Stainless steel surface treatment method capable of improving anti-corrosion capacity
A surface treatment, stainless steel technology, applied in the direction of metal material coating process, coating, solid-state diffusion coating, etc., can solve problems such as volatilization, protective coating and stainless steel substrate are easy to crack, and affect the performance of stainless steel products, etc., to achieve penetration The effect of good layer quality, easy process control and stable surface performance
- Summary
- Abstract
- Description
- Claims
- Application Information
AI Technical Summary
Problems solved by technology
Method used
Examples
Embodiment 1
[0015] The stainless steel surface treatment method to improve anti-corrosion ability includes the following steps:
[0016] (1) A steel sample with a size of 15*15*10mm was taken as the substrate, and aluminum nitride AlN was selected as the source material;
[0017] (2) The steel sample was polished with sandpaper for multiple passes, and then mechanically polished with 0.5 μm diamond spray polishing agent, then ultrasonically cleaned in acetone, alcohol, and deionized water for 10 minutes, dried, and packaged for use;
[0018] (3) Carry out aluminizing treatment with a double-layer glow plasma metallizing vacuum furnace, use a stainless steel cylinder as an auxiliary cathode, and place the substrate and aluminum nitride AlN in the auxiliary cathode;
[0019] (4) Start surface treatment: process parameters are frequency 55Hz, pole spacing 15mm, holding temperature 800°C, holding time 2h, source voltage 400V, cathode voltage 300V, after treatment the sample is cooled to room ...
Embodiment 2
[0025] The stainless steel surface treatment method to improve anti-corrosion ability includes the following steps:
[0026] (1) A steel sample with a size of 15*15*10mm was taken as the substrate, and aluminum nitride AlN was selected as the source material;
[0027] (2) The steel sample was polished with sandpaper for multiple passes, and then mechanically polished with 0.5 μm diamond spray polishing agent, then ultrasonically cleaned in acetone, alcohol, and deionized water for 10 minutes, dried, and packaged for use;
[0028] (3) Carry out aluminizing treatment with a double-layer glow plasma metallizing vacuum furnace, use a stainless steel cylinder as an auxiliary cathode, and place the substrate and aluminum nitride AlN in the auxiliary cathode;
[0029] (4) Start surface treatment: process parameters are frequency 60Hz, pole spacing 10mm, holding temperature 900°C, holding time 3h, source voltage 400V, cathode voltage 400V, after treatment the sample is cooled to room ...
Embodiment 3
[0032] The stainless steel surface treatment method to improve anti-corrosion ability includes the following steps:
[0033] (1) A steel sample with a size of 15*15*10mm was taken as the substrate, and aluminum nitride AlN was selected as the source material;
[0034] (2) The steel sample was polished with sandpaper for multiple passes, and then mechanically polished with 0.5 μm diamond spray polishing agent, then ultrasonically cleaned in acetone, alcohol, and deionized water for 10 minutes, dried, and packaged for use;
[0035] (3) Carry out aluminizing treatment with a double-layer glow plasma metallizing vacuum furnace, use a stainless steel cylinder as an auxiliary cathode, and place the substrate and aluminum nitride AlN in the auxiliary cathode;
[0036] (4) Start surface treatment: process parameters are frequency 55Hz, pole spacing 15mm, holding temperature 800°C, holding time 2h, source voltage 600V, cathode voltage 400V, after treatment the sample is cooled to room ...
PUM
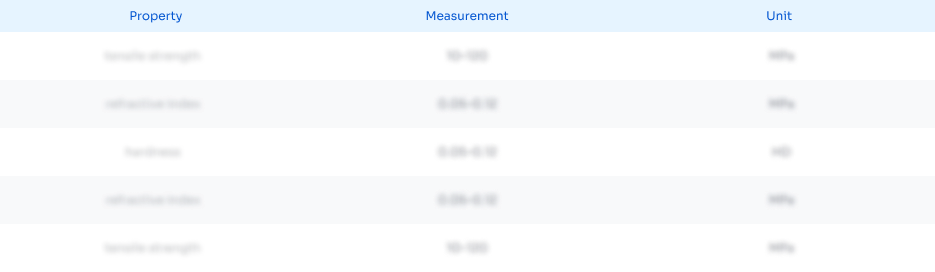
Abstract
Description
Claims
Application Information

- Generate Ideas
- Intellectual Property
- Life Sciences
- Materials
- Tech Scout
- Unparalleled Data Quality
- Higher Quality Content
- 60% Fewer Hallucinations
Browse by: Latest US Patents, China's latest patents, Technical Efficacy Thesaurus, Application Domain, Technology Topic, Popular Technical Reports.
© 2025 PatSnap. All rights reserved.Legal|Privacy policy|Modern Slavery Act Transparency Statement|Sitemap|About US| Contact US: help@patsnap.com