Electric heating wire formulation and electric heating wire preparation process
A preparation process and heating wire technology, applied in the direction of heating element materials, etc., can solve the problems of poor practicability, limited service life, poor performance, etc., and achieve the effect of improving creep resistance and improving performance.
- Summary
- Abstract
- Description
- Claims
- Application Information
AI Technical Summary
Problems solved by technology
Method used
Examples
Embodiment 1
[0029] Based on the raw materials of the above mass fraction ratio, take Cr30, Ni50, W1-5, Mo1-3, Ai5-10, Si1-3, Y 2 o 3 Composite oxide 0.3-3, the balance is Fe.
[0030] A preparation process for heating wire, based on the ratio of the above-mentioned raw materials, comprising the following steps:
[0031] Step 1: Pour the above-mentioned alloy powder into the high-energy ball mill tank according to the proportion and mix it mechanically;
[0032] Step 2: The evenly mixed alloy powder is taken out of the tank and enters the vacuum furnace for high-temperature hydrogen reduction;
[0033] Step 3: Put the reduced powder into a high-energy ball mill tank, add anhydrous gasoline and viscose, and add high-speed steel balls with a volume fraction of 60% in the high-energy ball mill tank. More than or equal to 48 hours, after the cover is sealed, carry out mechanical alloying ball milling for 48 hours;
[0034] Step 4: Sieve the ground powder to remove impurities and pour it in...
Embodiment 2
[0041] Based on the raw material of the mass fraction ratio of Example 1, take Cr50, Ni30, W1-5, Mo1-3, Ai5-10, Si1-3, Y 2 o 3 Composite oxide 0.3-3, the balance is Fe.
[0042] A preparation process of heating wire, based on the proportioning of a kind of raw material of embodiment 2, comprises the following steps:
[0043] Step 1: Pour the above-mentioned alloy powder into the high-energy ball mill tank according to the proportion and mix it mechanically;
[0044] Step 2: The evenly mixed alloy powder is taken out of the tank and enters the vacuum furnace for high-temperature hydrogen reduction;
[0045] Step 3: Put the reduced powder into a high-energy ball mill tank, add anhydrous gasoline and viscose, and add high-speed steel balls with a volume fraction of 60% in the high-energy ball mill tank, set the speed to 300r / min, and the ball milling time More than or equal to 48 hours, after the cover is sealed, carry out mechanical alloying ball milling for 48 hours;
[004...
Embodiment 3
[0053] Based on the raw materials of the mass fraction ratio of embodiment one and embodiment two, select a kind of optimal raw material ratio: get Cr40, Ni40, W1-5, Mo1-3, Ai5-10, Si1-3, Y 2 o 3 Composite oxide 0.3-3, the balance is Fe.
[0054] A kind of preparation technology of heating wire, based on the proportioning of the best raw material of embodiment three, comprises the following steps:
[0055] Step 1: Pour the above-mentioned alloy powder into the high-energy ball mill tank according to the proportion and mix it mechanically;
[0056] Step 2: The evenly mixed alloy powder is taken out of the tank and enters the vacuum furnace for high-temperature hydrogen reduction;
[0057] Step 3: Put the reduced powder into a high-energy ball mill tank, add anhydrous gasoline and viscose, and add high-speed steel balls with a volume fraction of 60% in the high-energy ball mill tank. More than or equal to 48 hours, after the cover is sealed, carry out mechanical alloying ball...
PUM
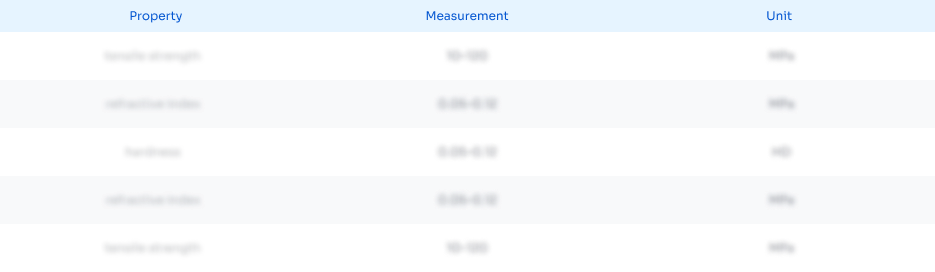
Abstract
Description
Claims
Application Information

- Generate Ideas
- Intellectual Property
- Life Sciences
- Materials
- Tech Scout
- Unparalleled Data Quality
- Higher Quality Content
- 60% Fewer Hallucinations
Browse by: Latest US Patents, China's latest patents, Technical Efficacy Thesaurus, Application Domain, Technology Topic, Popular Technical Reports.
© 2025 PatSnap. All rights reserved.Legal|Privacy policy|Modern Slavery Act Transparency Statement|Sitemap|About US| Contact US: help@patsnap.com