor is 8mm, the loading amount of the catalyst is 0.4g, the mixed 40-60 mesh quartz sand is filled in the constant temperature section, and the upper preheating section and the lower insulation section are filled with quartz sand. Reaction co...
Embodiment 2
[0019] Weigh 1.2359g ammonium heptamolybdate tetrahydrate and 1.0657g thiourea (Mo:S ratio 1:2) and dissolve in 75ml water, put the solution into a 100ml polytetrafluoroethylene reactor and seal it in a stainless steel shell. The reaction kettle was reacted in an oven at 220°C for 24h. After cooling to room temperature, the solid product was washed three times with water and once with ethanol, and dried at 60°C for 12h. Mix 0.7g of the product with 0.3g of potassium carbonate (Mo:K=1:1), mechanically grind for 1h, press into tablets and sieve to collect the 40-60 mesh catalyst. The K-MoS prepared by the above method 2 Catalysts were evaluated for catalytic performance in a stainless steel fixed-bed reactor. The inner diameter of the reactor is 8mm, the loading amount of the catalyst is 0.4g, the mixed 40-60 mesh quartz sand is filled in the constant temperature section, and the upper preheating section and the lower insulation section are filled with quartz sand. Reaction co...
Embodiment 3
[0021] Weigh 1.2359g of ammonium heptamolybdate tetrahydrate and 1.0657g of thiourea (Mo:S ratio 1:2) and dissolve them in 75ml of water, put the solution into a 100ml polytetrafluoroethylene reactor and seal it in a stainless steel shell. The reaction kettle was reacted in an oven at 220°C for 24h. After cooling to room temperature, the solid product was washed three times with water and once with ethanol, and dried at 60°C for 12h. Mix 0.7g of the product with 0.3g of potassium carbonate (Mo:K=1:1), mechanically grind for 1h, press into tablets and sieve to collect the 40-60 mesh catalyst. The K-MoS prepared by the above method 2 Catalysts were evaluated for catalytic performance in a stainless steel fixed-bed reactor. The inner diameter of the reactor is 8mm, the loading amount of the catalyst is 0.4g, the mixed 40-60 mesh quartz sand is filled in the constant temperature section, and the upper preheating section and the lower insulation section are filled with quartz sand...
PUM
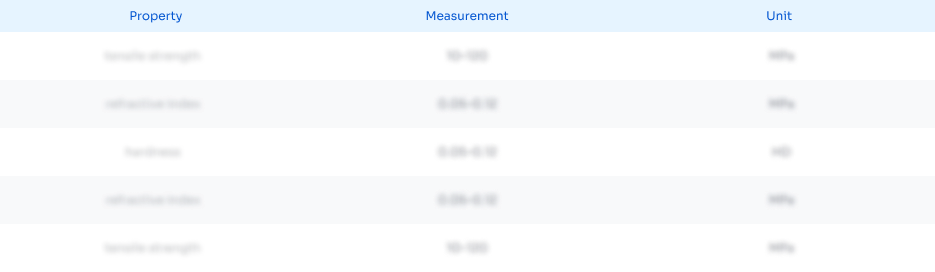
Abstract
Description
Claims
Application Information

- R&D
- Intellectual Property
- Life Sciences
- Materials
- Tech Scout
- Unparalleled Data Quality
- Higher Quality Content
- 60% Fewer Hallucinations
Browse by: Latest US Patents, China's latest patents, Technical Efficacy Thesaurus, Application Domain, Technology Topic, Popular Technical Reports.
© 2025 PatSnap. All rights reserved.Legal|Privacy policy|Modern Slavery Act Transparency Statement|Sitemap|About US| Contact US: help@patsnap.com