Process for preparing folding-resistant high barrier composite film in sputtering mode
A composite film and preparation process technology, applied in sputtering plating, metal material coating process, ion implantation plating and other directions, can solve the problems of sputtering process interference, film prone to cracks, inflexibility and other problems, to reduce Permeability and cost, overall material performance improvement, easy-to-achieve effects
- Summary
- Abstract
- Description
- Claims
- Application Information
AI Technical Summary
Problems solved by technology
Method used
Image
Examples
Embodiment 1
[0036] A preparation process for preparing a folding-resistant high-barrier composite packaging film by sputtering vacuum plasma deposition technology of polymer, inorganic material or inorganic oxide composite target material, the specific steps are as follows:
[0037] (1) Preparations for cleaning and drying the base material; using PET as the base material, ultrasonically clean it with acetone, alcohol, and deionized water for 20 minutes, and then send it to the blower unit for drying.
[0038] (2) Send the prepared substrate into the pre-sputtering vacuum box for pre-sputtering cleaning, the pre-sputtering gas is 999.99% argon, the sputtering power increase rate is 1.5W hours / square centimeter, and the sputtering time is 120 seconds;
[0039] (3) With PI / SiO 2 The composite material is the target (wherein SiO 2 The mass content is 50%), turn on the radio frequency power supply, carry out co-deposition on the pre-sputtering substrate to prepare C-Si composite high resist...
Embodiment 2
[0041] (1) Preparations for cleaning and drying the base material; using PET as the base material, use acetone, alcohol, and deionized water to ultrasonically clean it for 30 minutes, and then send it to the blower unit for drying.
[0042] (2) Send the prepared substrate into the pre-sputtering vacuum box for pre-sputtering cleaning, the pre-sputtering gas is 999.99% argon, the sputtering power is 1.2Wh / cm2, and the sputtering time is 150 seconds;
[0043] (3) PTFE / SiO2 2 Composite material (SiO 2 Content is 60wt%) as the target material, turn on the radio frequency power supply, carry out co-deposition on the pre-sputtering substrate to prepare F-Si composite high resistance film, the vacuum degree of the vacuum chamber is controlled at 2 × 10 -5 Pa, the working gas is 999.99% argon, the flow rate of argon gas is 90sccm, the working air pressure is 0.4Pa, the target base distance is 8cm, the drum rotation speed is 2m / min, and the sputtering power of the composite target is ...
Embodiment 3
[0045] (1) Preparations for cleaning and drying of the substrate; PP is used as the substrate, ultrasonically cleaned with acetone, alcohol, and deionized water for 15 minutes, and then sent to the blower unit for drying.
[0046] (2) Send the prepared substrate into the pre-sputtering vacuum box for pre-sputtering cleaning, the pre-sputtering gas is 999.99% argon, the sputtering power increase rate is 1.4W hours / square centimeter, and the sputtering time is 120 seconds;
[0047] (3) Using PTFE / ZnO (ZnO content is 40wt%) as the target material, turn on the radio frequency power supply, and prepare C-Al composite high resistance film by co-deposition on the pre-sputtered substrate, and the vacuum degree of the vacuum chamber is controlled at 4× 10-5Pa, the working gas is 999.99% argon, the flow rate of argon gas is 75sccm, the working pressure is controlled at 0.3Pa, the distance between the target and the base is 10cm, the rotation speed of the drum is controlled at 2.5m / min, ...
PUM
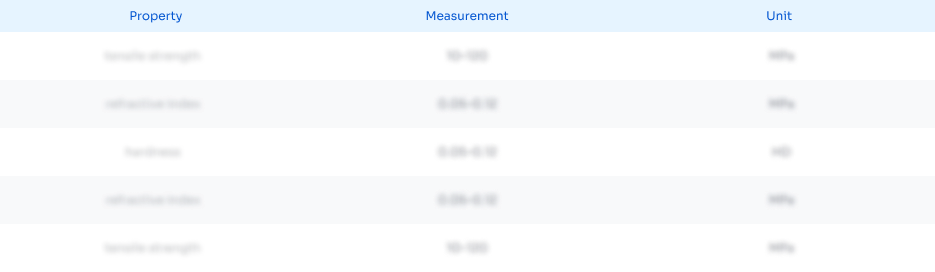
Abstract
Description
Claims
Application Information

- R&D
- Intellectual Property
- Life Sciences
- Materials
- Tech Scout
- Unparalleled Data Quality
- Higher Quality Content
- 60% Fewer Hallucinations
Browse by: Latest US Patents, China's latest patents, Technical Efficacy Thesaurus, Application Domain, Technology Topic, Popular Technical Reports.
© 2025 PatSnap. All rights reserved.Legal|Privacy policy|Modern Slavery Act Transparency Statement|Sitemap|About US| Contact US: help@patsnap.com