Titanium fire preventing flame-retardant coating and preparation method thereof
A technology of flame-retardant coating and titanium fire, which is applied in the field of titanium alloy application, can solve the problems that flame-retardant titanium alloy cannot meet the design requirements, the difficulty of manufacturing large-scale parts, and the difficulty of forming, so as to improve the interface bonding characteristics and the preparation cycle. Short, the effect of increasing the service temperature
- Summary
- Abstract
- Description
- Claims
- Application Information
AI Technical Summary
Problems solved by technology
Method used
Examples
Embodiment 1
[0029] Ti-5.8Al-4Sn-4Zr-0.7Nb-1.5Ta-0.4Si-0.06C titanium alloy substrate was coated with titanium-aluminum intermetallic compound coating by laser cladding method, and its nominal chemical composition was Ti-46Al-2Cr -5Nb-0.2Ta, the maximum power of the laser cladding equipment used is 6KW.
[0030] The spherical titanium-aluminum intermetallic compound powder with an average particle size of 53 μm was prepared by argon atomization method, and after drying, it was subjected to laser cladding. The laser power was 0.6KW, the cladding rate was 450mm / min, and the powder feeding rate was 1.8rpm, the prepared coating thickness is 0.8mm.
[0031] Then, the prepared titanium-aluminum intermetallic compound coating was subjected to stress relief annealing, wire cutting, grinding and drilling to obtain a flame retardant test sample with a size of 126mm×27mm×2.1mm (with a Φ4mm circle in the center hole). The flame retardant performance test was carried out with the friction ignition eq...
Embodiment 2
[0033] Ti-15Mo-3Al-2.7Nb-0.2Si titanium alloy substrate was coated with Ti-Al intermetallic compound coating by laser cladding method, and its nominal chemical composition was Ti-45Al-1.5Cr-2Nb-1.5Ta-0.1B . The maximum power of the laser cladding equipment used is 6KW.
[0034] The spherical titanium-aluminum intermetallic compound powder with an average particle size of 75 μm was prepared by argon atomization method. After drying, laser cladding was carried out on it. The laser power was 0.9KW, the cladding rate was 350mm / min, and the powder feeding rate was 1.5rpm, the prepared coating thickness is 1.0mm.
[0035]Then, the prepared titanium-aluminum intermetallic compound coating was subjected to stress relief annealing, wire cutting, grinding and drilling to obtain a flame retardant test sample with a size of 126mm×27mm×2.1mm (with a Φ4mm circle in the center hole). The flame retardant performance test was carried out using the friction ignition equipment of China Aerosp...
Embodiment 3
[0037] Ti-6.5Al-3.5Mo-15Zr-0.3Si titanium alloy substrate was coated with titanium-aluminum intermetallic compound coating by laser cladding method, and its nominal chemical composition was Ti-46Al-2Cr-3.5Nb-0.8Ta-0.2 For B-0.05C, the maximum power of the laser cladding equipment used is 6KW.
[0038] Spherical titanium-aluminum intermetallic compound powder with an average particle size of 116 μm was prepared by argon atomization method. After drying, laser cladding was carried out on it. The laser power was 1.2KW, the cladding rate was 400mm / min, and the powder feeding rate was 1.5rpm, the prepared coating thickness is 1.0mm.
[0039] Then, the prepared titanium-aluminum intermetallic compound coating was subjected to stress relief annealing, wire cutting, grinding and drilling to obtain a flame retardant test sample with a size of 126mm×27mm×2.1mm (with a Φ4mm circle in the center hole). The flame retardant performance test was carried out using the friction ignition equi...
PUM
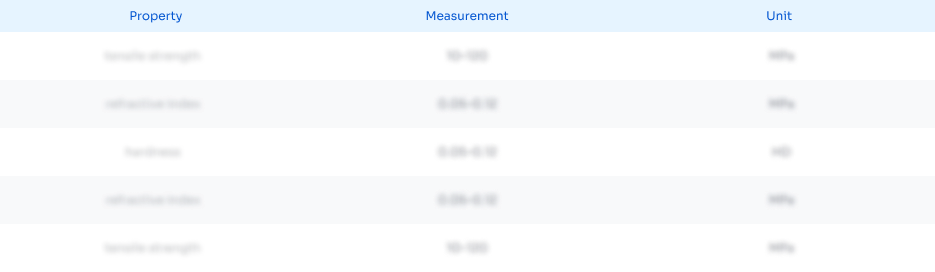
Abstract
Description
Claims
Application Information

- R&D
- Intellectual Property
- Life Sciences
- Materials
- Tech Scout
- Unparalleled Data Quality
- Higher Quality Content
- 60% Fewer Hallucinations
Browse by: Latest US Patents, China's latest patents, Technical Efficacy Thesaurus, Application Domain, Technology Topic, Popular Technical Reports.
© 2025 PatSnap. All rights reserved.Legal|Privacy policy|Modern Slavery Act Transparency Statement|Sitemap|About US| Contact US: help@patsnap.com