Epoxy resin-based composite wear-resistant coating material and preparation method thereof
A technology of epoxy resin and wear-resistant coating, which is applied in the field of composite materials, can solve the problems of poor bonding performance and wear resistance of the base layer, low tensile strength and low shear strength, etc., and achieve good wear resistance and wear resistance. High tensile strength and shear strength, good bonding performance
- Summary
- Abstract
- Description
- Claims
- Application Information
AI Technical Summary
Problems solved by technology
Method used
Image
Examples
example 1
[0022] Weigh 10g of molybdenum disulfide passed through a 200-mesh sieve, 3.0g of sodium cholate, add 2.0L of deionized water, and disperse in a 40°C constant temperature water bath for 6 hours with a 400W ultrasonic wave to obtain a molybdenum disulfide dispersion. Transfer the dispersion into a centrifuge, centrifuge at 3000r / min for 20min, collect the supernatant, and then centrifuge the supernatant at 12000r / min for 30min to obtain molybdenum disulfide with a two-dimensional layered structure. Molybdenum disulfide was added to 500mL deionized water, cleaned with 300W ultrasonic wave for 20 minutes, and then centrifuged at 12000r / min for 30 minutes to obtain a precipitate. Repeat the ultrasonic cleaning of the precipitate twice to obtain pretreated two-dimensional layered structure molybdenum disulfide. Measure 30mL of silane coupling agent KH-550, 150mL of absolute ethanol, add 0.6L of deionized water, and keep stirring and hydrolyzing at 300r / min for 8 hours in a constant ...
example 2
[0024] Weigh 11 molybdenum disulfide and 3.3 sodium cholate that have passed through a 200-mesh sieve, add 2.2 parts to deionized water, and disperse with 400W ultrasonic wave for 7 hours under a constant temperature water bath at 45°C to obtain a molybdenum disulfide dispersion. Dilute the molybdenum disulfide dispersion Transfer to a centrifuge, centrifuge at 3500r / min for 25min, collect the supernatant, and then centrifuge the supernatant at 12250r / min for 35min to obtain molybdenum disulfide with a two-dimensional layered structure. Molybdenum was added to 550mL deionized water, ultrasonically cleaned with 300W ultrasonic wave for 25min, and then centrifuged at 12250r / min for 35min to obtain a precipitate, and the precipitate was repeatedly ultrasonically cleaned twice to obtain pretreated two-dimensional layered molybdenum disulfide. Add 45mL of silane coupling agent KH-550 and 225mL of absolute ethanol to 0.9L of deionized water, and keep stirring and hydrolyzing at 350r / ...
example 3
[0026]Weigh 12g of molybdenum disulfide passed through a 200-mesh sieve, 3.6g of sodium cholate, add 2.4L of deionized water, and disperse with 400W ultrasonic wave for 8 hours under a constant temperature water bath at 50°C to obtain a molybdenum disulfide dispersion. Transfer the dispersion into a centrifuge, centrifuge at 4000r / min for 30min, collect the supernatant, and then centrifuge the supernatant at 12500r / min for 40min to obtain molybdenum disulfide with a two-dimensional layered structure. Molybdenum disulfide was added to 600mL deionized water, cleaned with 300W ultrasonic wave for 30 minutes, and then centrifuged at 12500r / min for 40 minutes to obtain a precipitate. Repeated ultrasonic cleaning of the precipitate three times to obtain pretreated two-dimensional layered structure molybdenum disulfide. Measure 60mL of silane coupling agent KH-550, 300mL of absolute ethanol, add 1.2L of deionized water, and keep stirring and hydrolyzing at 400r / min for 10h in a consta...
PUM
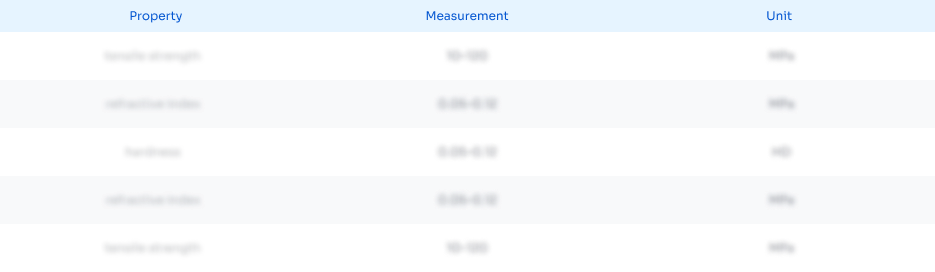
Abstract
Description
Claims
Application Information

- R&D
- Intellectual Property
- Life Sciences
- Materials
- Tech Scout
- Unparalleled Data Quality
- Higher Quality Content
- 60% Fewer Hallucinations
Browse by: Latest US Patents, China's latest patents, Technical Efficacy Thesaurus, Application Domain, Technology Topic, Popular Technical Reports.
© 2025 PatSnap. All rights reserved.Legal|Privacy policy|Modern Slavery Act Transparency Statement|Sitemap|About US| Contact US: help@patsnap.com