Manufacturing technology for ceramic reinforced metal-based composite squeeze roller
A metal-matrix composite and manufacturing process technology, which is applied in the field of metal-based composite materials, can solve the problems of increasing the manufacturing cost of roller presses, high carbide costs, and complicated preparation processes, so as to save costs, improve service life, and improve the manufacturing process. simple effect
- Summary
- Abstract
- Description
- Claims
- Application Information
AI Technical Summary
Problems solved by technology
Method used
Image
Examples
Embodiment 1
[0031] A manufacturing process of a ceramic-reinforced metal-matrix composite extrusion roll, comprising the following steps:
[0032] (1) Fully mix 100-mesh zirconium corundum ceramic particles and binder according to 9:1, fill them into a mold to prepare a third cylindrical ceramic particle preform;
[0033] (2) Preheat the prefabricated body to 850°C and fix it in the sand mold cavity, and pour high manganese steel molten metal at 1550°C to obtain the wear-resistant block 2;
[0034] (3) The wear-resistant block 2 is heated to 700°C at 90°C / h, kept for 1.5h, then heated to 1050°C at 50°C / h, water-quenched after holding for 2h, and then finished to ensure that the chuck 5 and the slot 6 and keyway 9 to achieve the required accuracy, and bolt holes are processed on the edge of the wear block;
[0035] (4) 40CrNiMo steel is made into roller tire 1 by upsetting, drawing, and die forging. It is finished after normalizing at 920°C, oil quenching at 870°C, and tempering at 300°C ...
Embodiment 2
[0039] A manufacturing process of a ceramic-reinforced metal-matrix composite extrusion roll, comprising the following steps:
[0040] (1) Fully mix 60-mesh zirconium corundum ceramic particles and binder according to 9:1, fill them into a mold to prepare a quarter cylindrical ceramic particle preform;
[0041] (2) Preheat the prefabricated body to 900°C and fix it in the mold cavity, pour Cr26 high-chromium cast iron metal liquid at 1500°C to compound by centrifugal casting, and obtain the wear-resistant block 2;
[0042] (3) The wear-resistant block 2 is heated to 600°C at 60°C / h, kept for 2h, then heated to 980°C at 50°C / h, kept for 1h, and air-cooled; then finish machining to ensure that the chuck 5 and the slot 6 and the keyway 9 to achieve the required accuracy, and process bolt holes on the edge of the wear block;
[0043] (4) 40CrNiMo steel is made into roller tire 1 by upsetting, drawing, and die forging. It is finished after normalizing at 920°C, oil quenching at 87...
Embodiment 3
[0047] A manufacturing process of a ceramic-reinforced metal-matrix composite extrusion roll, comprising the following steps:
[0048] (1) Fully mix 80-mesh WC ceramic particles and binder according to 9:1, fill them into a mold to prepare a quarter-cylindrical ceramic particle preform;
[0049] (2) Preheat the preform to 900°C and fix it in the mold cavity, pour 65Mn molten metal at 1500°C and perform compounding by extrusion casting to obtain the wear-resistant block 2;
[0050] (3) The wear-resistant block 2 is heated to 820°C at 60°C / h, kept for 0.5h, oil quenched, heated to 380°C for 2h and air-cooled; The required accuracy, and bolt holes are machined on the edge of the wear block;
[0051] (4) 40CrNiMo steel is made into roller tire 1 by upsetting, drawing, and die forging. It is finished after normalizing at 920°C, oil quenching at 870°C, and tempering at 300°C twice, and wear-resistant block 2 is processed matching keyway and bolt holes.
[0052] (5) Each wear-resist...
PUM
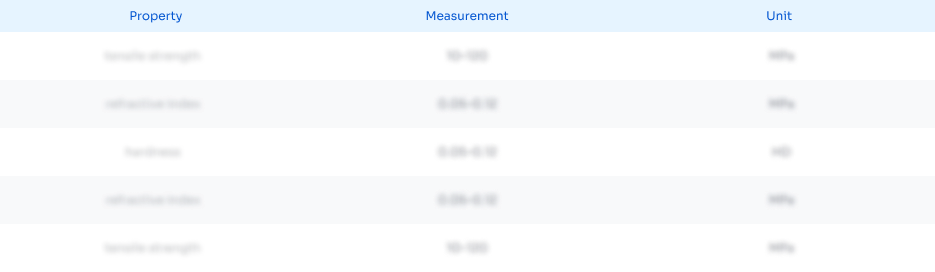
Abstract
Description
Claims
Application Information

- R&D
- Intellectual Property
- Life Sciences
- Materials
- Tech Scout
- Unparalleled Data Quality
- Higher Quality Content
- 60% Fewer Hallucinations
Browse by: Latest US Patents, China's latest patents, Technical Efficacy Thesaurus, Application Domain, Technology Topic, Popular Technical Reports.
© 2025 PatSnap. All rights reserved.Legal|Privacy policy|Modern Slavery Act Transparency Statement|Sitemap|About US| Contact US: help@patsnap.com