Organic silicon modified cationic light cured alicyclic epoxy resin paint and application thereof
An epoxy resin coating, cycloaliphatic epoxy technology, applied in the direction of coating, liquid coating device on the surface, surface pretreatment, etc., can solve the problems of poor toughness and leveling, and achieve good toughness and good water resistance Stain resistance, strong reactivity effect
- Summary
- Abstract
- Description
- Claims
- Application Information
AI Technical Summary
Problems solved by technology
Method used
Image
Examples
Embodiment 1
[0045] Embodiment 1: the preparation of cycloaliphatic epoxy resin prepolymer
[0046] In parts by weight, 150 parts of 2-butanone is placed in a reactor with a stirrer and a condenser, and 10 parts of 3,4-epoxycyclohexyl-methyl methacrylate, 45 45 parts of methyl methacrylate and 45 parts of butyl acrylate, stirred and heated to 90°C, then added 4.5 parts of azobisisobutyronitrile, kept the reaction at this temperature for 5 hours, and then recovered the solvent by distillation under reduced pressure to obtain cycloaliphatic epoxy Resin prepolymer S1;
[0047] figure 1 In order to obtain the infrared spectrogram of cycloaliphatic epoxy resin prepolymer S1, it can be found from the figure that at 790cm -1 The characteristic absorption of cycloaliphatic epoxy appears at , indicating that 3,4-epoxycyclohexyl-methyl methacrylate is connected to the main chain of acrylate polymer;
Embodiment 2
[0048] Embodiment 2: the preparation of cycloaliphatic epoxy resin prepolymer
[0049] In parts by weight, take 150 parts of 2-butanone and place it in a reactor with a stirrer and a condenser tube, and add 20 parts of 3,4-epoxycyclohexyl-methylmethacrylate, 40 parts of methyl methacrylate and 40 parts of butyl acrylate, after stirring and raising the temperature to 80°C, add 4.5 parts of dibenzoyl oxide, keep the reaction at this temperature for 7 hours, and then recover the solvent by distillation under reduced pressure to obtain alicyclic ring Oxygen resin prepolymer S2;
Embodiment 3
[0050] Embodiment 3: the preparation of cycloaliphatic epoxy resin prepolymer
[0051] Recorded in parts by weight, take 150 parts of ethyl acetate and place it in a reactor with a stirrer and a condenser tube, and add 30 parts of 3,4-epoxycyclohexyl-methyl methacrylate, 70 parts 1 part of n-hexyl methacrylate, after stirring and heating up to 90°C, add 4.5 parts of azobisisoheptanonitrile, keep the reaction at this temperature for 5 hours, and then recover the solvent by distillation under reduced pressure to obtain alicyclic epoxy resin prepolymer S3 ;
PUM
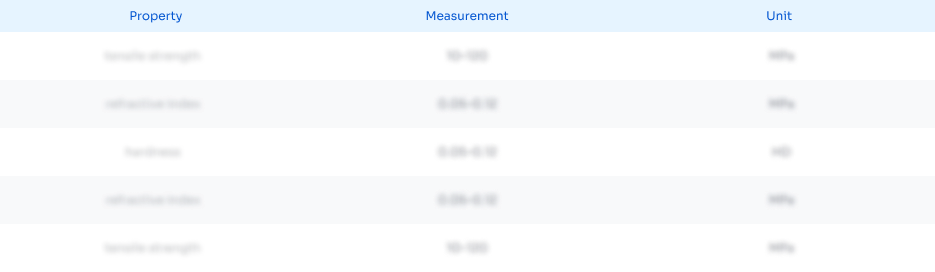
Abstract
Description
Claims
Application Information

- Generate Ideas
- Intellectual Property
- Life Sciences
- Materials
- Tech Scout
- Unparalleled Data Quality
- Higher Quality Content
- 60% Fewer Hallucinations
Browse by: Latest US Patents, China's latest patents, Technical Efficacy Thesaurus, Application Domain, Technology Topic, Popular Technical Reports.
© 2025 PatSnap. All rights reserved.Legal|Privacy policy|Modern Slavery Act Transparency Statement|Sitemap|About US| Contact US: help@patsnap.com