A barite thermal reduction-water immersion barium slag detoxification process
A barite and barium slag technology, which is applied in the field of barite thermal reduction-water immersion barium slag detoxification process, can solve the problems of high cost, inconvenient operation, and environmental pollution, and achieve the effect of reducing purification cost and easy operation
- Summary
- Abstract
- Description
- Claims
- Application Information
AI Technical Summary
Problems solved by technology
Method used
Examples
Embodiment 1
[0041] Take 1.5L of 5% sulfurous acid solution, add it to the barium residue containing 0.2% BaS at a solid-to-liquid ratio of 1:5g / ml, stir at room temperature for 1.5h, and filter to obtain the filtrate and filter residue. Add 0.5mol / L Na to the filter residue 2 SO 4 Soak the solution for 15 minutes to oxidize the barium sulfite into barium sulfate, take a sample for analysis, and the Ba in the solution after soaking 2+ The ion concentration is 0.53mg / L, the soluble Ba in the filter residue is less than 1ppm, and the barium residue is converted from hazardous solid waste to general solid waste. The resulting filtrate was passed through SO 2 , so that the concentration of sulfurous acid therein reaches 5.5% for later use.
Embodiment 2
[0043] Take 500 g of barium slag containing 0.15% BaS and grind it to -40 mesh, add the solution with a sulfurous acid concentration of 5.5% obtained in Example 1 at a solid-to-liquid ratio of 1:4 g / ml, stir at room temperature for 0.5 h, and then blow in air to continue Stir for 3h, filter, sample analysis, Ba in the filtrate 2+ The ion concentration is 0.15mg / L, the soluble Ba in the filter residue is less than 1ppm, and the obtained filtrate is passed through SO 2 make it regenerate.
Embodiment 3
[0045] The tail gas produced by the by-product sulfur in the barium carbonate production process is first sprayed and absorbed with water to obtain a solution containing sulfurous acid, and then lime water and lye are used to absorb the residual SO in the tail gas 2 emission. The resulting sulfurous acid-containing solution is partly drawn from the spray circulation system and used as a detoxification solution for the barium slag formed in the production process of barium carbonate. 2 , so that it can be regenerated and recycled. Take 4.5t of barium slag and put it in the leaching tank, draw out the detoxification solution from the spray circulation system, and use 25m 3 The rate of / h is circulated between the leaching tank and the spray system, and the barium dross is soaked in a cycle for 2 hours, drained, and stacked in the air for 1 week. Sampling analysis shows that the soluble Ba in the detoxified barium dregs is <1ppm.
PUM
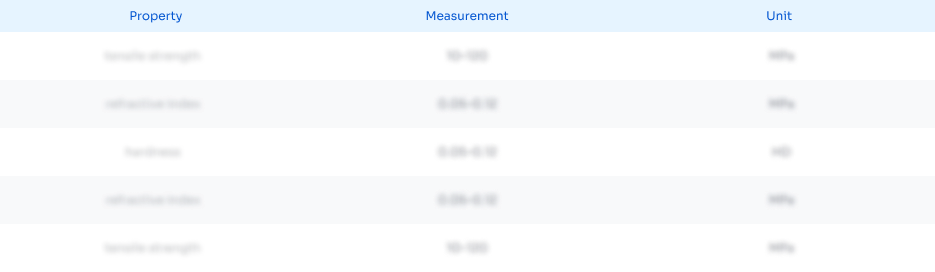
Abstract
Description
Claims
Application Information

- Generate Ideas
- Intellectual Property
- Life Sciences
- Materials
- Tech Scout
- Unparalleled Data Quality
- Higher Quality Content
- 60% Fewer Hallucinations
Browse by: Latest US Patents, China's latest patents, Technical Efficacy Thesaurus, Application Domain, Technology Topic, Popular Technical Reports.
© 2025 PatSnap. All rights reserved.Legal|Privacy policy|Modern Slavery Act Transparency Statement|Sitemap|About US| Contact US: help@patsnap.com