Multifunctional composite material and preparation method thereof
A functional composite material and a composite material technology, which are applied in the field of thermally conductive and/or conductive functional composite materials and their preparation, can solve the problems of reducing the modification effect of functional fillers, and no regulation of the distribution state of fillers, so as to reduce the content and save costs. Effect
- Summary
- Abstract
- Description
- Claims
- Application Information
AI Technical Summary
Problems solved by technology
Method used
Image
Examples
Embodiment 1
[0044] 50 parts of polypropylene and 50 parts of carbon fiber (surface-treated with silane coupling agent γ-methacryloxypropyltrimethoxysilane accounting for 2wt% of carbon fiber mass) were mixed uniformly in a high-speed mixer, and then added to the twin-screw Plasticize and mix in the extruder, and then prepare a thermally and electrically conductive composite parison of a certain thickness through an extrusion casting head. The twin-screw extrusion temperature is 180°C-220°C, and the screw speed is 200rpm. Biaxially stretch the parison at 170°C with a stretching rate of 5mm / min, then cool and shape it, the orientation state structure is as attached figure 2 Its performance is shown in Table 1.
Embodiment 2
[0046] 50 parts of polylactic acid, 10 parts of acetyl tributyl citrate and 40 parts of graphite nanosheets (surface-treated with silane coupling agent γ-aminopropyltriethoxysilane accounting for 8wt% of the mass of graphite nanosheets) were mixed at high speed Mix evenly in the machine, then add it to the twin-screw extruder for plasticization and mixing, and then prepare a thermally conductive composite material parison with a certain thickness through the extrusion casting head. The twin-screw extrusion temperature is 170-195°C, and the screw speed is 300rpm. The parison was uniaxially stretched at 160°C with a stretching rate of 10mm / min, and then cooled and shaped. The orientation state structure is shown in the attached image 3 Its performance is shown in Table 1.
Embodiment 3
[0048] 50 parts of polyethylene terephthalate, 45 parts of nickel-plated carbon nanotubes (accounting for the silane coupling agent γ-(2,3-epoxypropoxy)propane of 5.5wt% of the mass of nickel-plated carbon nanotubes base trimethoxysilane surface treatment), 10 parts of boron nitride fiber (surface treated with silane coupling agent γ-(2,3-epoxypropoxy)propyltrimethoxysilane accounting for 2wt% of the mass of boron nitride fiber ) mixed evenly in a high-speed mixer, then added to a twin-screw extruder for plasticization and mixing, and then prepared a certain thickness of heat-conducting and electrically-conductive composite material parison through extrusion casting head, the twin-screw extrusion temperature is 250 ~ 270 ° C , the screw speed is 240rpm. The parison was biaxially stretched at 250°C with a stretching rate of 10mm / min, and then cooled and shaped. The properties are shown in Table 1.
PUM
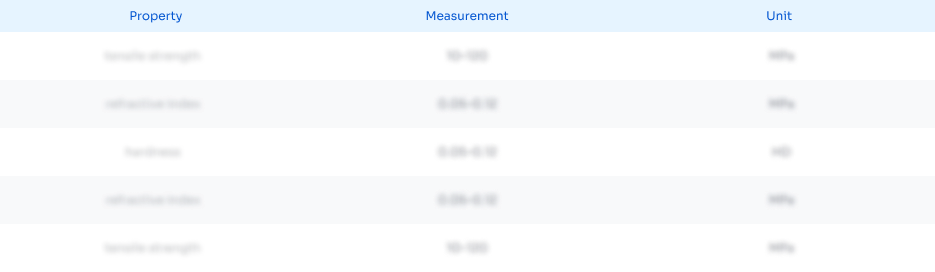
Abstract
Description
Claims
Application Information

- R&D Engineer
- R&D Manager
- IP Professional
- Industry Leading Data Capabilities
- Powerful AI technology
- Patent DNA Extraction
Browse by: Latest US Patents, China's latest patents, Technical Efficacy Thesaurus, Application Domain, Technology Topic, Popular Technical Reports.
© 2024 PatSnap. All rights reserved.Legal|Privacy policy|Modern Slavery Act Transparency Statement|Sitemap|About US| Contact US: help@patsnap.com