A gear shaft heat treatment process
A gear shaft and process technology, applied in heat treatment furnaces, heat treatment equipment, manufacturing tools, etc., can solve problems such as weak anti-stripping and anti-accident capabilities, low surface hardness of the shaft body, shallow hardened layer, etc., to improve hardenability And hardenability, improve wear resistance and fatigue resistance, increase the effect of austenite stability
- Summary
- Abstract
- Description
- Claims
- Application Information
AI Technical Summary
Problems solved by technology
Method used
Examples
Embodiment 1
[0018] A gear shaft heat treatment process, comprising the steps of:
[0019] (1) First normalize and heat the forged gear shaft blank to 1000°C for austenitization for 0.5h;
[0020] (2) Then cool to 850°C with the furnace for spheroidizing annealing for 2 hours, and then air cool to room temperature;
[0021] (3) After quenching and heating the gear shaft blank to 950°C for 1 hour, oil cooling;
[0022] (4) When the gear shaft blank is cooled to 350°C, put it into a tempering furnace, heat it at 500°C for 1 hour for tempering treatment, then cool it to 250°C with the furnace, and then take it out of the furnace and air-cool it to room temperature.
[0023] The forging step before the heat treatment process is to firstly heat the gear shaft blank to 1100° C., hold it for 2 hours, and then take it out of the furnace for forging.
[0024] The composition and weight percentage of the gear shaft blank are 0.25% C, 0.25% Si, 2.50% Cr, 1.50% Mn, 0.15% Mo, 0.15% V, 0.03% Y, and th...
Embodiment 2
[0028] A gear shaft heat treatment process, comprising the steps of:
[0029] (1) First normalize and heat the forged gear shaft blank to 1100° C. for austenitization for 0.5 h;
[0030] (2) Then cool to 900°C with the furnace for spheroidizing annealing for 1 hour, and then air cool to room temperature;
[0031] (3) After quenching and heating the gear shaft blank to 1050°C for 0.5h, oil cooling;
[0032] (4) When the gear shaft blank is cooled to 200°C, put it into a tempering furnace, heat it at 450°C for 2 hours and temper it, then cool it to 300°C with the furnace, and then take it out of the furnace and air cool it to room temperature.
[0033] The forging step before the heat treatment process is to firstly heat the gear shaft blank to 1200° C., hold it for 1 hour, and then take it out of the furnace for forging.
[0034] The composition and weight percentage of the gear shaft blank are 0.35% C, 0.35% Si, 3.50% Cr, 2.00% Mn, 0.20% Mo, 0.20% V, 0.05% Y, and the balance...
Embodiment 3
[0038] A gear shaft heat treatment process, comprising the steps of:
[0039] (1) First normalize and heat the forged gear shaft blank to 1050° C. for austenitization for 1 hour;
[0040] (2) Then cool to 880°C with the furnace for spheroidizing annealing for 1 hour, and then air cool to room temperature;
[0041] (3) After quenching and heating the gear shaft blank to 1000°C for 0.5h, oil cooling;
[0042] (4) When the gear shaft blank is cooled to 300°C, put it into a tempering furnace, heat it at 480°C for 2 hours and temper it, then cool it to 280°C with the furnace, and then take it out of the furnace and air cool it to room temperature.
[0043] The forging step before the heat treatment process is to firstly heat the gear shaft blank to 1150° C., hold it for 1 hour, and then take it out of the furnace for forging.
[0044] The composition and weight percentage of the gear shaft blank are 0.30% C, 0.35% Si, 3.00% Cr, 1.80% Mn, 0.15% Mo, 0.17% V, 0.04% Y, and the balanc...
PUM
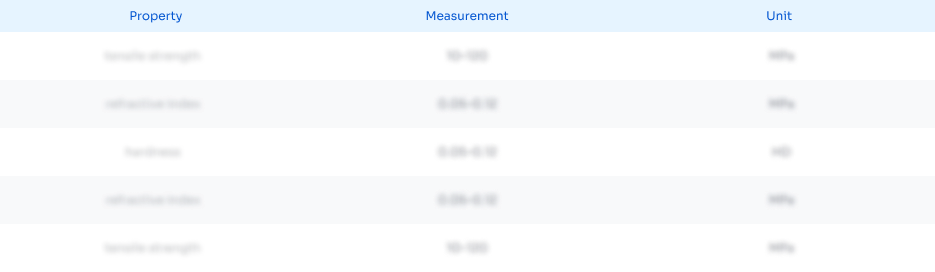
Abstract
Description
Claims
Application Information

- R&D
- Intellectual Property
- Life Sciences
- Materials
- Tech Scout
- Unparalleled Data Quality
- Higher Quality Content
- 60% Fewer Hallucinations
Browse by: Latest US Patents, China's latest patents, Technical Efficacy Thesaurus, Application Domain, Technology Topic, Popular Technical Reports.
© 2025 PatSnap. All rights reserved.Legal|Privacy policy|Modern Slavery Act Transparency Statement|Sitemap|About US| Contact US: help@patsnap.com