Preparation method for abrasion resistant alloy material
A wear-resistant alloy and a technology for preparation steps are applied in the preparation of wear-resistant alloy materials and in the field of wear-resistant materials, which can solve the problems of non-dense interior, backward smelting process, low casting technology level, etc., so as to improve work hardening and reduce yield strength. and tensile strength, the effect of improving compactness
- Summary
- Abstract
- Description
- Claims
- Application Information
AI Technical Summary
Problems solved by technology
Method used
Examples
example 1
[0020] Put the tungsten powder in a stainless steel ball mill jar, mill it at a speed of 400r / min for 4 hours, and pass through a 200-mesh sieve to obtain tungsten powder; in parts by weight, take 4 parts of obsidian, 8 parts of pitchite, and 9 parts of perlite , washed with clean water, dried naturally and placed in a ball mill jar, ball milled at a speed of 300r / min for 2 hours, and passed through a 150 mesh sieve to obtain a mixed ball milled powder; according to a mass ratio of 3:1, mix the tungsten powder and the mixed ball milled powder , continue stirring for 30 minutes with a mixer at a speed of 150r / min to obtain a uniformly mixed powder mixture; take a steel ingot with a phosphorus and sulfur content of 0.04%, and the model is HPB300, place the steel ingot in an electric melting furnace, and control the temperature at 1200 °C, hold the pressure at 500MPa for 4 hours to obtain a molten liquid; take a powder mixture of 20% of the mass of the ingot and add it to the molt...
example 2
[0022] Put the tungsten powder in a stainless steel ball mill jar, mill it at a speed of 450r / min for 4.5 hours, and pass through a 230-mesh sieve to obtain tungsten powder; in parts by weight, take 5 parts of obsidian, 10 parts of turpentine, and 12 parts of pearl Rock, washed with clean water, dried naturally and placed in a ball mill jar, ball milled at a speed of 350r / min for 2.5h, and passed through a 170 mesh sieve to obtain a mixed ball mill powder; according to a mass ratio of 3:1, the tungsten powder and the mixed ball mill The powder is mixed, continuously stirred at a speed of 160r / min for 30min with a mixer to obtain a uniformly mixed powder mixture; get a steel ingot with a phosphorus and sulfur content of 0.04%, the model is GB700-79, place the steel ingot in an electric melting furnace, and The temperature was controlled at 1250°C, and the pressure was maintained at 550MPa for 4.5 hours to obtain a molten liquid; the powder mixture of 20% of the mass of the ingot...
example 3
[0024] Put the tungsten powder in a stainless steel ball mill jar, mill it at a speed of 500r / min for 5 hours, and pass through a 250-mesh sieve to obtain tungsten powder; in parts by weight, take 6 parts of obsidian, 12 parts of pitchite, and 18 parts of perlite , washed with clean water, dried naturally and placed in a ball mill jar, ball milled at a speed of 400r / min for 3 hours, and passed through a 200 mesh sieve to obtain a mixed ball milled powder; according to a mass ratio of 3:1, mix the tungsten powder and the mixed ball milled powder , use a mixer to continuously stir for 30 minutes at a speed of 180r / min to obtain a uniformly mixed powder mixture; take a steel ingot with a phosphorus and sulfur content of 0.04%, and the model is Q235, place the steel ingot in an electric melting furnace, and control the temperature at 1300 °C, hold the pressure at 600MPa for 5 hours to obtain a molten liquid; take a powder mixture of 20% of the mass of the ingot and add it to the mo...
PUM
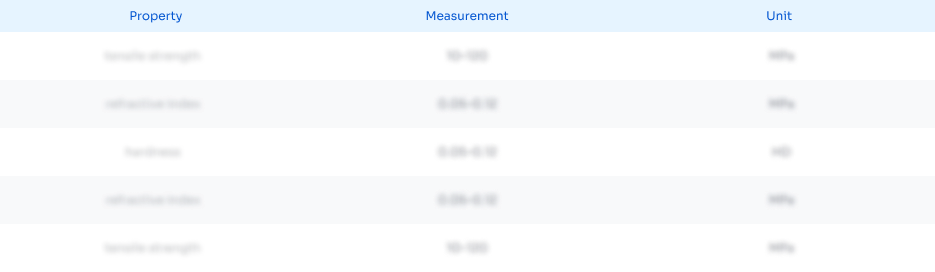
Abstract
Description
Claims
Application Information

- R&D
- Intellectual Property
- Life Sciences
- Materials
- Tech Scout
- Unparalleled Data Quality
- Higher Quality Content
- 60% Fewer Hallucinations
Browse by: Latest US Patents, China's latest patents, Technical Efficacy Thesaurus, Application Domain, Technology Topic, Popular Technical Reports.
© 2025 PatSnap. All rights reserved.Legal|Privacy policy|Modern Slavery Act Transparency Statement|Sitemap|About US| Contact US: help@patsnap.com