A kind of bearing and its preparation process
A preparation process and bearing technology, which is applied in the field of bearings and its preparation process, can solve performance problems such as lack of strength, hardness, numerous processes, non-wear resistance, etc., and achieve the effects of reducing product weight, eliminating residual stress, and optimizing mechanical properties
- Summary
- Abstract
- Description
- Claims
- Application Information
AI Technical Summary
Problems solved by technology
Method used
Image
Examples
Embodiment 1
[0033] Ingredients: Weigh raw materials according to the composition and mass percentage of the above alloy steel, including Cd: 0.06%, Mn: 1%, C: 0.6%, Tl: 0.1%, Cu: 0.03%, Co: 0.05%, and the balance is Fe and impurities, wherein impurities include P<0.04%, S<0.04%, N<0.04%, O<0.03%. The raw materials are melted to form alloy liquid and poured into the mold to form bearing semi-finished products.
[0034] Heat treatment: Temper the bearing semi-finished product first, heat it to 550°C, keep it warm for 10 minutes, cool it down to room temperature naturally, and then perform annealing treatment, heat the semi-finished product to 350°C, keep it warm for 5 minutes, cool it with the furnace, and then perform the second isothermal tempering treatment , keep warm for 3 minutes, cool to room temperature with external air, and finally anneal for the second time at a lower temperature, heat to 250°C, keep warm for 3 minutes and then cool naturally to room temperature.
[0035] Blendi...
Embodiment 2
[0038] Ingredients: Weigh raw materials according to the composition and mass percentage of the above alloy steel, including Cd: 0.05%, Mn: 0.5%, C: 0.4%, Tl: 0.08%, Cu: 0.01%, Co: 0.03%, and the balance is Fe and impurities, wherein impurities include P<0.04%, S<0.04%, N<0.04%, O<0.03%. The raw materials are melted to form alloy liquid and poured into the mold to form bearing semi-finished products.
[0039] Heat treatment: Temper the bearing semi-finished product first, heat it to 400°C, keep it warm for 5 minutes, cool it down to room temperature naturally, then perform annealing treatment, heat the semi-finished product to 300°C, keep it warm for 1 minute, cool it with the furnace, and then perform the second isothermal tempering treatment , keep warm for 1min, cool to room temperature with external air, and finally anneal for the second time at a lower temperature, heat to 200°C, keep warm for 1min and then cool naturally to room temperature.
[0040] Blending of external ...
Embodiment 3
[0043] Ingredients: Weigh raw materials according to the composition and mass percentage of the above alloy steel, including Cd: 0.07%, Mn: 1.5%, C: 0.8%, Tl: 0.12%, Cu: 0.05%, Co: 0.07%, and the balance is Fe and impurities, wherein impurities include P<0.04%, S<0.04%, N<0.04%, O<0.03%. The raw materials are melted to form alloy liquid and poured into the mold to form bearing semi-finished products.
[0044] Heat treatment: Temper the bearing semi-finished product first, heat it to 700°C, keep it warm for 15 minutes, cool it down to room temperature naturally, then perform annealing treatment, heat the semi-finished product to 400°C, keep it warm for 10 minutes, cool it with the furnace, and then perform the second isothermal tempering treatment , heat preservation for 5 minutes, external air cooling to room temperature, and finally a second annealing at a lower temperature, heating to 300 ° C, heat preservation for 5 minutes, and then naturally cooling to room temperature. ...
PUM
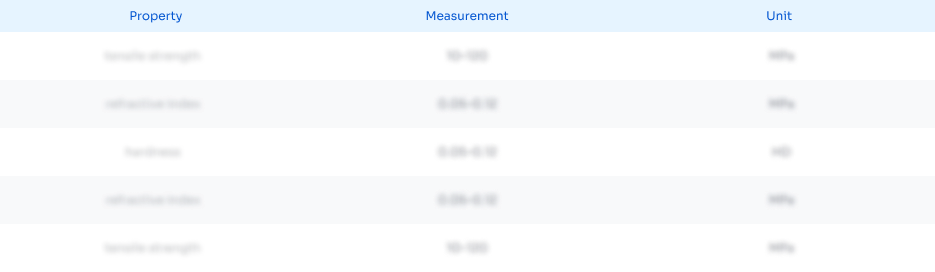
Abstract
Description
Claims
Application Information

- Generate Ideas
- Intellectual Property
- Life Sciences
- Materials
- Tech Scout
- Unparalleled Data Quality
- Higher Quality Content
- 60% Fewer Hallucinations
Browse by: Latest US Patents, China's latest patents, Technical Efficacy Thesaurus, Application Domain, Technology Topic, Popular Technical Reports.
© 2025 PatSnap. All rights reserved.Legal|Privacy policy|Modern Slavery Act Transparency Statement|Sitemap|About US| Contact US: help@patsnap.com