Die polishing method
A mold and rough polishing technology, applied in surface polishing machine tools, grinding/polishing equipment, manufacturing tools, etc., can solve the problems of poor polishing effect, high mold rework rate, affecting mold production efficiency, etc. The effect of high finish and excellent grinding effect
- Summary
- Abstract
- Description
- Claims
- Application Information
AI Technical Summary
Problems solved by technology
Method used
Examples
Embodiment 1
[0016] A mold polishing method, comprising the following steps:
[0017] (1) Roughly polish the formed mold with oil stone, and use lubricating coolant and oil stone for rough polishing, wherein the lubricating coolant is made of the following components in parts by weight: 1 part of dimethyl suberate, ethyl bromide 6 parts of ethylene glycol acetal, 20 parts of n-hexane;
[0018] (2) Attach the sandpaper to the wooden strip for grinding, and the wooden strip is at 50° to the surface of the mold;
[0019] (3) The polishing cloth wheel is mixed with abrasive paste for fine polishing, wherein the abrasive paste is made of the following components in parts by weight: 14 parts by weight of phosphoglyceric acid, 19 parts of methyl epoxyacetyl ricinoleate, 30 parts of cedar oil, silicon carbide 120 servings.
[0020] Specifically, the lubricating coolant in the above step (1) is made by the following method: after fully mixing dimethyl suberate and n-hexane, then adding bromoaceta...
Embodiment 2
[0024] A mold polishing method, comprising the following steps:
[0025] (1) Roughly polish the formed mold with oilstone, and use lubricating coolant and oilstone for rough polishing, wherein the lubricating coolant is made of the following components by weight: 2 parts of dimethyl suberate, ethyl bromide 8 parts of ethylene glycol acetal, 23 parts of n-hexane;
[0026] (2) Attach the sandpaper to the wooden strip for grinding, and the wooden strip is at 55° to the surface of the mold;
[0027] (3) The polishing cloth wheel is mixed with abrasive paste for fine polishing, wherein the abrasive paste is made of the following components by weight: 16 parts of phosphoglyceric acid, 22 parts of methyl epoxyacetyl ricinoleate, 33 parts of cedar oil, silicon carbide 125 copies.
[0028] Specifically, the lubricating coolant in the above step (1) is made by the following method: after fully mixing dimethyl suberate and n-hexane, then adding bromoacetaldehyde ethylene glycol acetal ...
Embodiment 3
[0032] A mold polishing method, comprising the following steps:
[0033] (1) Roughly polish the formed mold with oil stone, and use lubricating coolant and oil stone for rough polishing, wherein the lubricating coolant is made of the following components in parts by weight: 3 parts of dimethyl suberate, ethyl bromide 9 parts of ethylene glycol acetal, 25 parts of n-hexane;
[0034] (2) Attach the sandpaper to the wooden strip for grinding, and the wooden strip is at 60° to the surface of the mold;
[0035] (3) The polishing cloth wheel is mixed with abrasive paste for fine polishing, wherein the abrasive paste is made of the following components by weight: 23 parts of phosphoglyceric acid, 26 parts of methyl epoxyacetyl ricinoleate, 35 parts of cedar oil, silicon carbide 135 copies.
[0036] Specifically, the lubricating coolant in the above step (1) is made by the following method: after fully mixing dimethyl suberate and n-hexane, then adding bromoacetaldehyde ethylene gly...
PUM
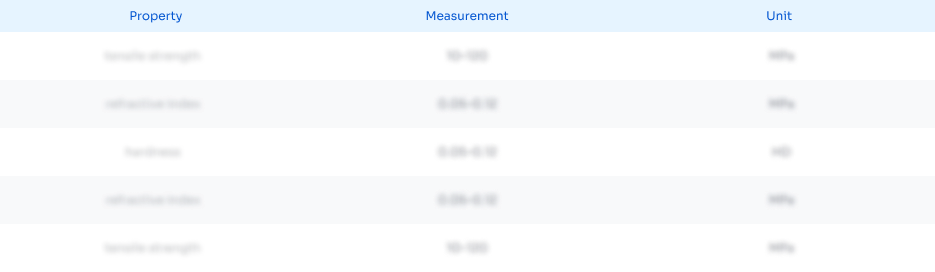
Abstract
Description
Claims
Application Information

- Generate Ideas
- Intellectual Property
- Life Sciences
- Materials
- Tech Scout
- Unparalleled Data Quality
- Higher Quality Content
- 60% Fewer Hallucinations
Browse by: Latest US Patents, China's latest patents, Technical Efficacy Thesaurus, Application Domain, Technology Topic, Popular Technical Reports.
© 2025 PatSnap. All rights reserved.Legal|Privacy policy|Modern Slavery Act Transparency Statement|Sitemap|About US| Contact US: help@patsnap.com