Casting process of corrosion-resistant pipeline valve
A technology of pipeline valve and casting process, applied in manufacturing tools, casting molding equipment, casting molds, etc., can solve the problems of complex valve casting process and low valve quality, achieve simple and easy casting process, improve dispersion and compatibility properties, good corrosion resistance and flame retardancy
- Summary
- Abstract
- Description
- Claims
- Application Information
AI Technical Summary
Problems solved by technology
Method used
Image
Examples
Embodiment 1
[0028] This embodiment provides a casting process for a corrosion-resistant pipeline valve. The valve includes a valve body and a protective layer coated on the valve body. The casting process for modifying the valve specifically includes the following steps:
[0029] (1) According to the shape of the valve, use quartz sand, water glass and bentonite as modeling materials to make a corresponding mold, and open a gate on the mold, and then blow the mold with warm air, and then place it in Dry in the oven at 150°C, ready for use;
[0030] (2) Transport the raw materials used to manufacture the valve to the smelting electric furnace for smelting treatment to obtain the mother liquor;
[0031] (3) Pour the mother liquor into a mold preheated to 200°C. After pouring, keep it warm for 30 minutes to obtain a valve ingot;
[0032] (4) Grind the obtained valve ingot with sandpaper, and then clean the polished surface with acetone, and then dry it naturally. After drying, the surface of the obt...
Embodiment 2
[0045] This embodiment provides a casting process for a corrosion-resistant pipeline valve. The valve includes a valve body and a protective layer coated on the valve body. The casting process for modifying the valve specifically includes the following steps:
[0046] (1) According to the shape of the valve, use quartz sand, water glass and bentonite as modeling materials to make a corresponding mold, and open a gate on the mold, and then blow the mold with warm air, and then place it in Dry it in the oven at 190℃, ready for use;
[0047] (2) Transport the raw materials used to manufacture the valve to the smelting electric furnace for smelting treatment to obtain the mother liquor;
[0048] (3) Pour the mother liquor into a mold preheated to 300°C, after pouring, keep it warm for 40 minutes to obtain a valve ingot;
[0049] (4) Grind the obtained valve ingot with sandpaper, and then clean the polished surface with acetone, and then dry it naturally. After drying, the surface of the o...
Embodiment 3
[0062] This embodiment provides a casting process for a corrosion-resistant pipeline valve. The valve includes a valve body and a protective layer coated on the valve body. The casting process for modifying the valve specifically includes the following steps:
[0063] (1) According to the shape of the valve, use quartz sand, water glass and bentonite as modeling materials to make a corresponding mold, and open a gate on the mold, and then blow the mold with warm air, and then place it in Dry in the oven at 170°C, ready for use;
[0064] (2) Transport the raw materials used to manufacture the valve to the smelting electric furnace for smelting treatment to obtain the mother liquor;
[0065] (3) Pour the mother liquor into a mold preheated to 250°C. After pouring, keep it warm for 35 minutes to obtain a valve ingot;
[0066] (4) Grind the obtained valve ingot with sandpaper, and then clean the polished surface with acetone, and then dry it naturally. After drying, the surface of the obt...
PUM
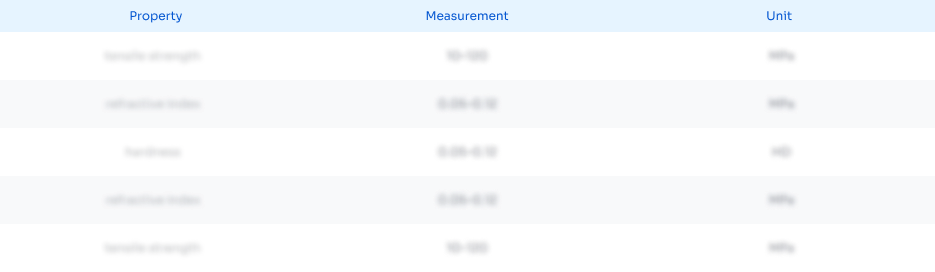
Abstract
Description
Claims
Application Information

- Generate Ideas
- Intellectual Property
- Life Sciences
- Materials
- Tech Scout
- Unparalleled Data Quality
- Higher Quality Content
- 60% Fewer Hallucinations
Browse by: Latest US Patents, China's latest patents, Technical Efficacy Thesaurus, Application Domain, Technology Topic, Popular Technical Reports.
© 2025 PatSnap. All rights reserved.Legal|Privacy policy|Modern Slavery Act Transparency Statement|Sitemap|About US| Contact US: help@patsnap.com