High-performance rotational moulding type urea box and preparation method thereof
A rotomolding, high-performance technology, applied in the field of high-performance rotomolding urea tank and its preparation, can solve the problems of burning, restricting the use of linear low-density polyethylene composite materials, human injury, etc., to increase compatibility, The effect of improving electrical conductivity and reducing surface energy
- Summary
- Abstract
- Description
- Claims
- Application Information
AI Technical Summary
Problems solved by technology
Method used
Image
Examples
Embodiment 1
[0035] The preparation method of the high-performance rotomolded urea tank is as follows:
[0036] The masterbatch and linear low density polyethylene are mixed in a mixer at a ratio of 1:10, and then they are ground into powder by a grinder and then rotomolded.
[0037] The concrete preparation method of masterbatch is as follows:
[0038] (1) Put 120 parts by weight of linear low-density polyethylene resin, 2 parts by weight of functional additives and 1 part by weight of filler into the internal mixer of the torque rheometer and blend for 0.5 h, the blending temperature is 150 ° C, and then sequentially Add 0.5 parts by weight of antioxidant, 0.5 parts by weight of flame retardant and 0.2 parts by weight of lubricant, blend for 1 hour and discharge;
[0039] (2) Extrude in a twin-screw extruder and pelletize to obtain a master batch. The extrusion process conditions are: screw temperature 90°C in the first zone, 130°C in the second zone, 150°C in the third zone, 150°C in t...
Embodiment 2
[0051] A kind of preparation method of high-performance rotomoulding type urea tank is as follows:
[0052] The masterbatch and linear low density polyethylene are mixed in a mixer at a ratio of 1:3, and then ground into a powder of 30-40 mesh by a grinder, and then rotomolded.
[0053] The concrete preparation method of masterbatch is as follows:
[0054] (1) Put 100 parts by weight of linear low density polyethylene resin, 10 parts by weight of functional additives and 3 parts by weight of filler into the internal mixer of the torque rheometer and blend for 1 hour at a blending temperature of 150°C, and then add 2 parts by weight of antioxidant, 2 parts by weight of flame retardant and 1 part by weight of lubricant are blended for 2 hours and discharged;
[0055] (2) Extrude in a twin-screw extruder and pelletize to obtain a master batch. The extrusion process conditions are: screw temperature 100°C in zone 1, 130°C in zone 2, 155°C in zone 3, 155°C in zone 4, and zone 5 1...
Embodiment 3
[0067] A kind of preparation method of high-performance rotomoulding type urea tank is as follows:
[0068] The masterbatch and linear low density polyethylene are mixed in a mixer at a ratio of 1:3, and then they are ground into powder by a grinder and then rotomolded.
[0069] The concrete preparation method of masterbatch is as follows:
[0070] (1) Put 100 parts by weight of linear low-density polyethylene resin, 15 parts by weight of functional additives and 3 parts by weight of filler into the internal mixer of the torque rheometer and blend for 2 hours at a blending temperature of 130°C, and then add 5 parts by weight of antioxidant, 2 parts by weight of flame retardant and 1 part by weight of lubricant are blended for 2 hours and discharged;
[0071] (2) Extrude in a twin-screw extruder and pelletize to obtain a master batch. The extrusion process conditions are: screw temperature 110°C in zone 1, 145°C in zone 2, 160°C in zone 3, 160°C in zone 4, and zone 5 170°C. ...
PUM
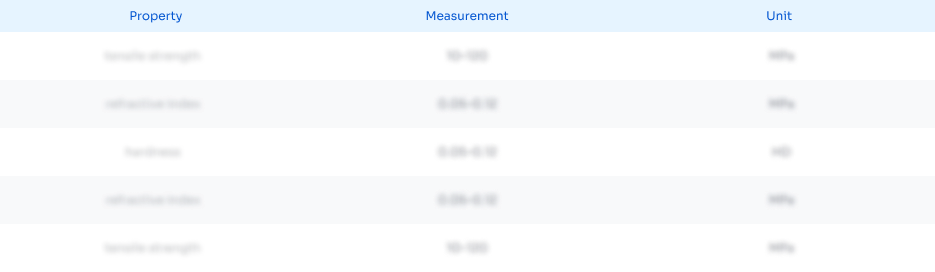
Abstract
Description
Claims
Application Information

- Generate Ideas
- Intellectual Property
- Life Sciences
- Materials
- Tech Scout
- Unparalleled Data Quality
- Higher Quality Content
- 60% Fewer Hallucinations
Browse by: Latest US Patents, China's latest patents, Technical Efficacy Thesaurus, Application Domain, Technology Topic, Popular Technical Reports.
© 2025 PatSnap. All rights reserved.Legal|Privacy policy|Modern Slavery Act Transparency Statement|Sitemap|About US| Contact US: help@patsnap.com