MAX phase reinforced zirconium titanium aluminum vanadium alloy and preparation method thereof
A zirconium-titanium-aluminum-vanadium alloy and zirconium-titanium-aluminum technology, which is applied in the field of alloy materials and their preparation, can solve the problems of difficult forging temperature control, increased manufacturing cycle and cost of zirconium-titanium-based alloys, etc., and achieves low cost and improved mechanical properties of the alloy. , the effect of refining the organization
- Summary
- Abstract
- Description
- Claims
- Application Information
AI Technical Summary
Problems solved by technology
Method used
Image
Examples
Embodiment 1
[0020] Embodiment 1 (comparative example)
[0021] Cut 63.5g of forged 20Zr (Ti-20Zr-6Al-4V), put it in absolute ethanol, clean it with ultrasonic vibration, dry it with a hair dryer, and place it in a non-consumable vacuum arc melting furnace for repeated melting 8 times, the vacuum degree is 2.0×10 -2 Pa, the smelting current is kept at 300A, and the smelting time of each sample is 2min. After each smelting is completed, wait for the high-temperature red color of the ingot to recede before the next smelting. An alloy ingot with uniform composition is obtained.
[0022] A compression rod with a height of 10 mm and a diameter of 5 mm was cut from the ingot on a wire cutting machine, and the scale was removed from the surface with sandpaper, and its compression mechanical properties were tested on an instron5982 mechanical property testing machine. The specific experimental data are shown in Table 1.
[0023] Then put the zirconium-titanium-aluminum-vanadium alloy ingot into ...
Embodiment 2
[0025] Cut 63.9g of forged 20Zr (Ti-20Zr-6Al-4V) and SPS (plasma discharge sintering) to obtain pure Ti 3 AlC 2 Phase 0.33g, crushed, respectively placed in absolute ethanol, cleaned with ultrasonic vibration, dried with a hair dryer, placed in a non-consumable vacuum arc melting furnace for repeated melting 8 times, the vacuum degree was 2.0×10 -2 Pa, the smelting current is kept at 300A, and the sample smelting time is 2 minutes. After each smelting is completed, wait for the high-temperature red heat color of the ingot to fade before the next smelting. An alloy ingot with uniform composition is obtained.
[0026] A compression rod with a height of 10 mm and a diameter of 5 mm was cut from the ingot on a wire cutting machine, and the scale was removed from the surface with sandpaper, and its compression mechanical properties were tested on an instron5982 mechanical property testing machine. The specific experimental data are shown in Table 1.
[0027] Then put the zirconiu...
Embodiment 3
[0029] Cut 63.2g of forged 20Zr (Ti-20Zr-6Al-4V) and SPS (plasma discharge sintering) to obtain pure Ti 3 AlC 2 Phase 0.64g, crushed, respectively placed in absolute ethanol, cleaned with ultrasonic vibration, dried with a hair dryer, placed in a non-consumable vacuum arc melting furnace for repeated melting 8 times, the vacuum degree was 2.0×10 -2 Pa, the smelting current is kept at 300A, and the sample smelting time is 2 minutes. After each smelting is completed, wait for the high-temperature red heat color of the ingot to fade before the next smelting. An alloy ingot with uniform composition is obtained.
[0030] A compression rod with a height of 10 mm and a diameter of 5 mm was cut from the ingot on a wire cutting machine, and the scale was removed from the surface with sandpaper, and its compression mechanical properties were tested on an instron5982 mechanical property testing machine. The specific experimental data are shown in Table 1.
[0031] Then put the zirconiu...
PUM
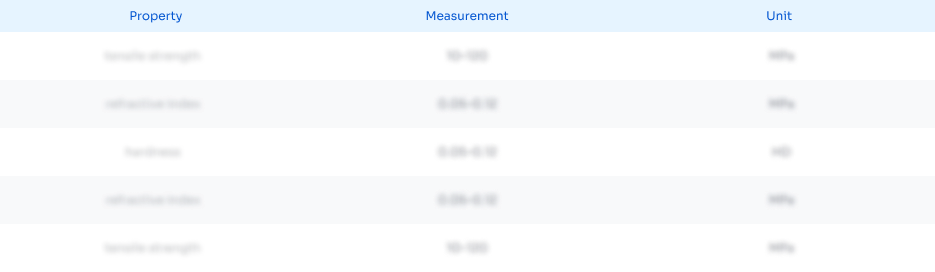
Abstract
Description
Claims
Application Information

- R&D
- Intellectual Property
- Life Sciences
- Materials
- Tech Scout
- Unparalleled Data Quality
- Higher Quality Content
- 60% Fewer Hallucinations
Browse by: Latest US Patents, China's latest patents, Technical Efficacy Thesaurus, Application Domain, Technology Topic, Popular Technical Reports.
© 2025 PatSnap. All rights reserved.Legal|Privacy policy|Modern Slavery Act Transparency Statement|Sitemap|About US| Contact US: help@patsnap.com