Particle-reinforced composite-material finite-element modeling method of considering microstructure interface
A composite material and microstructure technology, applied in special data processing applications, instruments, electrical digital data processing, etc., can solve problems such as low modeling efficiency, inability to accurately reflect the real microstructure of materials, and complicated operations
- Summary
- Abstract
- Description
- Claims
- Application Information
AI Technical Summary
Problems solved by technology
Method used
Image
Examples
Embodiment 1
[0178] The finite element modeling method of particle reinforced composite materials disclosed in this embodiment considering the microstructure interface, the specific implementation method is as follows:
[0179] Step 1. Use the Keyence laser scanning microscope to obtain a digital image of the microstructure of the particle-reinforced composite material SiCp / Al, and save it in JPEG format, such as figure 2 ;
[0180] For the SiCp / Al material used, the cross-section of the material is obtained after wire cutting, grinding, and polishing processes, and the oxidation and corrosion areas on the surface of the material are effectively removed, and the microstructure of the material is extracted using a KEYENCE laser scanning microscope , to obtain optical microscope images of the microstructure of the studied particle-reinforced composites.
[0181] Step 2: Use Photoshop to preprocess the original photos.
[0182]Use the cropping function of Photoshop to remove the black bord...
PUM
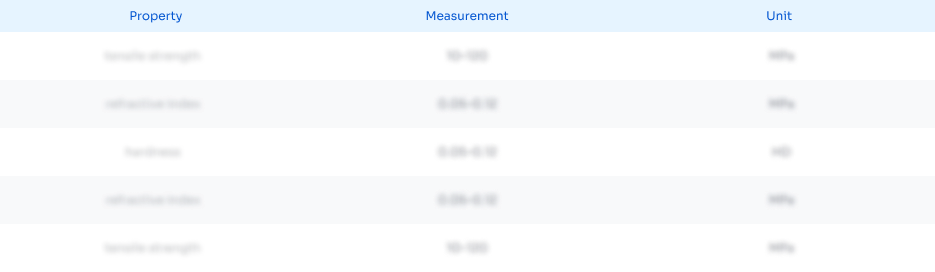
Abstract
Description
Claims
Application Information

- R&D Engineer
- R&D Manager
- IP Professional
- Industry Leading Data Capabilities
- Powerful AI technology
- Patent DNA Extraction
Browse by: Latest US Patents, China's latest patents, Technical Efficacy Thesaurus, Application Domain, Technology Topic, Popular Technical Reports.
© 2024 PatSnap. All rights reserved.Legal|Privacy policy|Modern Slavery Act Transparency Statement|Sitemap|About US| Contact US: help@patsnap.com