Industrial calcination shaft kiln
A calcining and industrial technology, applied in vertical furnaces, waste heat treatment, furnace control devices, etc., can solve the problems of uneven temperature, sintered materials into large blocks, and short operating cycles, and achieve the effect of uniformity
- Summary
- Abstract
- Description
- Claims
- Application Information
AI Technical Summary
Problems solved by technology
Method used
Image
Examples
Embodiment 1
[0043] see figure 1 , 7 The industrial calcination shaft kiln shown includes a straight upper cylinder 5 , a middle cylinder 7 and a lower cylinder 11 . A feeding bin 1, a feeding pipe 2 and a distributor 6 are arranged on the upper part of the upper cylinder body 5 for filling materials into the cylinder body. The outlet end of the feeding pipe is located at the center of the top of the upper cylinder and communicates with the inside of the cylinder, and the distributor is located below the outlet of the feeding pipe. The feeding pipe 2 can be stretched relative to the upper cylinder to change the length (equivalent to the feeding pipe can move up and down relative to the upper cylinder). Distributor 6 is a conical body with a small upper part and a larger lower part. It is suspended on the top of the upper cylinder by suspension cables or suspenders 25. The suspension cables or suspenders can be adjusted to change the upper and lower positions of the distributor relative ...
Embodiment 2
[0051] see figure 2 Shown industrial calcination shaft kiln, its difference with embodiment 1 mainly lies in:
[0052] The upper cylinder 4 in Embodiment 2 is an upper cylinder with a conical bottom with a large upper part and a smaller lower part. This is conducive to a more uniform heat exchange between the air flow and the material. This structure can be used in different said industrial calcination shaft kilns.
[0053] The upper opening of the middle cylinder body 7 in the second embodiment is shaped, and the outer circumference of the upper end thereof protrudes upwards, forming an empty area 24 communicating with the cavity 23 at the upper part of the sudden change section. This is beneficial to increase the volume of the cavity 23 . This structure can be used in different said industrial calcination shaft kilns.
[0054] The distributor 9 and the supporting legs 10 in the second embodiment are hollow structures connected internally, cooling air is passed through t...
Embodiment 3
[0057] see image 3 Shown industrial calcination shaft kiln, its difference with embodiment 1 mainly lies in:
[0058] The upper cylinder body 4 in the embodiment 3 is an upper cylinder body with a conical bottom with a large top and a small bottom. This is conducive to a more uniform heat exchange between the air flow and the material. This structure can be used in different industrial calcination shaft kilns
[0059] The flue gas pipe 3 in Embodiment 3 is provided with a flue gas-air heat exchanger 19, the inlet of the combustion-supporting air supply channel 18 of the fuel combustion device is connected to the air outlet of the heat exchanger 19, and the air inlet of the heat exchanger is connected to the air outlet of the heat exchanger. Blowers 20 are connected. This structure can be used in different said industrial calcination shaft kilns.
[0060] The distributor 9 in Example 3 is a hollow plate-shaped structure, and the installation height of the distributor is lo...
PUM
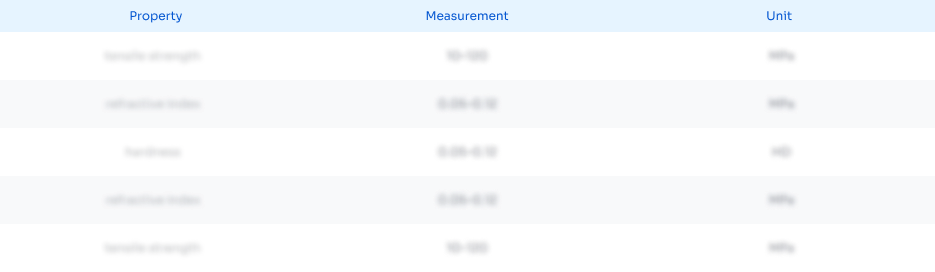
Abstract
Description
Claims
Application Information

- R&D
- Intellectual Property
- Life Sciences
- Materials
- Tech Scout
- Unparalleled Data Quality
- Higher Quality Content
- 60% Fewer Hallucinations
Browse by: Latest US Patents, China's latest patents, Technical Efficacy Thesaurus, Application Domain, Technology Topic, Popular Technical Reports.
© 2025 PatSnap. All rights reserved.Legal|Privacy policy|Modern Slavery Act Transparency Statement|Sitemap|About US| Contact US: help@patsnap.com