ABS (acrylonitrile butadiene styrene) halogen-free flame-retardant composite material and preparation method thereof
A flame retardant composite material and composite flame retardant technology are applied in the field of ABS halogen-free flame retardant composite material and its preparation, which can solve the problems of deterioration of ABS mechanical properties and processing performance, and high flame retardant addition amount, and improve mechanical properties. and machinability, improving flame retardant properties, and improving application performance
- Summary
- Abstract
- Description
- Claims
- Application Information
AI Technical Summary
Problems solved by technology
Method used
Examples
preparation example Construction
[0037] A preparation method of BS halogen-free flame-retardant composite material, the preparation steps are:
[0038] (1) Weigh the raw materials according to the ratio of parts by mass;
[0039] (2) Add acrylonitrile-butadiene-styrene copolymer into the internal mixer to preheat for 5 minutes, then add compound flame retardant, synergistic flame retardant, organic clay, antioxidant, lubricant and compatibilizer agent, melt blending for 10-15min at 180-185°C, 50-60r / min;
[0040] (3) Preheat the molten blend with a flat vulcanizing agent for 3-5 minutes, then hot press at 180-185°C and 14-15MPa for 6-7 minutes, and then cold press at 14-15MPa for 3-5 minutes to form.
Embodiment 1
[0042] A preparation method of BS halogen-free flame-retardant composite material, the preparation steps are:
[0043] (1) Raw materials are weighed according to the ratio of parts by mass: acrylonitrile-butadiene-benzene synthesized by suspension graft copolymerization method, with a relative density of 1.0-1.1g / cm3 and a butadiene content of 17-70%. 80 parts of ethylene copolymer, 55 parts of composite flame retardant (including 22 parts of high-polymerization ammonium phosphate, 610 parts of polyamide, 623 parts of modified polyamide), 5 parts of 4A molecular sieve, 1 part of organic loess, 2, 0.5 parts of 2-methylene bis(4-methyl-6-tert-butylphenol), 3 parts of ethylene bis stearamide, grafted material of ABS and maleic anhydride with a grafting rate of 0.5-3% 7 copies;
[0044] (2) Add acrylonitrile-butadiene-styrene copolymer to the internal mixer to preheat for 5 minutes, then add compound flame retardant, 4A molecular sieve, organic loess, 2,2-methylenebis(4-formazol ...
Embodiment 2
[0047] A preparation method of BS halogen-free flame-retardant composite material, the preparation steps are:
[0048](1) Raw materials are weighed according to the ratio of parts by mass: acrylonitrile-butadiene-benzene synthesized by suspension graft copolymerization method, with a relative density of 1.0-1.1g / cm3 and a butadiene content of 17-70%. 90 parts of ethylene copolymer, 50 parts of composite flame retardant (including 20 parts of high-polymerization ammonium phosphate, 615 parts of polyamide, 615 parts of modified polyamide), 9 parts of 4A molecular sieve, 3 parts of organic red clay, antioxidant 10100.3 parts, 2 parts of monoglyceride stearate, 5 parts of grafts of ABS and maleic anhydride with a graft rate of 0.5-3%;
[0049] (2) Add acrylonitrile-butadiene-styrene copolymer to the internal mixer to preheat for 5 minutes, then add compound flame retardant, 4A molecular sieve, organic red clay, antioxidant 1010, monoglyceride stearate and The grafted material of ...
PUM
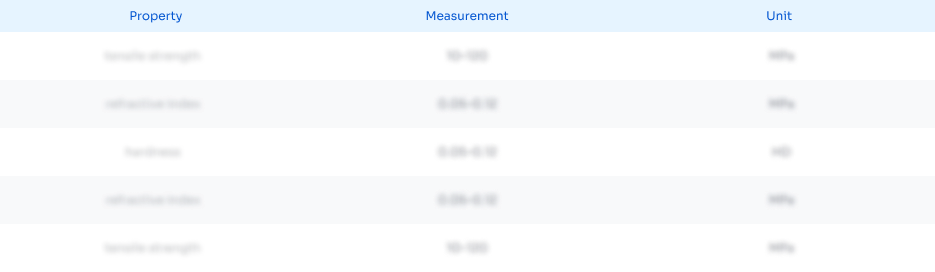
Abstract
Description
Claims
Application Information

- R&D
- Intellectual Property
- Life Sciences
- Materials
- Tech Scout
- Unparalleled Data Quality
- Higher Quality Content
- 60% Fewer Hallucinations
Browse by: Latest US Patents, China's latest patents, Technical Efficacy Thesaurus, Application Domain, Technology Topic, Popular Technical Reports.
© 2025 PatSnap. All rights reserved.Legal|Privacy policy|Modern Slavery Act Transparency Statement|Sitemap|About US| Contact US: help@patsnap.com