Alloy for impeller of aircraft gas compressor
A compressor and aircraft technology, applied in the field of alloys, can solve problems such as fracture toughness, stress corrosion resistance that cannot meet high strength, high toughness, high corrosion resistance, unstable working status of compressors, and restrictions on the development of the aircraft industry. Achieve the effect of excellent surface quality and crystalline structure, good hardness, and prevent cracking
- Summary
- Abstract
- Description
- Claims
- Application Information
AI Technical Summary
Problems solved by technology
Method used
Examples
Embodiment 1
[0029] An alloy used for an aircraft compressor impeller is made of the following raw materials in parts by weight: 86.0 parts of Al, 3.4 parts of Ni, 0.7 parts of Si, 1.0 part of Fe, 1.8 parts of Cu, 0.8 parts of Mn, and 0.4 parts of Mg.
[0030] A kind of described production technique for the alloy of aircraft compressor impeller, concrete steps are:
[0031] (1) Dry pot preparation: blast the vacuum furnace crucible, heat it to 700°C, and keep it for 4 hours; then, when the crucible is cooled to 200°C, spray the crucible with liquid spray; then preheat the crucible to 600°C , keep warm for 2h; wherein, the liquid spray material is silicon nitride solution;
[0032] (2) Vacuum melting treatment: place the 1060 Al plate on the bottom of the vacuum furnace crucible, then add Ni, Si, Fe, Cu, Mn, Mg into the vacuum furnace crucible; then vacuum the vacuum furnace crucible to 1Mpa , heated up to 1100°C for high-temperature refining; then maintained at 930°C for low-temperature ...
Embodiment 2
[0039] An alloy used for an aircraft compressor impeller is made of the following raw materials in parts by weight: 95.0 parts of Al, 2.0 parts of Ni, 1.2 parts of Si, 0.7 parts of Fe, 2.6 parts of Cu, 0.4 parts of Mn, and 0.8 parts of Mg.
[0040] A kind of described production technique for the alloy of aircraft compressor impeller, concrete steps are:
[0041] (1) Dry pot preparation: blast the vacuum furnace crucible and heat it to 800°C for 2 hours; then when the crucible is cooled to 300°C, spray the crucible with liquid spray material; then preheat the crucible to 500°C , keep warm for 3h; wherein, the liquid spray material is silicon nitride solution;
[0042] (2) Vacuum melting treatment: place the 1060 Al plate on the bottom of the vacuum furnace crucible, then add Ni, Si, Fe, Cu, Mn, Mg into the vacuum furnace crucible; then vacuum the vacuum furnace crucible to 1Mpa , heat up to 1250°C for high-temperature refining; then maintain the temperature at 890°C for low-t...
Embodiment 3
[0049] An alloy used for an aircraft compressor impeller is made of the following raw materials in parts by weight: 89.2 parts of Al, 3.1 parts of Ni, 0.9 parts of Si, 0.8 parts of Fe, 2.2 parts of Cu, 0.6 parts of Mn, and 0.6 parts of Mg.
[0050] A kind of described production technique for the alloy of aircraft compressor impeller, concrete steps are:
[0051] (1) Dry pot preparation: blast the vacuum furnace crucible and heat it to 750°C for 3 hours; then when the crucible is cooled to 250°C, spray the crucible with liquid spray material; then preheat the crucible to 530°C , heat preservation for 2.5h; wherein, the liquid spray material is a silicon nitride solution;
[0052] (2) Vacuum melting treatment: place the 1060 Al plate on the bottom of the vacuum furnace crucible, then add Ni, Si, Fe, Cu, Mn, Mg into the vacuum furnace crucible; then vacuum the vacuum furnace crucible to 1Mpa , heat up to 1170°C for high-temperature refining; then maintain the temperature at 910...
PUM
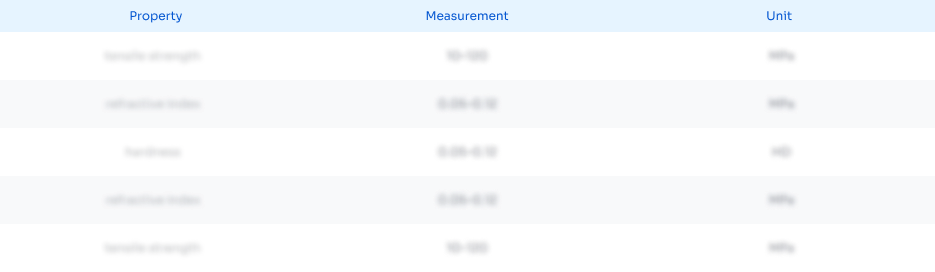
Abstract
Description
Claims
Application Information

- R&D Engineer
- R&D Manager
- IP Professional
- Industry Leading Data Capabilities
- Powerful AI technology
- Patent DNA Extraction
Browse by: Latest US Patents, China's latest patents, Technical Efficacy Thesaurus, Application Domain, Technology Topic, Popular Technical Reports.
© 2024 PatSnap. All rights reserved.Legal|Privacy policy|Modern Slavery Act Transparency Statement|Sitemap|About US| Contact US: help@patsnap.com