Casting process and casting system
A casting process and sand bag technology, used in manufacturing tools, casting equipment, molds, etc., can solve the problems of non-dense mechanical properties of castings, shrinkage cavities and loose grains, long solidification time, etc., and increase the eutectic structure. , the effect of fine tissue, pinhole level reduction or elimination
- Summary
- Abstract
- Description
- Claims
- Application Information
AI Technical Summary
Problems solved by technology
Method used
Image
Examples
Embodiment 1
[0030] The casting process that the embodiment of the present invention provides comprises:
[0031] Assembly: assemble the sand core into sand bag 001;
[0032] Filling: Move the assembled sand bag 001 to the pouring device for filling;
[0033] Solidification: Move the filled sand bag 001 to a high-pressure environment for solidification.
[0034] Taking cast aluminum alloy castings as an example, the specific steps of the casting process provided by the embodiment of the present invention are described below:
[0035] The cast aluminum alloy is melted in the molten metal holding furnace 400, and after refining, degassing and modification, the temperature of the molten aluminum is controlled at 640°C-760°C before filling.
[0036] Assemble the sand core into a sand bag 001, clamp the assembled sand bag 001 by the manipulator, and move it to the top of the riser pipe 500 of the pouring device, make the gate of the sand bag 001 dock with the riser pipe 500, and wait for the ...
Embodiment 2
[0053] The casting system provided by the embodiment of the present invention is used to realize the above-mentioned casting process. The casting system includes a pouring device and a pressure holding device, and the pouring device and the pressure holding device are arranged independently of each other.
[0054] The pouring device is used to fill the sand bag 001 with molten metal, and the filled sand bag 001 is moved to the pressure holding device by the manipulator, and the pressure holding device makes the metal liquid in the sand bag 001 solidify under the required pressure environment. In the pouring system provided by the embodiment of the present invention, the pressure holding device and the pouring device are set independently of each other, not only can complete pouring and pressure holding and solidification, but the pressure holding device can also be applied to hold the sand bag 001 that has been poured by other pouring devices , suitable for different sand bags ...
PUM
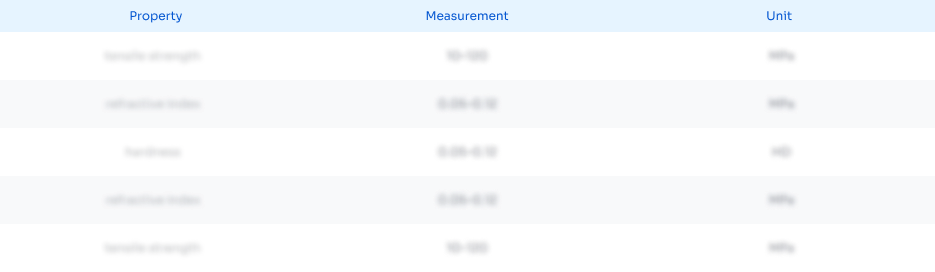
Abstract
Description
Claims
Application Information

- R&D
- Intellectual Property
- Life Sciences
- Materials
- Tech Scout
- Unparalleled Data Quality
- Higher Quality Content
- 60% Fewer Hallucinations
Browse by: Latest US Patents, China's latest patents, Technical Efficacy Thesaurus, Application Domain, Technology Topic, Popular Technical Reports.
© 2025 PatSnap. All rights reserved.Legal|Privacy policy|Modern Slavery Act Transparency Statement|Sitemap|About US| Contact US: help@patsnap.com