Intra-molecular cross-linking polymer, preparation method thereof and application thereof
A technology of cross-linked polymers and polymers, applied in the direction of coating, etc., can solve the problems of a large number of raw materials, difficult to control the cross-linking polymerization reaction process, and complicated preparation methods of chemically synthesized intramolecular cross-linked polymers. The effect of viscosity, strong gamma ray penetration, and simple post-processing
- Summary
- Abstract
- Description
- Claims
- Application Information
AI Technical Summary
Problems solved by technology
Method used
Image
Examples
Embodiment 1
[0041] Accurately weigh 20g of the pretreated PVDF powder, dissolve in 150g of NMP solvent, stir for 24 hours to obtain a homogeneous solution, pass N 2 After more than 25min, place the homogeneous solution in 60 Under the CO source, the radiation reaction was carried out at 25°C, the dose rate was 3.56kGy / h, and the absorbed dose was 64kGy.
[0042] After the irradiation reaction is completed, the obtained homogeneous solution is post-treated according to the following steps: reverse-phase precipitate the homogeneous solution in deionized water, wash the obtained white solid several times, soak it in deionized water for 24 hours, and deionize The water was poured off, and the obtained solid was vacuum-dried in a vacuum oven (50° C., vacuum degree 0.07 MPa) to constant weight to obtain a sample.
Embodiment 2
[0044] Accurately weigh 20g of the pretreated PVDF powder, dissolve in 150g of DMAC solvent, stir for 24 hours to obtain a homogeneous solution, pass N 2 After more than 25min, place the homogeneous solution in 60 Under the CO source, the radiation reaction was carried out at 25°C, the dose rate was 3.56kGy / h, and the absorbed dose was 64kGy.
[0045] After the irradiation reaction is completed, the obtained homogeneous solution is post-treated according to the following steps: reverse-phase precipitate the homogeneous solution in deionized water, wash the obtained white solid several times, soak it in deionized water for 24 hours, and deionize The water was poured off, and the obtained solid was vacuum-dried in a vacuum oven (50° C., vacuum degree 0.07 MPa) to constant weight to obtain a sample.
Embodiment 3
[0047] Accurately weigh 20g of the pretreated PVDF powder, dissolve it in 150g of DMSO solvent, stir for 24 hours to obtain a homogeneous solution, pass N 2 After more than 25min, place the homogeneous solution in 60 Under the CO source, the radiation reaction was carried out at 25°C, the dose rate was 3.56kGy / h, and the absorbed dose was 64kGy.
[0048] After the irradiation reaction is completed, the obtained homogeneous solution is post-treated according to the following steps: reverse-phase precipitate the homogeneous solution in deionized water, wash the obtained white solid several times, soak it in deionized water for 24 hours, and deionize The water was poured off, and the obtained solid was vacuum-dried in a vacuum oven (50° C., vacuum degree 0.07 MPa) to constant weight to obtain a sample.
PUM
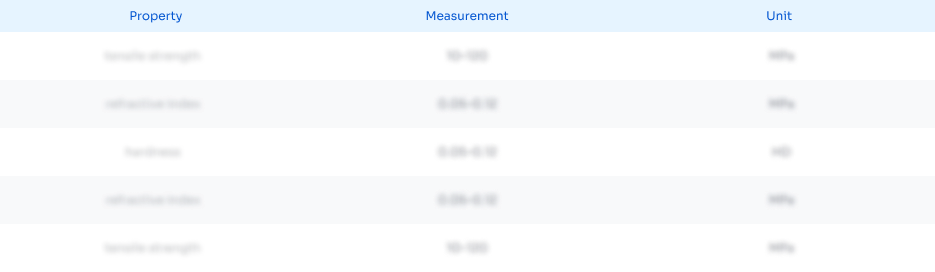
Abstract
Description
Claims
Application Information

- R&D Engineer
- R&D Manager
- IP Professional
- Industry Leading Data Capabilities
- Powerful AI technology
- Patent DNA Extraction
Browse by: Latest US Patents, China's latest patents, Technical Efficacy Thesaurus, Application Domain, Technology Topic, Popular Technical Reports.
© 2024 PatSnap. All rights reserved.Legal|Privacy policy|Modern Slavery Act Transparency Statement|Sitemap|About US| Contact US: help@patsnap.com