Smelting process of Cr-Mo steel ingot being low in sulfur, phosphorus and silicon
A smelting method and technology for steel ingots, which are applied in the field of smelting low-sulfur, low-phosphorus and low-silicon Cr-Mo steel ingots, can solve the problems of difficulty in slag floating, inconsistent steel plate flaw detection, etc., and achieve the effects of low cost, strong versatility and simple operation.
- Summary
- Abstract
- Description
- Claims
- Application Information
AI Technical Summary
Problems solved by technology
Method used
Image
Examples
Embodiment 1
[0019] One furnace of 12Cr2Mo1VR was smelted, 117 tons in a single furnace, 53 tons in a single steel ingot, and the thickness of the finished rolled steel plate was 137mm, and the length was 13500mm. The chemical composition and mass percentage of steel ingot are: C: 0.14%, Si: 0.06%, Mn: 0.57%, Cr: 2.34%, Mo: 1.02%, V: 0.304%, Ni: 0.14%, Ca: 0.001 %, P: 0.005%, S: 0.003%, As: 0.004%, Sn: 0.001%, Sb: 0.001%, and the balance is Fe and unavoidable impurities.
[0020] The low-sulfur, low-phosphorus, low-silicon, low-silicon Cr-Mo steel ingot smelting method in this embodiment includes electric furnace steelmaking process control, refining furnace refining process control, VOD process control and casting process control procedures. The specific process steps are as follows:
[0021] (1) Control process of electric furnace steelmaking process: in the process of electric furnace steelmaking, 38kg / t steel active quicklime and 23kg / t steel fluorite are added, and when electric furna...
Embodiment 2
[0028] One furnace of 12Cr2Mo1R was smelted, with a single furnace of 105 tons, a single steel ingot of 47 tons, and a finished rolled steel plate with a thickness of 134mm and a length of 12800mm. The chemical composition and mass percentage of steel ingot are: C: 0.12%, Si: 0.07%, Mn: 0.54%, Cr: 2.41%, Mo: 1.03%, V: 0.02%, Ni: 0.17%, Ca: 0.001 %, P: 0.004%, S: 0.002%, As: 0.003%, Sn: 0.001%, Sb: 0.001%, and the balance is Fe and unavoidable impurities.
[0029] (1) Control process of electric furnace steelmaking process: During the electric furnace steelmaking process, 43kg / t steel active quicklime and 23kg / t steel fluorite are added, and when electric furnace steel is tapped, S: 0.029%, P: 0.008%;
[0030] (2) Refining furnace refining process control process: during the refining furnace refining process, add active quicklime 5kg / t steel, fluorite 3kg / t steel, smelt for 35min; add Al wire 2.2kg / t steel at one time before adding alloy; add alloy After that, 500kg of metal C...
Embodiment 3
[0035] One furnace of 2.25Cr1Mo0.25V was smelted, with a single furnace of 112 tons, a single steel ingot of 52 tons, and a finished rolled steel plate with a thickness of 142mm and a length of 11870mm. The chemical composition and mass percentage of steel ingot are: C: 0.13%, Si: 0.10%, Mn: 0.53%, Cr: 2.39%, Mo: 1.01%, V: 0.31%, Ni: 0.18%, Ca: 0.001 %, P: 0.007%, S: 0.005%, As: 0.002%, Sn: 0.001%, Sb: 0.001%, and the balance is Fe and unavoidable impurities.
[0036] (1) Control process of electric furnace steelmaking process: in the process of electric furnace steelmaking, add 40kg / t steel active quicklime and 26kg / t steel fluorite, and when electric furnace is tapping, S: 0.03%, P: 0.009%;
[0037] (2) Refining furnace refining process control process: during the refining furnace refining process, add active quicklime 4kg / t steel, fluorite 2.6kg / t steel, smelt for 20min; add Al wire 2.1kg / t steel at one time before adding alloy; add Add 500kg of metal Cr after the alloy, a...
PUM
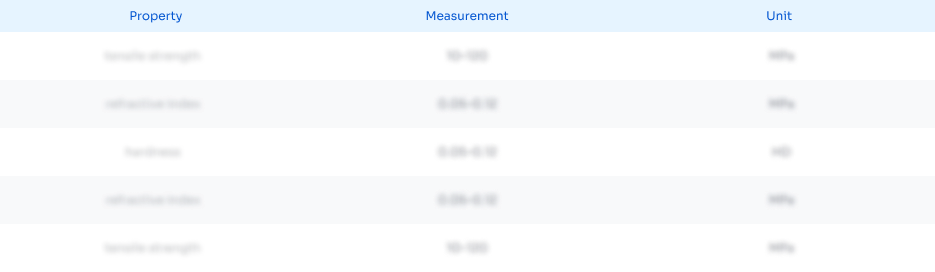
Abstract
Description
Claims
Application Information

- R&D Engineer
- R&D Manager
- IP Professional
- Industry Leading Data Capabilities
- Powerful AI technology
- Patent DNA Extraction
Browse by: Latest US Patents, China's latest patents, Technical Efficacy Thesaurus, Application Domain, Technology Topic, Popular Technical Reports.
© 2024 PatSnap. All rights reserved.Legal|Privacy policy|Modern Slavery Act Transparency Statement|Sitemap|About US| Contact US: help@patsnap.com