Thermal insulation elastomer modified asphalt coating as well as preparation method and waterproof coil thereof
A thermal insulation and body modification technology, which is applied in asphalt coatings, building insulation materials, coatings, etc., can solve the problems that the surface is not easy to bond, the application effect cannot be achieved, and the complementarity is poor, so as to avoid degradation and improve The effect of anti-ultraviolet aging ability
- Summary
- Abstract
- Description
- Claims
- Application Information
AI Technical Summary
Problems solved by technology
Method used
Image
Examples
Embodiment 1
[0051] 55 parts (parts by mass, the same below) of natural lake asphalt and 7 parts of base oil were respectively added to the reactor and heated to 175 ° C, and the shear mixer was started. At a speed of 800 rpm, 2 parts of graphene airgel were slowly added to keep The temperature is 170-180°C, and the stirring is continued for 1.5 hours. The obtained material is dispersed through a colloid mill and then transferred to a reaction kettle. Reduce to 500rpm, and stir for 1 hour, then raise the temperature to 190°C, add 6 parts of styrene-butadiene-styrene thermoplastic elastomer (SBS), keep the temperature at 180-190°C, and stir at 500rpm for reaction After 2.5 hours, reduce the stirring speed to 300rpm, add 27 parts of talcum powder, keep the temperature at 180-190°C, and continue stirring for 1 hour to obtain the thermal insulation elastomer modified asphalt coating material.
[0052] A thermal insulation elastomer modified asphalt waterproof coiled material, comprising the ab...
Embodiment 2
[0054]55 parts (parts by mass, the same below) of natural lake asphalt and 7 parts of base oil were added to the reactor and heated to 175 ° C, and the shear mixer was started. At a speed of 500 rpm, 3 parts of graphene airgel were slowly added to keep The temperature is 170-180°C, and the stirring is continued for 1 hour. The obtained material is dispersed through a colloid mill and then transferred to a reaction kettle. Reduce to 300rpm, and stir for 0.5 hours, then raise the temperature to 190°C, add 6 parts of styrene-butadiene-styrene thermoplastic elastomer (SBS), keep the temperature at 180-190°C, and stir at 300rpm for reaction After 2 hours, reduce the stirring speed to 200rpm, add 24 parts of talcum powder, keep the temperature at 180-190°C, and continue stirring for 0.5 hours to obtain a thermal insulation elastomer modified asphalt coating material.
[0055] A thermal insulation elastomer modified asphalt waterproof coiled material, comprising the above thermal ins...
Embodiment 3
[0057] 65 parts (parts by mass, the same below) of natural lake asphalt and 10 parts of base oil were added to the reactor and heated to 175 ° C, and the shear mixer was started. At a speed of 800 rpm, 1 part of graphene airgel was slowly added to keep The temperature is 170-180°C, and the stirring is continued for 1.5 hours. The obtained material is dispersed through a colloid mill and then transferred to a reaction kettle. Then, the temperature is raised to 185°C, and 5 parts of polypropylene are added. Reduce to 500rpm, and stir for 1 hour, then raise the temperature to 190°C, add 8 parts of styrene-butadiene-styrene thermoplastic elastomer (SBS), keep the temperature at 180-190°C, and stir at 500rpm for reaction After 3 hours, reduce the stirring speed to 300rpm, add 11 parts of talcum powder, keep the temperature at 180-190°C, and continue stirring for 0.5 hours to obtain the thermal insulation elastomer modified asphalt coating material.
[0058] A thermal insulation ela...
PUM
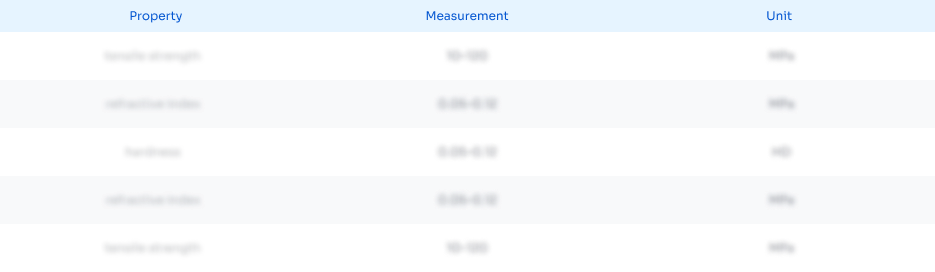
Abstract
Description
Claims
Application Information

- Generate Ideas
- Intellectual Property
- Life Sciences
- Materials
- Tech Scout
- Unparalleled Data Quality
- Higher Quality Content
- 60% Fewer Hallucinations
Browse by: Latest US Patents, China's latest patents, Technical Efficacy Thesaurus, Application Domain, Technology Topic, Popular Technical Reports.
© 2025 PatSnap. All rights reserved.Legal|Privacy policy|Modern Slavery Act Transparency Statement|Sitemap|About US| Contact US: help@patsnap.com