Preparation method of nano ceramic powder with lubrication function
A nano-ceramic powder, functional technology, applied in the field of nano-materials, achieves the effect of strong practicability, simple process and easy-to-obtain raw materials
- Summary
- Abstract
- Description
- Claims
- Application Information
AI Technical Summary
Problems solved by technology
Method used
Examples
Embodiment 1
[0021] (1) Mix 2 parts of alumina, 1 part of calcium borate, 2 parts of carbon powder, 5 parts of carbon fiber, 1 part of titanium carbide, and 5 parts of polyethylene glycol into a high-temperature roller smelting furnace for pressurized roller smelting. The temperature is 1050°C, the pressure is 8MPa, and the reaction is continued for 3 hours. Then, 5 parts of lubricant and 3 parts of phenylethyl alcohol oleate are added, and the stirring is continued for 50 minutes. Insulation, wherein the lubricant is composed of: 7 parts of silicate, 2 parts of phosphate, 1 part of castor oil, 5 parts of glycerol, 1 part of lithium hydroxide, and 1 part of boron nitride;
[0022] (2) Inject the high-temperature mixed solution of step (1) into a screw-type stirring paddle, and carry out cooling and stirring on the above-mentioned mixed solution. The stirring speed is controlled at 500 rpm, and stirring is performed while cooling. Stirring at ℃ for 30 minutes to prepare a semi-solid slurry;...
Embodiment 2
[0027] (1) Mix 3 parts of alumina, 2 parts of calcium borate, 4 parts of carbon powder, 10 parts of carbon fiber, 2 parts of titanium carbide, and 7 parts of polyethylene glycol into a high-temperature roller smelting furnace for pressurized roller smelting. The temperature is 1050°C, the pressure is 8MPa, and the reaction is continued for 3 hours. Then, 5 parts of lubricant and 3 parts of lauryl phenylacetate are added, and the stirring is continued for 50 minutes. Insulation, wherein the lubricant is composed of: 7 parts of silicate, 2 parts of phosphate, 1 part of castor oil, 5 parts of glycerol, 1 part of lithium hydroxide, and 1 part of boron nitride;
[0028] (2) Inject the high-temperature mixed solution of step (1) into the screw-type stirring paddle, lower the temperature and stir the above-mentioned mixed solution, control the stirring speed at 700 rpm, stir while cooling down, and when the temperature reaches 670° C. Stirring at ℃ for 30 minutes to prepare a semi-so...
Embodiment 3
[0033] (1) 5 parts of alumina, 3 parts of calcium borate, 5 parts of carbon powder, 15 parts of carbon fiber, 2 parts of titanium carbide, and 9 parts of polyethylene glycol are mixed and injected into a high-temperature roller smelting furnace for pressurized roller smelting. The temperature is 1050°C, the pressure is 8MPa, and the reaction is continued for 3 hours. Then, 5 parts of lubricant and 3 parts of maleic acid alcohol ester are added, and the stirring is continued for 50 minutes. Keep warm above ℃, and the lubricant composition is: 7 parts of silicate, 2 parts of phosphate, 1 part of castor oil, 5 parts of glycerol, 1 part of lithium hydroxide, and 1 part of boron nitride;
[0034] (2) Inject the high-temperature mixed solution of step (1) into the screw-type stirring paddle, and carry out cooling and stirring on the above-mentioned mixed solution. Stirring at ℃ for 30 minutes to prepare a semi-solid slurry;
[0035] (3) inject the semi-solid slurry in the step (2) ...
PUM
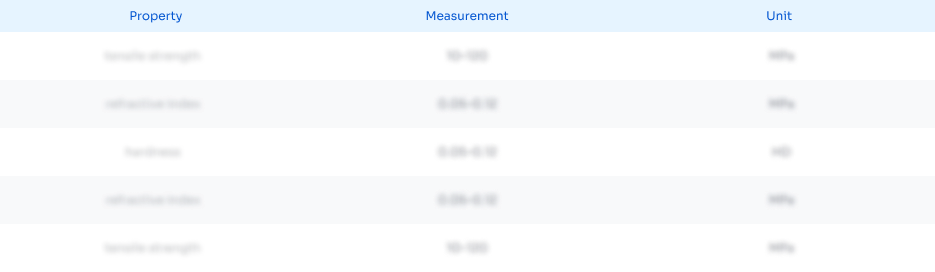
Abstract
Description
Claims
Application Information

- Generate Ideas
- Intellectual Property
- Life Sciences
- Materials
- Tech Scout
- Unparalleled Data Quality
- Higher Quality Content
- 60% Fewer Hallucinations
Browse by: Latest US Patents, China's latest patents, Technical Efficacy Thesaurus, Application Domain, Technology Topic, Popular Technical Reports.
© 2025 PatSnap. All rights reserved.Legal|Privacy policy|Modern Slavery Act Transparency Statement|Sitemap|About US| Contact US: help@patsnap.com